Extrusion is a manufacturing process that involves shaping material by forcing it through a die. The two basic types of extrusion are hot extrusion and cold extrusion , each with distinct characteristics, applications, and advantages. Hot extrusion is performed at elevated temperatures, making the material easier to shape, and is commonly used for producing automotive and aerospace components. Cold extrusion, on the other hand, is conducted at or near room temperature, resulting in stronger finished products, and is often used for manufacturing fasteners and precision automotive parts. Below, we explore these two types in detail, focusing on their processes, applications, and benefits.
Key Points Explained:
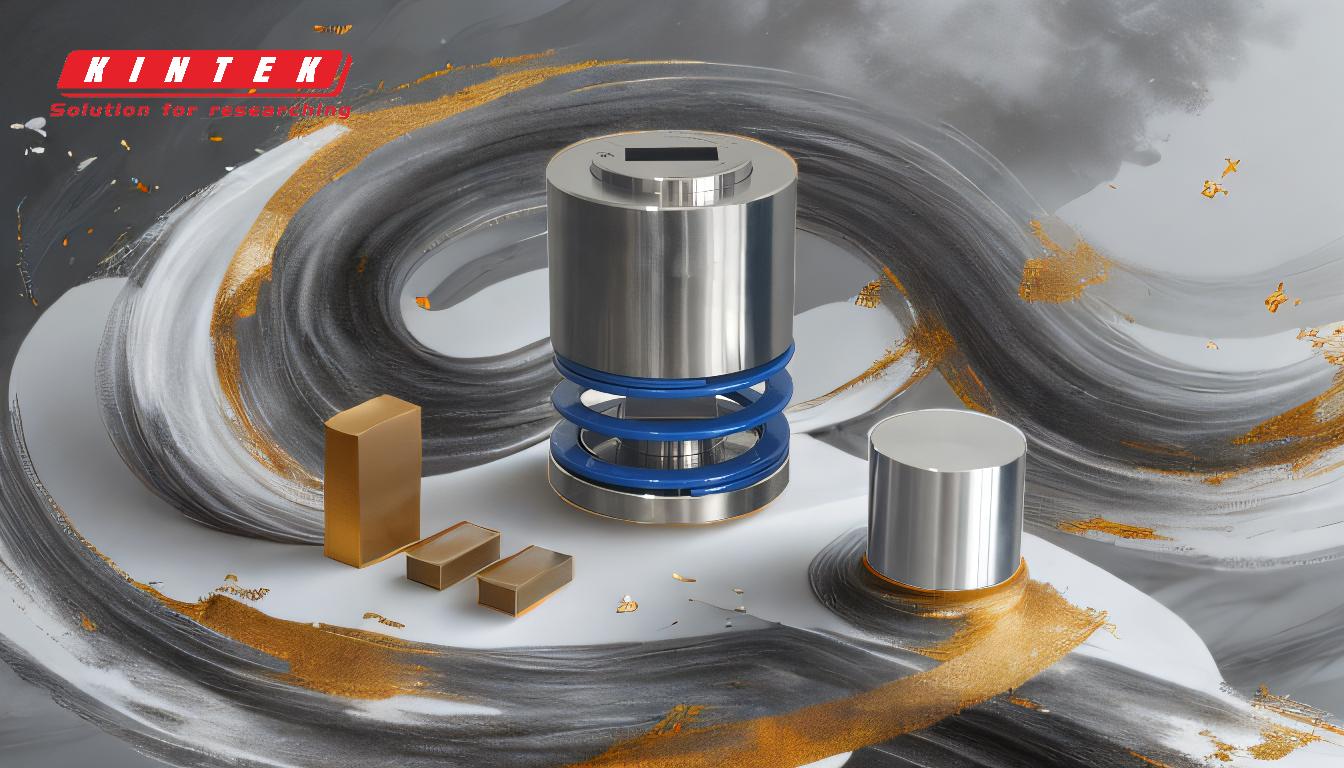
-
Hot Extrusion
- Definition: Hot extrusion involves heating the material (typically metals like aluminum, copper, or steel) above its recrystallization temperature before forcing it through a die.
