Sintering is a critical process in materials science, where powdered materials are compacted and heated to form a solid structure. The quality and properties of the sintered product are influenced by several key factors, including temperature, sintering time, pressure, atmosphere, particle size, and composition. Each of these factors plays a significant role in determining the sintering kinetics, densification, and final material properties. For example, higher temperatures can enhance tensile strength and impact energy, while smaller particle sizes and homogeneous compositions promote better densification. Additionally, the sintering atmosphere, whether it be air, vacuum, or inert gases, can significantly affect the outcome. Understanding these factors is essential for optimizing the sintering process to achieve desired material properties.
Key Points Explained:
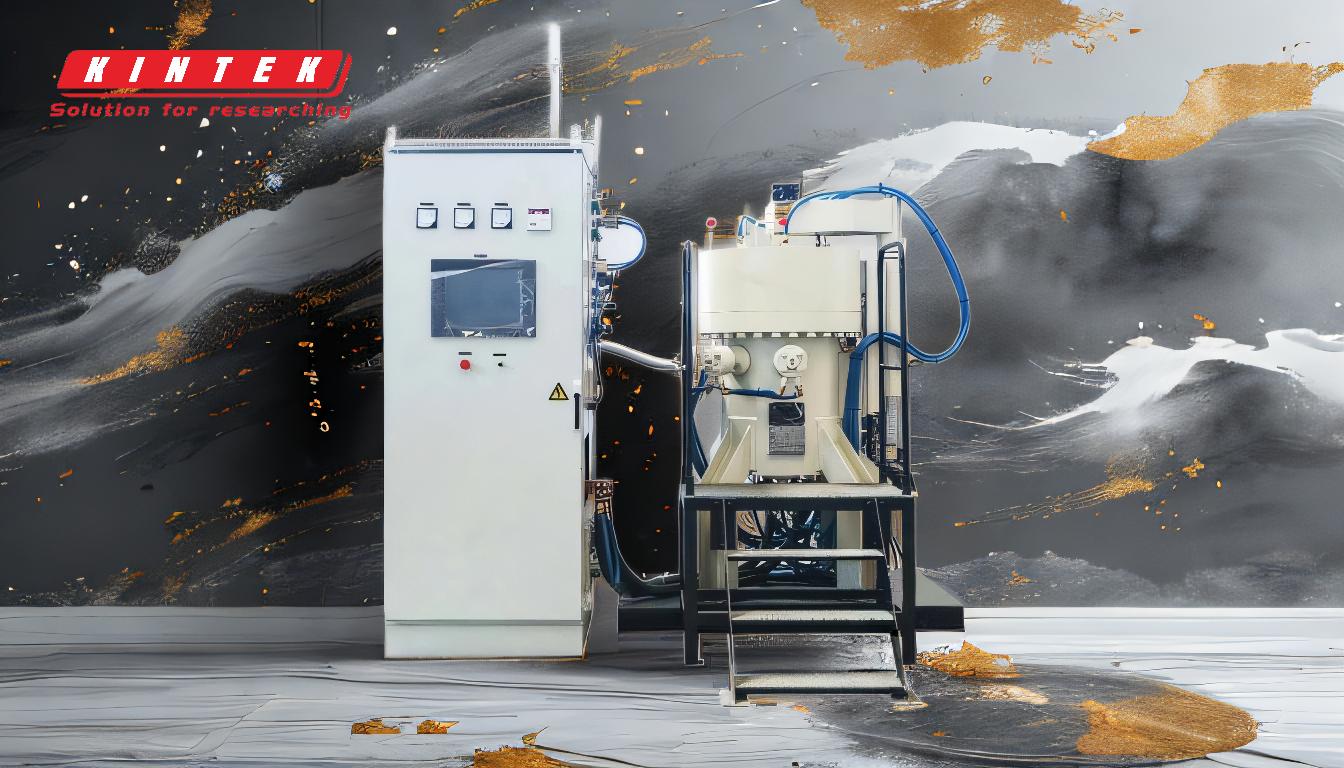
-
Temperature:
- Role in Sintering: Temperature is one of the most critical factors in sintering. It directly influences the sintering kinetics, which governs the rate at which particles bond and densify. Higher temperatures generally increase the mobility of atoms, leading to faster diffusion and better particle bonding.
- Impact on Material Properties: Elevated temperatures can enhance the mechanical properties of the sintered product, such as tensile strength, bending fatigue strength, and impact energy. However, excessively high temperatures can lead to undesirable grain growth or phase transformations, which may degrade material properties.
-
Sintering Time:
- Effect on Densification: The duration of the sintering process affects the extent of densification. Longer sintering times allow for more complete particle bonding and pore elimination, leading to higher density and improved mechanical properties.
- Trade-offs: While longer sintering times can improve densification, they also increase the risk of grain growth and may lead to energy inefficiency. Therefore, sintering time must be optimized to balance densification and energy consumption.
-
Pressure:
- Role in Particle Rearrangement: Applied pressure during sintering helps in the rearrangement of particles, reducing porosity and enhancing densification. Pressure can also facilitate the elimination of voids and improve the uniformity of the sintered product.
