Induction heating design involves a systematic approach to ensure efficient and effective heating of materials. The design process must account for the characteristics of the material being heated, the properties of the induction coil, the power supply requirements, and the thermal dynamics of the system. Key elements include material selection, coil design, frequency selection, power supply capacity, and thermal management. Each of these factors influences the overall efficiency, heating rate, and temperature uniformity of the system. By carefully considering these elements, designers can optimize the induction heating process for specific applications.
Key Points Explained:
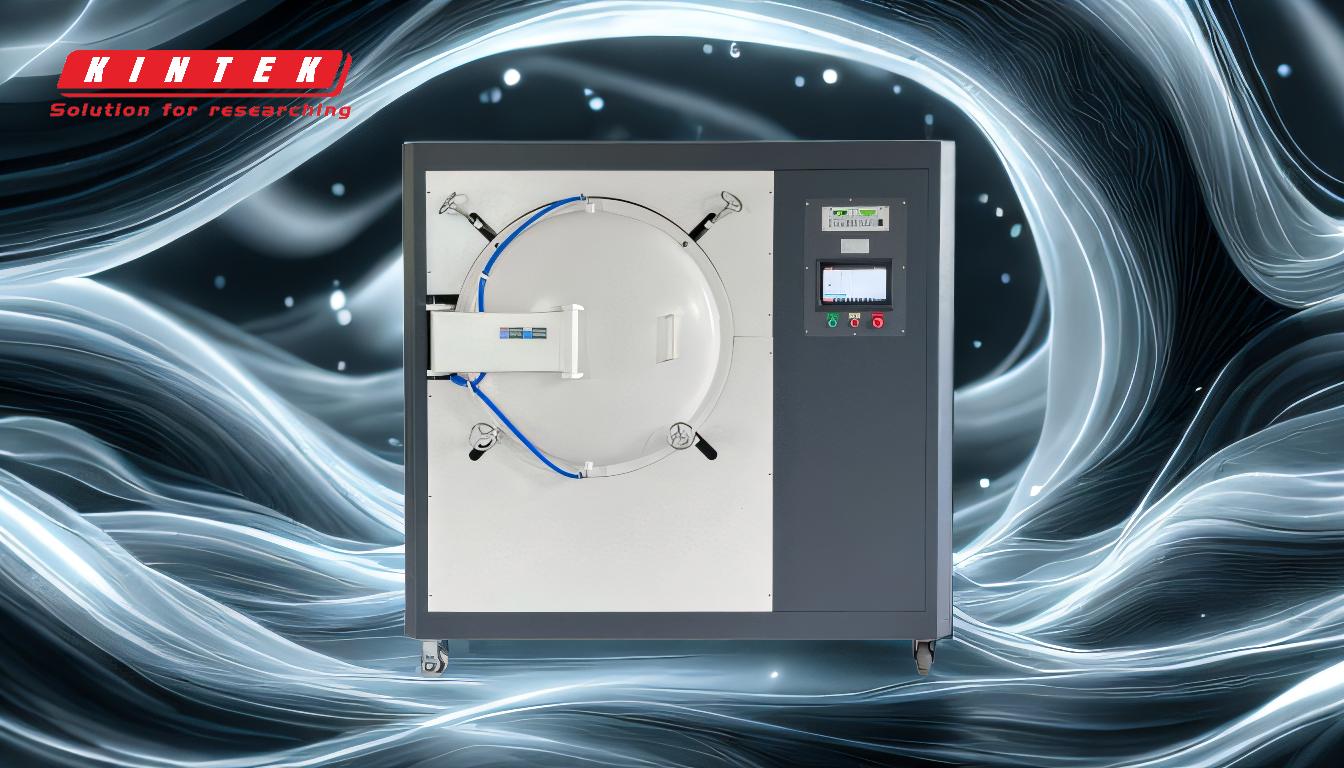
-
Material Characteristics:
- Type of Material: Induction heating is most effective with conductive materials, particularly metals. Magnetic materials heat due to hysteresis losses, while non-magnetic conductive materials heat due to eddy currents.
- Size and Thickness: Smaller and thinner materials heat faster because the induced currents can penetrate more effectively. Thicker materials may require lower frequencies to achieve deeper heating.
- Resistivity: Materials with higher resistivity heat more efficiently because they generate more heat from the same induced current.
-
Inductor Coil Design:
- Coil Geometry: The shape and size of the inductor coil must match the geometry of the workpiece to ensure uniform heating. Custom coils may be required for complex shapes.
- Coil Material: The coil itself must be made of a material that can withstand high temperatures and resist wear from repeated heating cycles.
- Cooling Requirements: The coil often requires cooling (e.g., water cooling) to prevent overheating and maintain efficiency.
-
Frequency Selection:
- Heating Depth: Higher frequencies result in shallower heating depths, making them suitable for surface heating or thin materials. Lower frequencies are better for deeper penetration in thicker materials.
- Application-Specific Frequencies: The choice of frequency depends on the material properties and the desired heating profile. For example, high frequencies are used for localized heating, while low frequencies are used for bulk heating.
-
Power Supply Capacity:
- Power Requirements: The power supply must provide sufficient energy to achieve the required temperature rise in the material. This depends on the material's specific heat, mass, and the desired temperature change.
- Efficiency Considerations: The power supply should be efficient to minimize energy losses and reduce operating costs. It must also handle the thermal load without overheating.
-
Thermal Management:
- Heat Loss Mechanisms: Heat can be lost through conduction, convection, and radiation. The system design must account for these losses to ensure accurate temperature control.
- Cooling Systems: In some cases, additional cooling systems (e.g., chillers) may be required to manage heat dissipation and maintain system stability.
-
System Components:
- Chiller: Used to cool the induction coil and other components to prevent overheating and maintain efficiency.
- Power Unit: Provides the necessary electrical energy to the induction coil at the required frequency and power level.
- Vacuum Unit: In some applications, a vacuum environment may be required to prevent oxidation or other chemical reactions during heating.
-
Application-Specific Considerations:
- Temperature Range: The system must be designed to accommodate the required temperature range for the application. Higher temperatures may require more powerful systems and better thermal management.
- Heating Uniformity: Ensuring uniform heating across the workpiece is critical for applications requiring precise temperature control, such as in metallurgical processes.
By addressing these elements systematically, designers can create induction heating systems tailored to specific applications, ensuring optimal performance and efficiency.
Summary Table:
Key Element | Description |
---|---|
Material Characteristics | - Type: Conductive materials (metals) work best. |
- Size/Thickness: Smaller/thinner materials heat faster. | |
- Resistivity: Higher resistivity materials heat more efficiently. | |
Inductor Coil Design | - Geometry: Matches workpiece shape for uniform heating. |
- Material: Must withstand high temperatures. | |
- Cooling: Often requires water cooling to prevent overheating. | |
Frequency Selection | - Higher frequencies: Shallow heating for thin materials. |
- Lower frequencies: Deeper penetration for thicker materials. | |
Power Supply Capacity | - Must provide sufficient energy for desired temperature rise. |
- Efficiency: Minimizes energy losses and operating costs. | |
Thermal Management | - Accounts for heat loss (conduction, convection, radiation). |
- May require additional cooling systems (e.g., chillers). | |
System Components | - Chiller: Cools induction coil and components. |
- Power Unit: Provides electrical energy at required frequency and power. | |
- Vacuum Unit: Prevents oxidation in some applications. | |
Application-Specific | - Temperature Range: Must accommodate required application temperatures. |
- Heating Uniformity: Critical for precise temperature control. |
Ready to design your induction heating system? Contact our experts today for tailored solutions!