Sintering is a critical process in materials science and manufacturing, where powdered materials are heated to form a solid mass without melting. The process is influenced by a variety of factors, including temperature, sintering time, pressure, atmospheric composition, particle size, and cooling rate. These factors collectively determine the final properties of the sintered product, such as density, strength, and microstructure. Understanding and controlling these variables is essential for optimizing the sintering process to achieve desired material properties and product performance.
Key Points Explained:
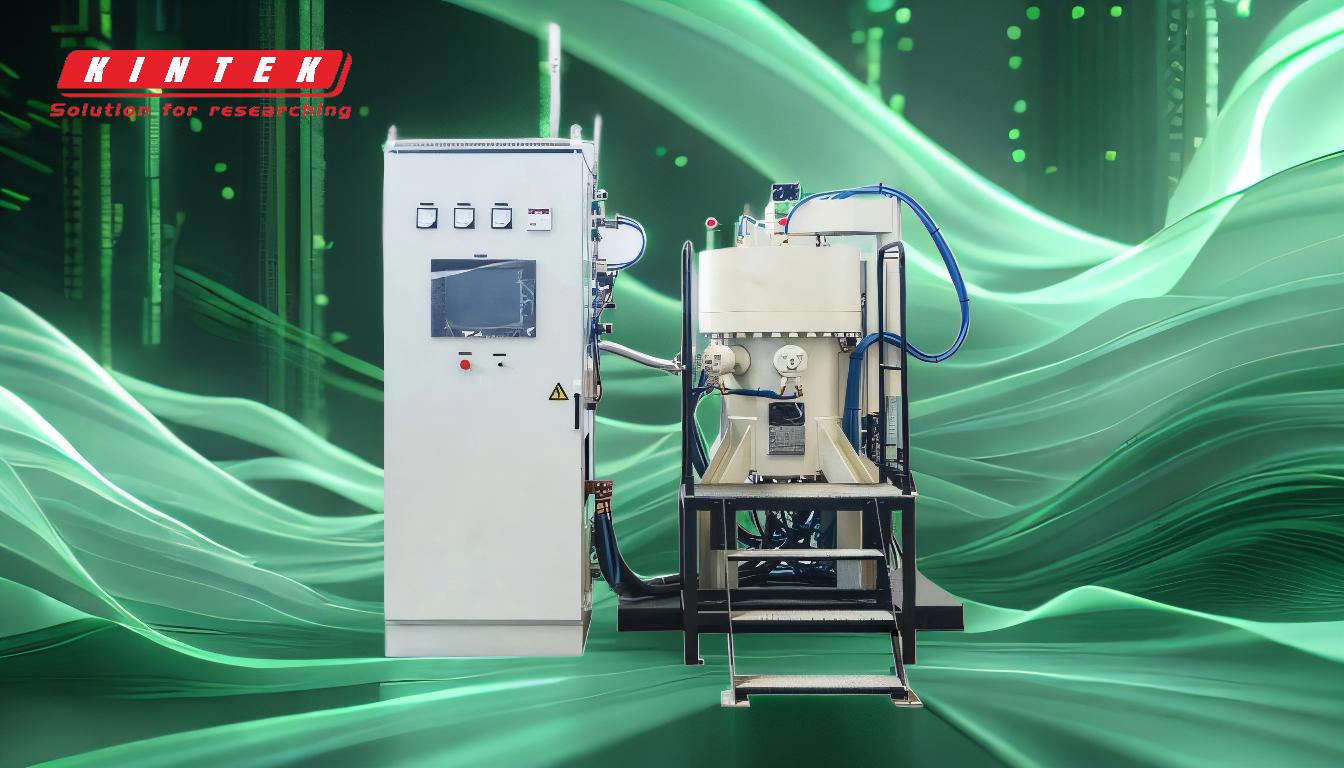
-
Temperature:
- Role: Temperature is one of the most critical factors in sintering. It directly influences the kinetics of the sintering process, including diffusion rates and grain growth.
- Impact: Higher temperatures generally increase the rate of densification and can improve mechanical properties such as tensile strength, bending fatigue strength, and impact energy. However, excessively high temperatures can lead to undesirable grain growth or melting.
- Control: The optimal sintering temperature depends on the material being sintered and the desired properties. It must be carefully controlled to balance densification and grain growth.
-
Sintering Time:
- Role: The duration of the sintering process affects the extent of densification and grain growth.
- Impact: Longer sintering times can lead to greater densification but may also result in excessive grain growth, which can degrade mechanical properties.
- Control: Sintering time should be optimized to achieve the desired density and microstructure without over-sintering.
-
Pressure:
- Role: Applied pressure during sintering can enhance particle rearrangement and eliminate porosity.