- Impact on Final Properties: Higher pressures generally lead to better densification and improved mechanical properties. However, the application of pressure must be carefully controlled to avoid deformation or cracking of the material.
-
Atmosphere:
- Types of Atmospheres: The sintering atmosphere can be air, vacuum, or inert gases like argon or nitrogen. Each atmosphere has different effects on the sintering process.
- Influence on Sintering: The choice of atmosphere can affect oxidation, reduction, or contamination of the material. For example, a vacuum or inert atmosphere can prevent oxidation, which is crucial for materials that are sensitive to oxygen. The atmosphere also influences the thermal conductivity and heat transfer during sintering.
-
Particle Size:
- Effect on Sintering Behavior: Smaller particle sizes have a higher surface area to volume ratio, which promotes faster diffusion and better densification. Smaller particles also tend to sinter at lower temperatures compared to larger particles.
- Impact on Final Properties: Finer powders generally result in a more homogeneous microstructure and improved mechanical properties. However, very fine particles can be challenging to handle and may require special processing techniques.
-
Composition:
- Role in Sintering: The chemical composition of the powder mixture affects the sintering behavior. Homogeneous compositions tend to sinter more uniformly, leading to better densification and fewer defects.
- Impact on Material Properties: The composition determines the final phase and microstructure of the sintered product. Alloying elements or additives can be used to tailor the properties of the sintered material, such as hardness, toughness, or thermal conductivity.
-
Heating Rate:
- Effect on Densification: The rate at which the material is heated can influence the sintering process. A slower heating rate allows for more uniform heat distribution and can reduce thermal stresses, leading to better densification.
- Impact on Microstructure: Rapid heating rates can lead to uneven sintering and may cause defects such as cracks or voids. Therefore, the heating rate must be carefully controlled to achieve the desired microstructure and properties.
-
Cooling Rate:
- Effect on Final Properties: The rate at which the sintered product is cooled can affect the final microstructure and properties. Slow cooling rates can lead to grain growth and phase transformations, while rapid cooling can result in a finer microstructure and improved mechanical properties.
- Trade-offs: The cooling rate must be optimized to balance the desired microstructure and properties. Rapid cooling may be beneficial for certain materials, but it can also introduce residual stresses.
-
Layer Thickness and Machine Speed:
- Role in Industrial Sintering: In industrial sintering processes, factors such as layer thickness and machine speed are controlled to ensure consistent quality. The layer thickness affects the heat distribution and sintering kinetics, while the machine speed determines the sintering time and endpoint.
- Impact on Sintering Quality: Proper control of these parameters is essential to achieve uniform sintering and avoid defects. For example, a layer thickness of 250-500mm and a machine speed of 1.5-4m/min are typical values used in industrial sintering processes.
-
Gaseous Atmosphere and Vacuum:
- Influence on Sintering: The gaseous atmosphere and vacuum level can significantly affect the sintering process. A vacuum or inert atmosphere can prevent oxidation and contamination, while a controlled gaseous atmosphere can be used to achieve specific reactions or phase transformations.
- Impact on Material Properties: The choice of atmosphere can influence the final properties of the sintered product, such as density, porosity, and mechanical strength. Therefore, the atmosphere must be carefully selected based on the material and desired properties.
In summary, the sintering process is influenced by a complex interplay of factors, each of which must be carefully controlled to achieve the desired material properties. Understanding these factors and their interactions is essential for optimizing the sintering process and producing high-quality sintered products.
Summary Table:
Factor | Role in Sintering | Impact on Material Properties |
---|---|---|
Temperature | Governs sintering kinetics; higher temps enhance diffusion and bonding. | Improves tensile strength, bending fatigue strength, and impact energy. |
Sintering Time | Longer times improve densification but risk grain growth. | Enhances density and mechanical properties; trade-off with energy efficiency. |
Pressure | Facilitates particle rearrangement and porosity reduction. | Higher pressures lead to better densification and uniformity. |
Atmosphere | Air, vacuum, or inert gases affect oxidation, reduction, and contamination. | Prevents oxidation; influences thermal conductivity and material integrity. |
Particle Size | Smaller particles sinter faster and at lower temps; higher surface area improves bonding. | Finer powders yield homogeneous microstructures and better mechanical properties. |
Composition | Homogeneous mixtures sinter uniformly; additives tailor properties. | Determines final phase, microstructure, and properties like hardness and toughness. |
Heating Rate | Slower rates ensure uniform heat distribution and reduce thermal stress. | Rapid heating may cause defects; controlled rates improve densification. |
Cooling Rate | Affects microstructure; slow cooling may cause grain growth, while rapid cooling refines it. | Rapid cooling enhances mechanical properties but may introduce residual stresses. |
Layer Thickness | Influences heat distribution and sintering kinetics in industrial processes. | Proper control ensures uniform sintering and avoids defects. |
Gaseous Atmosphere | Vacuum or inert gases prevent oxidation; controlled atmospheres enable specific reactions. | Impacts density, porosity, and mechanical strength of the sintered product. |
Ready to optimize your sintering process? Contact our experts today for tailored solutions!