Hydraulic systems generate heat during operation due to friction, fluid compression, and energy losses. Effective cooling is essential to maintain system efficiency, prevent overheating, and extend the lifespan of components. There are several methods to cool hydraulic systems, including air cooling, water cooling, and the use of heat exchangers. Each method has its advantages and is chosen based on factors such as system size, operating environment, and heat load. Proper cooling ensures stable performance and prevents damage to hydraulic components.
Key Points Explained:
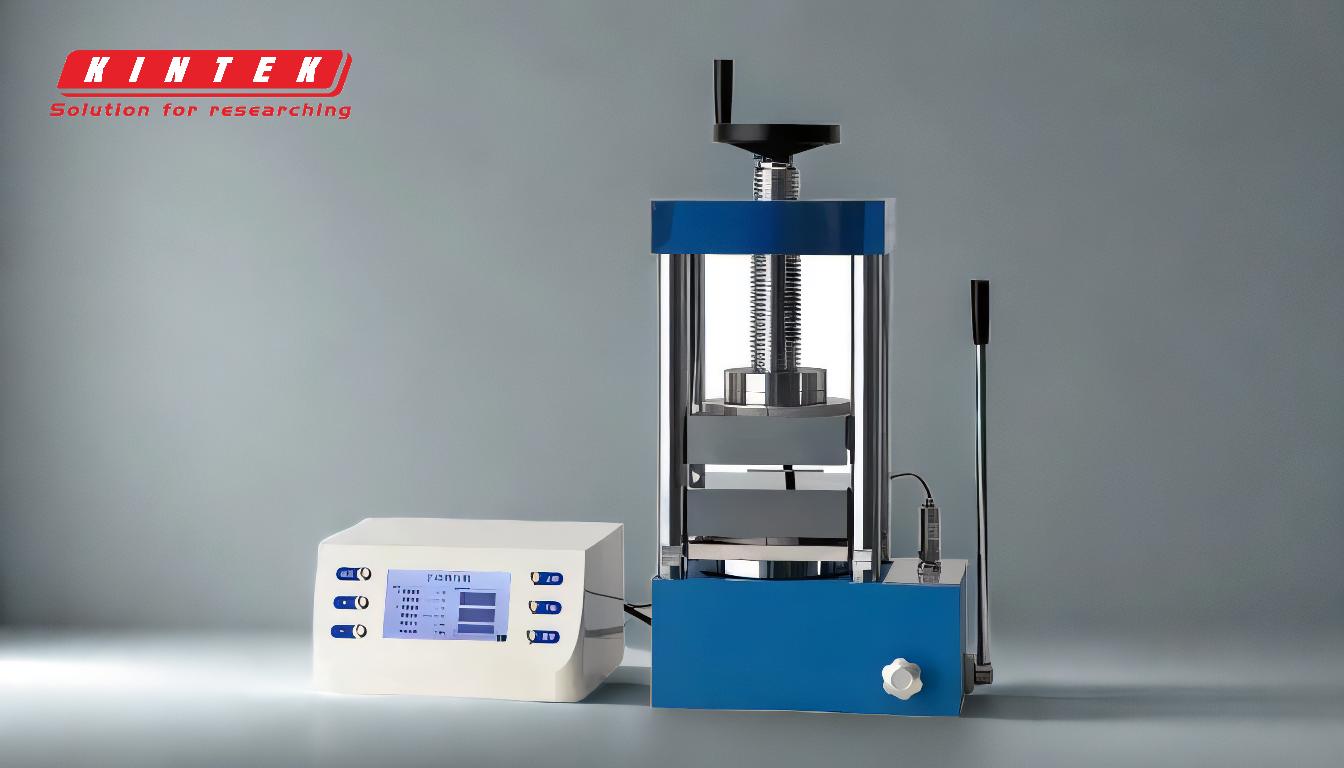
-
Air Cooling
- Air cooling is one of the most common and cost-effective methods for cooling hydraulic systems.