- Impact: Higher pressures can lead to faster densification and improved mechanical properties. However, excessive pressure can cause deformation or cracking.
- Control: The amount of pressure applied must be carefully controlled based on the material and the desired outcome.
-
Atmospheric Composition:
- Role: The atmosphere in which sintering occurs (e.g., air, vacuum, argon, nitrogen) can influence the sintering process by affecting oxidation, reduction, or other chemical reactions.
- Impact: For example, a vacuum or inert atmosphere can prevent oxidation, which is crucial for sintering certain metals. The choice of atmosphere can also affect the final properties of the sintered product.
- Control: The atmosphere must be selected based on the material and the desired properties, with careful control of gas composition and flow rates.
-
Particle Size:
- Role: The size of the particles being sintered affects the surface area and the driving force for sintering.
- Impact: Smaller particles have a higher surface area, which promotes faster densification. However, very fine particles can lead to excessive grain growth or agglomeration.
- Control: The particle size distribution should be optimized to achieve uniform densification and control grain growth.
-
Cooling Rate:
- Role: The rate at which the sintered product is cooled can affect the microstructure and residual stresses.
- Impact: Rapid cooling can lead to a finer microstructure but may also introduce residual stresses. Slow cooling can reduce stresses but may result in coarser grains.
- Control: The cooling rate should be tailored to the material and the desired properties, often involving a controlled cooling cycle.
-
Heating Rate:
- Role: The rate at which the material is heated to the sintering temperature can influence the densification process.
- Impact: A faster heating rate can lead to more rapid densification but may also cause thermal gradients that lead to cracking or warping.
- Control: The heating rate must be carefully controlled to ensure uniform heating and avoid thermal stresses.
-
Composition:
- Role: The chemical composition of the material being sintered affects its sintering behavior and final properties.
- Impact: Homogeneous compositions generally promote better densification, while impurities or inhomogeneities can lead to defects or uneven sintering.
- Control: The composition should be carefully controlled to ensure consistent sintering behavior and desired material properties.
-
Layer Thickness and Machine Speed:
- Role: In some sintering processes, such as those involving sintering ore, the layer thickness and machine speed are critical parameters.
- Impact: Thicker layers or slower machine speeds can lead to incomplete sintering, while thinner layers or faster speeds may result in uneven sintering.
- Control: These parameters must be optimized to ensure that the sintering feed is burned uniformly and reaches the scheduled endpoint.
-
Air Volume and Vacuum:
- Role: In certain sintering processes, the air volume and vacuum level are important factors.
- Impact: Proper air volume ensures adequate oxygen supply for combustion, while the right vacuum level helps in controlling the sintering atmosphere.
- Control: These parameters are typically controlled based on the specific requirements of the sintering process and the material being sintered.
In summary, sintering is a multifaceted process influenced by a wide range of factors. Each of these factors must be carefully controlled and optimized to achieve the desired properties in the final sintered product. Understanding the interplay between these variables is crucial for anyone involved in the design or optimization of sintering processes.
Summary Table:
Factor | Role | Impact | Control |
---|---|---|---|
Temperature | Influences diffusion rates and grain growth | Higher temperatures increase densification but may cause grain growth or melting | Optimize based on material and desired properties |
Sintering Time | Affects densification and grain growth | Longer times increase densification but may lead to excessive grain growth | Balance time to achieve desired density without over-sintering |
Pressure | Enhances particle rearrangement and reduces porosity | Higher pressures improve densification but can cause deformation | Apply controlled pressure based on material and outcome |
Atmospheric Composition | Affects oxidation, reduction, and chemical reactions | Inert atmospheres prevent oxidation; choice impacts final properties | Select and control atmosphere based on material and desired properties |
Particle Size | Influences surface area and driving force for sintering | Smaller particles densify faster but may lead to excessive grain growth | Optimize particle size distribution for uniform densification |
Cooling Rate | Affects microstructure and residual stresses | Rapid cooling creates finer microstructures but may introduce stresses | Tailor cooling rate to material and desired properties |
Heating Rate | Influences densification and thermal gradients | Faster heating densifies quickly but may cause cracking or warping | Control heating rate for uniform heating |
Composition | Determines sintering behavior and final properties | Homogeneous compositions promote better densification; impurities cause defects | Ensure consistent composition for desired properties |
Layer Thickness/Machine Speed | Affects uniformity of sintering in ore processes | Thicker layers or slower speeds may lead to incomplete sintering | Optimize parameters for uniform sintering |
Air Volume/Vacuum | Ensures oxygen supply and controls sintering atmosphere | Proper air volume supports combustion; vacuum prevents oxidation | Adjust based on process and material requirements |
Need help optimizing your sintering process? Contact our experts today for tailored solutions!