Sintering is a critical process in manufacturing that transforms powdered materials into dense, durable, and functional components. The primary objectives of sintering include enhancing material properties such as strength, durability, and density by bonding particles at high temperatures below the material's melting point. This process also eliminates pores, reduces volume, and improves mechanical properties, making it essential for producing a wide range of industrial products like gears, bearings, and electrical contacts. Sintering is cost-effective, versatile, and allows for precise control over material characteristics, making it indispensable in modern manufacturing.
Key Points Explained:
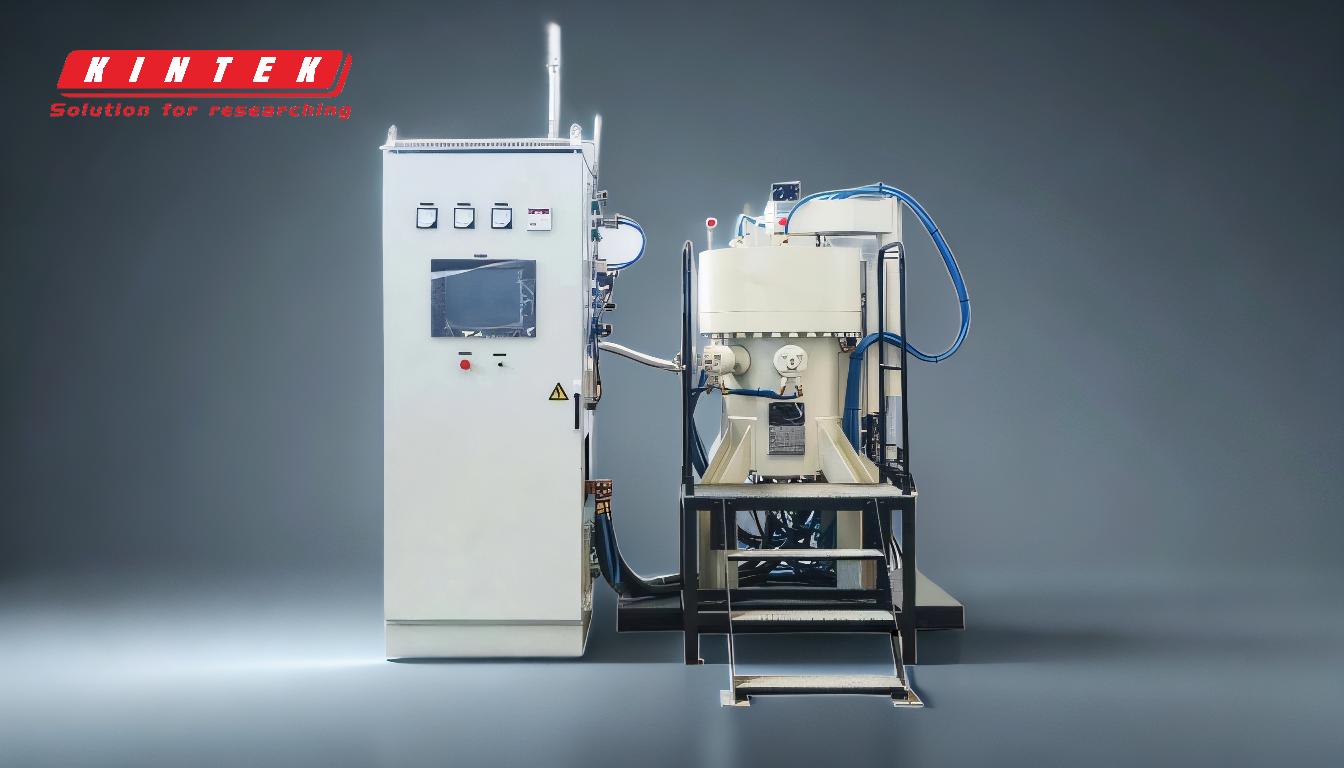
-
Transformation of Powdered Material into a Dense Body
- Sintering compacts powdered materials into a solid, dense mass by applying high heat and pressure.
- The process forces atoms into tighter bonds, resulting in a stronger and more durable product.
- This transformation is achieved without melting the material, making it energy-efficient and cost-effective.
-
Enhancement of Material Properties
- Sintering improves mechanical properties such as strength, hardness, and durability.
- The process reduces porosity, leading to increased density and better structural integrity.
- By controlling the sintering temperature and atmosphere, manufacturers can fine-tune the material's characteristics to meet specific requirements.
-
Bonding of Particles and Grain Growth
- During sintering, solid particles bond together, and grains grow, leading to a reduction in voids and grain boundaries.
- This bonding process results in a polycrystalline sintered body with a specific microstructure, which is crucial for the material's performance.
- The elimination of pores and grain boundaries enhances the material's overall quality and functionality.
-
Volume Shrinkage and Dimensional Control
- Sintering causes minor shrinkage, which is accounted for during the compaction stage to achieve the final dimensions of the part.
- The controlled shrinkage ensures precision in manufacturing, making sintering ideal for producing components with tight tolerances.
- Adjusting the cooling rate further allows for fine-tuning the part's properties and dimensions.
-
Cost-Effectiveness and Versatility
- Sintering is a cost-effective method for producing high-quality components without the need for melting.
- Its versatility makes it suitable for a wide range of industries, including automotive, aerospace, electronics, and machinery.
- Common products include gears, bearings, pulleys, rotors, and electrical contacts, showcasing the process's adaptability.
-
Controlled Atmosphere and Temperature
- Sintering is performed in a controlled atmosphere furnace to ensure proper bonding and prevent oxidation or contamination.
- The temperature is maintained slightly below the material's melting point to achieve optimal results without compromising the material's integrity.
- This controlled environment is critical for achieving consistent and reliable outcomes.
-
Finalization of Mechanical Properties
- The sintering process gives the part its final mechanical properties, such as tensile strength, wear resistance, and fatigue life.
- By adjusting parameters like temperature, time, and cooling rate, manufacturers can tailor the material's properties to specific applications.
- This customization capability makes sintering a preferred method for producing high-performance components.
In summary, sintering is a vital manufacturing process that achieves multiple objectives, including densification, property enhancement, and dimensional control, while remaining cost-effective and versatile. Its ability to produce high-quality, durable components makes it indispensable across various industries.
Summary Table:
Key Objective | Description |
---|---|
Densification | Transforms powdered materials into a solid, dense mass without melting. |
Property Enhancement | Improves strength, hardness, and durability while reducing porosity. |
Dimensional Control | Ensures precision with controlled shrinkage and tight tolerances. |
Cost-Effectiveness | Produces high-quality components without melting, reducing energy costs. |
Versatility | Suitable for industries like automotive, aerospace, and electronics. |
Controlled Atmosphere | Prevents oxidation and contamination for consistent results. |
Customizable Properties | Tailors mechanical properties like wear resistance and fatigue life. |
Learn how sintering can optimize your manufacturing process—contact our experts today!