- It uses fans or blowers to dissipate heat from the hydraulic fluid by passing air over a heat exchanger or radiator.
- This method is suitable for smaller systems or environments where water cooling is impractical.
- Advantages include simplicity, low maintenance, and no need for additional water supply.
- However, air cooling may be less effective in high-temperature environments or for systems with large heat loads.
-
Water Cooling
- Water cooling involves circulating water through a heat exchanger to absorb heat from the hydraulic fluid.
- This method is highly efficient and is often used in large hydraulic systems or applications with high heat generation.
- Water cooling can handle higher heat loads compared to air cooling and is effective in maintaining consistent temperatures.
- However, it requires a reliable water supply and proper filtration to prevent contamination.
- Maintenance is also more complex due to the need to manage water quality and prevent corrosion.
-
Heat Exchangers
- Heat exchangers are devices designed to transfer heat from the hydraulic fluid to a cooling medium, such as air or water.
- Common types include shell-and-tube heat exchangers, plate heat exchangers, and finned-tube heat exchangers.
- Heat exchangers are highly efficient and can be customized to meet specific cooling requirements.
- They are often used in industrial applications where precise temperature control is needed.
- Regular maintenance is required to ensure optimal performance and prevent fouling or blockages.
-
Oil Cooling Systems
- Some hydraulic systems use dedicated oil cooling systems, where the hydraulic fluid is circulated through a separate cooling unit.
- These systems often include pumps, filters, and cooling fans to maintain fluid temperature within a safe range.
- Oil cooling is particularly useful in high-performance or heavy-duty applications.
- It provides consistent cooling and can be integrated with other cooling methods for enhanced efficiency.
- However, it adds complexity and cost to the hydraulic system.
-
Thermostatic Control
- Thermostatic control systems regulate the temperature of the hydraulic fluid by adjusting the cooling process based on real-time temperature readings.
- This ensures that the system operates within the optimal temperature range, improving efficiency and reducing wear.
- Thermostatic valves can be used to control the flow of cooling medium (air or water) based on system requirements.
- This method is particularly useful in applications with variable heat loads or operating conditions.
-
Environmental Considerations
- The choice of cooling method should consider the operating environment and available resources.
- For example, in areas with limited water supply, air cooling or oil cooling systems may be preferred.
- In high-temperature environments, water cooling or advanced heat exchangers may be necessary to ensure adequate cooling.
- Proper insulation and ventilation can also help improve cooling efficiency and reduce energy consumption.
By selecting the appropriate cooling method and maintaining the system properly, hydraulic systems can operate efficiently and reliably, even under demanding conditions. Regular monitoring and maintenance are essential to ensure the cooling system functions effectively and prevents overheating.
Summary Table:
Method | Description | Advantages | Limitations |
---|---|---|---|
Air Cooling | Uses fans or blowers to dissipate heat via air passing over a heat exchanger. | Cost-effective, low maintenance, no water supply needed. | Less effective in high-temperature environments or for large heat loads. |
Water Cooling | Circulates water through a heat exchanger to absorb heat from hydraulic fluid. | Highly efficient, handles high heat loads, maintains consistent temperatures. | Requires water supply, complex maintenance, risk of contamination and corrosion. |
Heat Exchangers | Transfers heat from hydraulic fluid to a cooling medium (air or water). | Highly efficient, customizable, precise temperature control. | Requires regular maintenance to prevent fouling or blockages. |
Oil Cooling | Uses a dedicated cooling unit to circulate and cool hydraulic fluid. | Consistent cooling, suitable for high-performance applications. | Adds complexity and cost to the system. |
Thermostatic Control | Regulates cooling based on real-time temperature readings. | Improves efficiency, reduces wear, adapts to variable heat loads. | Requires advanced components and monitoring. |
Need help choosing the right cooling method for your hydraulic system? Contact our experts today for tailored solutions!