The heat produced in a heating element depends on several key factors, including the electrical current passing through it, the resistance of the heating element material, and the duration of energy utilization. Additionally, the material properties of the heating element, such as its coefficient of electrical resistance, temperature tolerance, and reactivity to environmental factors like oxygen, play a significant role in determining heat generation. The choice of material is also influenced by the specific application, working temperature, and furnace atmosphere, which can affect the element's performance and reliability.
Key Points Explained:
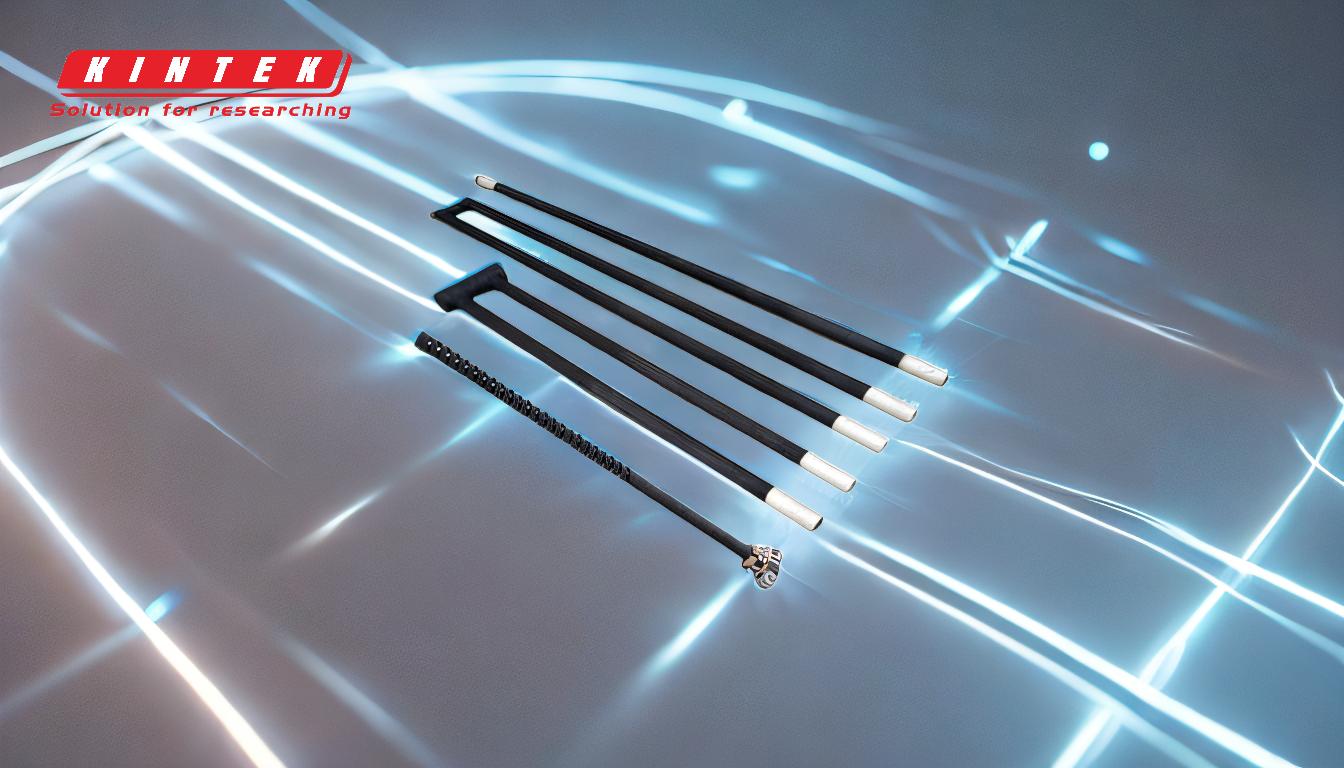
-
Electric Current (I):
- The amount of heat produced in a heating element is directly proportional to the square of the electric current passing through it (I²). This relationship is derived from Joule's law, which states that the heat generated (H) is given by H = I²Rt, where R is the resistance and t is the time.
- Higher current increases the energy dissipated as heat, making it a critical factor in heat generation.
-
Resistance of the Heating Element (R):
- The intrinsic resistive properties of the heating element material determine its ability to convert electrical energy into heat. Materials with higher resistance generate more heat for a given current.
- The coefficient of electrical resistance of the material plays a significant role in heat production. For example, materials like ferrochromium-aluminum or silicon carbide are chosen for their specific resistive properties and temperature tolerance.
-
Time (t):
- The duration for which the current flows through the heating element affects the total heat produced. Longer durations result in greater heat generation, as heat accumulates over time.
-
Material Properties:
- Temperature Ratings: The material must withstand the operating temperature without degrading. For instance, ferrochromium-aluminum wires are suitable for temperatures up to 1200°C, while silicon carbide bars can handle up to 1400°C.
- Reactivity to Oxygen: Some materials, like silicon carbide, can tolerate high temperatures in the presence of oxygen, while others may require protective atmospheres to prevent oxidation.
- Uniform Heating and Temperature Uniformity: The material should ensure even heat distribution across the workload, which is crucial for consistent process results.
-
Application-Specific Factors:
- Furnace Atmosphere: The type of atmosphere (e.g., endo gas, low-pressure carburizing) influences the choice of heating element. Some materials perform better in specific atmospheres, ensuring reliable performance.
- Cost and Suitability: The material must balance cost-effectiveness with the requirements of the application, such as thermal efficiency and durability.
-
Environmental and Operational Constraints:
- The availability of natural gas or other energy sources can influence the choice of heating elements.
- The design of the heating element must account for the specific operational conditions, such as the need for rapid heating or maintaining tight temperature control.
By considering these factors, one can select the appropriate heating element material and design to achieve optimal heat generation and performance for a given application.
Summary Table:
Factor | Impact on Heat Production |
---|---|
Electric Current (I) | Heat is proportional to I²; higher current increases heat generation. |
Resistance (R) | Higher resistance materials generate more heat for a given current. |
Time (t) | Longer durations result in greater heat accumulation. |
Material Properties | Temperature tolerance, reactivity to oxygen, and uniform heating are critical. |
Application-Specific | Furnace atmosphere, cost, and suitability influence material choice. |
Operational Constraints | Energy source availability and design requirements affect performance. |
Need help selecting the right heating element for your application? Contact our experts today!