-
Process:
- The material is heated to a high temperature (often between 50% to 75% of its melting point) to reduce its hardness and increase its malleability.
- The softened material is then pushed through a die using a laboratory hydraulic press or mechanical press to achieve the desired shape.
-
Applications:
- Automotive parts (e.g., engine components, frames).
- Aerospace components (e.g., structural elements, turbine parts).
- Large structural components (e.g., beams, rails).
-
Advantages:
- Easier to shape due to reduced material hardness.
- Suitable for producing complex shapes and large cross-sections.
- Lower force required compared to cold extrusion.
-
Limitations:
- Higher energy consumption due to heating.
- Potential for oxidation or scaling on the material surface.
-
Cold Extrusion
- Definition: Cold extrusion is performed at or near room temperature, where the material is forced through a die without significant heating.
-
Process:
- The material is typically pre-treated (e.g., annealed) to improve its ductility.
- High pressure is applied to the material using a laboratory press , forcing it through the die to create the desired shape.
-
Applications:
- Fasteners (e.g., bolts, nuts, screws).
- Automotive components (e.g., gears, shafts).
- Bicycle parts (e.g., cranks, sprockets).
-
Advantages:
- Produces stronger and more durable parts due to work hardening.
- Better surface finish and dimensional accuracy.
- Lower energy consumption compared to hot extrusion.
-
Limitations:
- Higher force required, which may limit the size of the components.
- Limited to materials with sufficient ductility at room temperature.
-
Comparison of Hot and Cold Extrusion
- Temperature: Hot extrusion operates at elevated temperatures, while cold extrusion is performed at or near room temperature.
- Material Properties: Hot extrusion reduces material hardness, making it easier to shape, whereas cold extrusion enhances material strength through work hardening.
- Applications: Hot extrusion is ideal for large, complex components, while cold extrusion is better suited for smaller, precision parts.
- Energy Consumption: Hot extrusion requires significant energy for heating, while cold extrusion is more energy-efficient.
- Surface Finish: Cold extrusion typically provides a better surface finish and tighter tolerances compared to hot extrusion.
-
Choosing Between Hot and Cold Extrusion
- Material Type: Hot extrusion is preferred for materials that are difficult to shape at room temperature, while cold extrusion is suitable for ductile materials like aluminum and steel.
- Component Size: Hot extrusion is better for large components, whereas cold extrusion is ideal for smaller, intricate parts.
- Strength Requirements: Cold extrusion is preferred when higher strength and durability are required due to work hardening.
- Cost Considerations: Cold extrusion may be more cost-effective for high-volume production of small parts, while hot extrusion is more economical for large, complex shapes.
By understanding the differences between hot and cold extrusion, manufacturers can select the appropriate method based on the material, desired properties, and application requirements. Both techniques play a crucial role in modern manufacturing, offering unique advantages for producing a wide range of products.
Summary Table:
Aspect | Hot Extrusion | Cold Extrusion |
---|---|---|
Temperature | Elevated (50%-75% of melting point) | Room temperature or slightly above |
Material Properties | Reduced hardness, easier to shape | Enhanced strength through work hardening |
Applications | Automotive, aerospace, large structural components | Fasteners, precision automotive parts, bicycle components |
Energy Consumption | Higher due to heating | Lower, more energy-efficient |
Surface Finish | Potential oxidation or scaling | Better surface finish and tighter tolerances |
Component Size | Ideal for large, complex shapes | Suitable for smaller, intricate parts |
Strength Requirements | Lower force required | Higher strength and durability due to work hardening |
Cost Considerations | Economical for large, complex shapes | Cost-effective for high-volume production of small parts |
Need help choosing the right extrusion method for your project? Contact our experts today for tailored advice!