The Chemical Vapor Deposition (CVD) process is a sophisticated method used to deposit thin films onto substrates through chemical reactions in the vapor phase. It involves several critical steps, including the introduction of precursor gases into a reaction chamber, their interaction with a heated substrate, and the subsequent deposition of a solid material on the substrate surface. Key parameters such as temperature, pressure, and gas flow rates significantly influence the quality and characteristics of the deposited film. The process can be performed under various conditions, including atmospheric and low pressures, and often requires precise control to achieve desired film properties.
Key Points Explained:
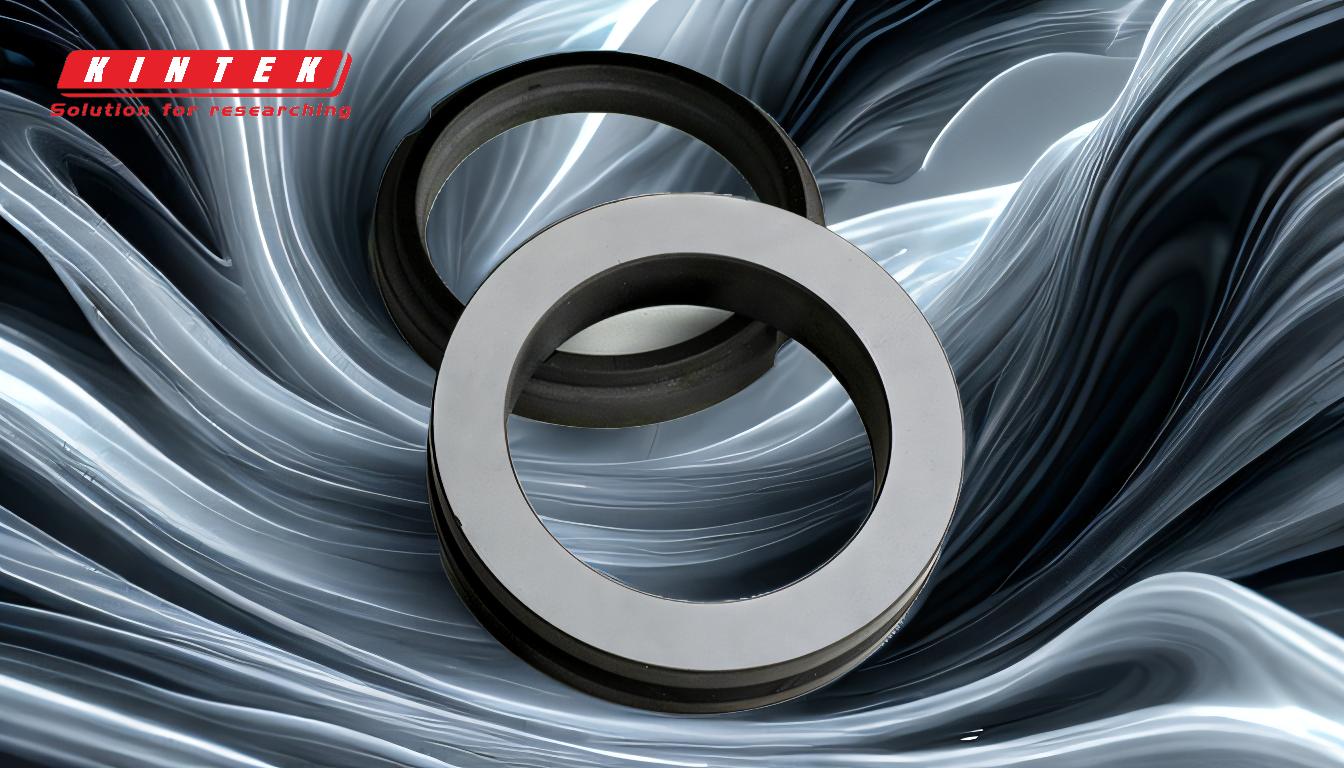
-
Introduction of Precursor Gases
- The CVD process begins with the introduction of precursor gases, often mixed with carrier gases, into a reaction chamber.
- These gases are typically volatile compounds of the material to be deposited.
- The flow rates of these gases are carefully controlled using flow regulators and valves to ensure precise deposition.
-
Transport of Gases to the Substrate
- The precursor gases are transported to the substrate surface, which is usually heated to a specific temperature.
- The temperature of the substrate plays a critical role in determining the type of chemical reaction that will occur.
- The gases pass through a boundary layer near the substrate surface, where they are adsorbed.
-
Surface Reactions and Decomposition
- On the heated substrate, the precursor gases undergo thermal decomposition or chemical reactions.
- These reactions break down the gases into atoms, molecules, or other reactive species.
- The reactions are often catalyzed by the substrate surface, especially in processes like graphene growth, where a metal catalyst (e.g., Cu, Pt, or Ir) is used.
-
Deposition of Thin Film
- The nonvolatile reaction products from the surface reactions deposit onto the substrate, forming a thin film.
- The film's structure, thickness, and morphology depend on parameters such as temperature, pressure, and gas flow rates.
- For example, in graphene growth, carbon-bearing gases decompose at high temperatures, and the carbon atoms nucleate on the metal catalyst to form a graphene lattice.
-
Desorption and Removal of By-products
- Gaseous by-products or unreacted gases are desorbed from the substrate surface.
- These by-products are then transported away from the reaction chamber through an exhausting system.
- This step ensures that the deposited film remains pure and free from contaminants.
-
Control of Environmental Conditions
- The CVD process often occurs under vacuum or controlled atmospheric conditions to prevent the inclusion of ambient components in the film.
- In some cases, plasma or light is used to induce chemical reactions at lower temperatures, enabling deposition on heat-sensitive substrates or in narrow grooves.
-
Applications and Variations
- CVD is widely used in the semiconductor industry to deposit thin films such as protective layers, wiring films, and insulating films on silicon wafers.
- The process is also employed in the production of advanced materials like graphene, where specific substrates and catalysts are used to achieve high-quality films.
- Variations of CVD, such as Plasma-Enhanced CVD (PECVD), allow for lower-temperature operations and greater control over film properties.
By following these steps and carefully controlling the process parameters, the CVD process enables the deposition of high-quality thin films with precise thicknesses and properties, making it a cornerstone of modern materials science and semiconductor manufacturing.
Summary Table:
Step | Description |
---|---|
1. Introduction of Precursor Gases | Precursor gases, often mixed with carrier gases, are introduced into the reaction chamber. |
2. Transport of Gases to Substrate | Gases are transported to the heated substrate, where they undergo adsorption. |
3. Surface Reactions & Decomposition | Gases decompose or react on the substrate, forming reactive species. |
4. Deposition of Thin Film | Nonvolatile reaction products deposit onto the substrate, forming a thin film. |
5. Desorption of By-products | Gaseous by-products are removed from the chamber to ensure film purity. |
6. Control of Environmental Conditions | Process occurs under vacuum or controlled conditions to prevent contamination. |
7. Applications & Variations | CVD is used in semiconductors and advanced materials like graphene. |
Ready to optimize your thin film deposition? Contact our experts today for tailored CVD solutions!