Heat treatment of steel is a critical process used to alter its physical and mechanical properties, such as hardness, toughness, ductility, and strength. The process involves three fundamental stages: heating, soaking, and cooling. Each stage plays a vital role in achieving the desired material properties. The heating stage raises the steel to a specific temperature, the soaking stage maintains this temperature to ensure uniform structural changes, and the cooling stage solidifies these changes. These stages can be tailored to achieve specific outcomes, such as annealing for softness or quenching for hardness. Understanding these stages is essential for optimizing steel's performance in various applications.
Key Points Explained:
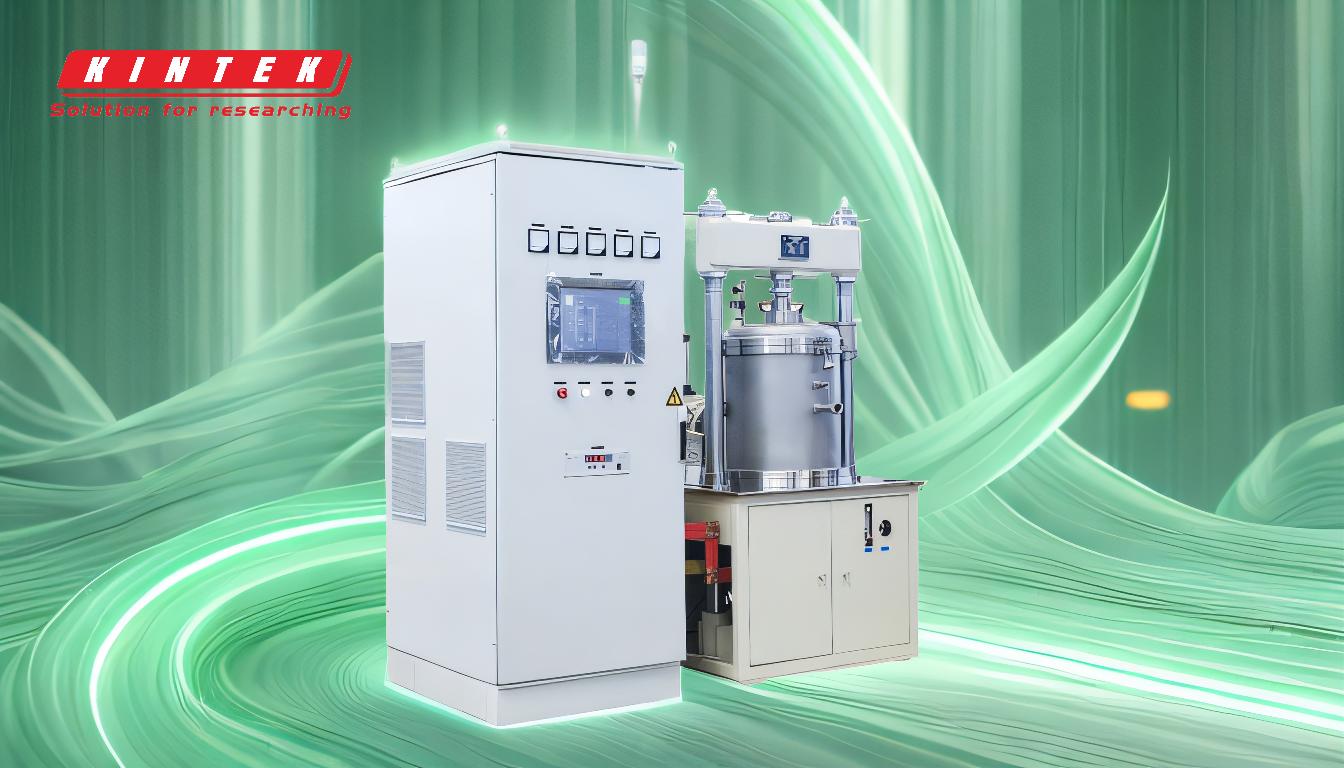
-
Heating Stage:
- The first stage involves heating the steel to a predetermined temperature, which can range from a few hundred degrees to as high as 2,400°F, depending on the desired outcome.
- Purpose: Heating ensures the steel reaches a temperature where its internal structure begins to change, making it more malleable or preparing it for further transformations.
- Considerations: The heating rate must be carefully controlled to avoid thermal stress, which can lead to warping or cracking. Uniform heating is critical to ensure consistent results.
-
Soaking Stage:
- Once the steel reaches the target temperature, it is held at that temperature for a specific duration, known as the soaking time.
- Purpose: Soaking allows the heat to penetrate uniformly throughout the material, ensuring that the entire workpiece undergoes the desired structural changes.
- Considerations: The soaking time can vary significantly, from a few seconds to several hours, depending on the steel's composition and the intended application. Proper soaking ensures homogeneity in the material's properties.
-
Cooling Stage:
- After soaking, the steel is cooled according to a prescribed method, which can involve rapid quenching, slow cooling in a furnace, or controlled cooling in air.
- Purpose: The cooling rate determines the final properties of the steel. Rapid cooling (quenching) typically increases hardness, while slower cooling (annealing) enhances ductility and reduces internal stresses.
- Considerations: The cooling method must be carefully selected to achieve the desired balance between hardness, toughness, and other properties. Improper cooling can lead to brittleness or residual stresses.
-
Types of Heat Treatment Processes:
- Annealing: Involves heating the steel to a specific temperature and then slowly cooling it to soften the material, improve ductility, and relieve internal stresses.
- Quenching: Rapidly cools the steel to increase hardness and strength, often followed by tempering to reduce brittleness.
- Tempering: Reheats quenched steel to a lower temperature to improve toughness and reduce brittleness while maintaining hardness.
- Case Hardening: Adds a hard surface layer to the steel while maintaining a softer, tougher core, enhancing wear resistance.
- Carburizing: Introduces carbon into the surface layer of the steel to increase surface hardness and wear resistance.
- Precipitation Hardening: Strengthens the steel by forming fine particles within the material, improving strength and hardness without significantly reducing ductility.
-
Applications and Considerations:
- Aerospace Industry: Heat treatment is crucial for components that require high strength-to-weight ratios and resistance to extreme conditions.
- Automotive Industry: Used to enhance the durability and performance of engine parts, gears, and suspension components.
- Tool Manufacturing: Heat treatment ensures tools have the necessary hardness and wear resistance for cutting, shaping, and forming operations.
- Customization: The heat treatment process can be tailored to meet specific requirements, such as localized hardening or stress relief in particular areas of a component.
By understanding and carefully controlling the stages of heat treatment, manufacturers can optimize the properties of steel for a wide range of applications, ensuring durability, performance, and longevity.
Summary Table:
Stage | Purpose | Key Considerations |
---|---|---|
Heating | Raise steel to a specific temperature for structural changes. | Control heating rate to avoid warping; ensure uniform heating for consistent results. |
Soaking | Maintain temperature for uniform heat penetration. | Soaking time varies based on steel composition and application requirements. |
Cooling | Solidify structural changes through controlled cooling methods. | Cooling rate determines final properties (e.g., hardness, toughness). |
Need expert guidance on heat treatment for your steel applications? Contact us today to optimize your process!