Furnaces are essential equipment in various industrial processes, designed to generate and control heat for material processing. Their working principles revolve around the combustion of fuels (gas, oil, biomass, etc.) or the use of electric heating elements to produce heat, which is then transferred to the material being processed. The heat transfer mechanisms include radiation, convection, and conduction, depending on the furnace design and the type of material. Furnaces are engineered for energy efficiency, uniform temperature distribution, and environmental compliance, often incorporating advanced technologies like oscillating combustion and energy-saving materials.
Key Points Explained:
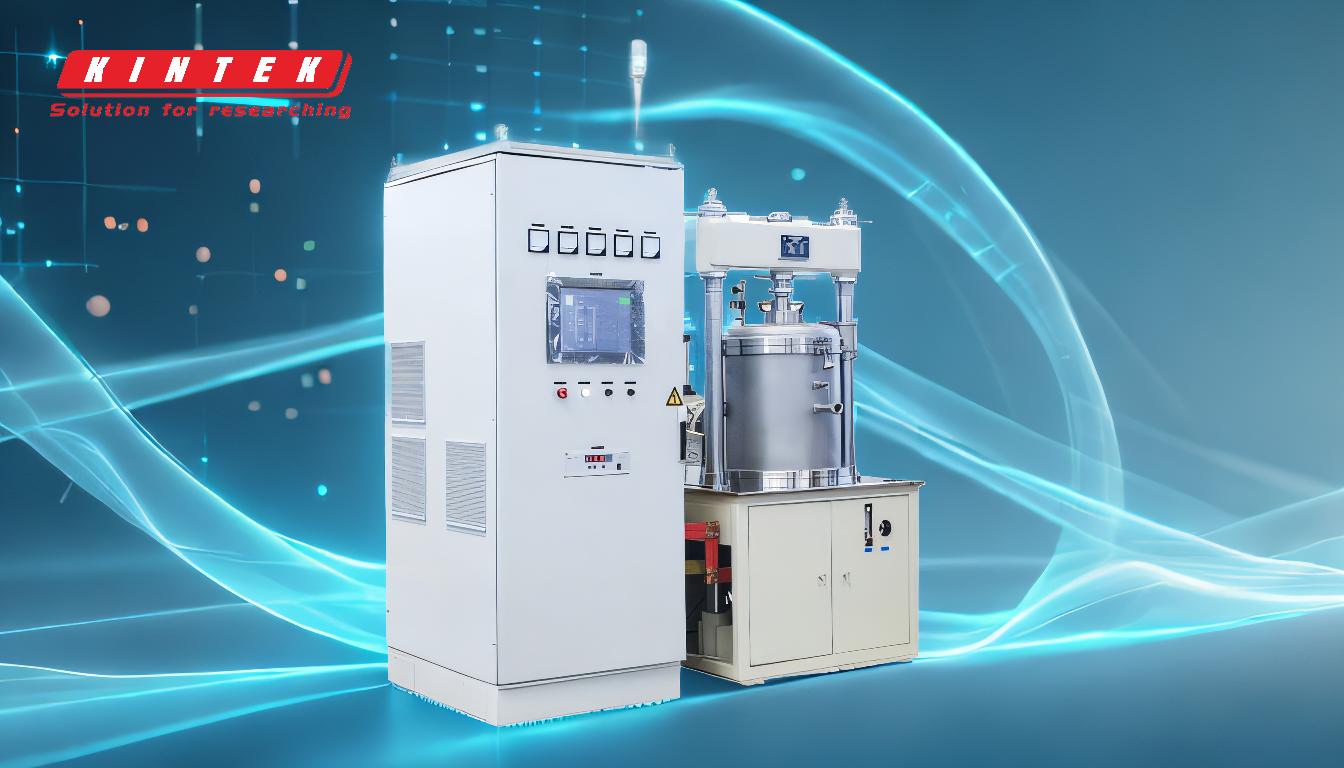
-
Heat Generation:
- Furnaces generate heat primarily through the combustion of fuels such as gas, oil, biomass, or scrap. In gas-powered furnaces, natural gas is burned in an enclosed space to produce heat.
- Alternatively, electric furnaces use high-quality metal and ceramic heating elements that radiate heat within the furnace cavity.
-
Heat Transfer Mechanisms:
- Radiation: Heat is transferred from the combustion gases or heating elements to the material through electromagnetic waves.
- Convection: Hot gases circulate within the furnace, transferring heat to the material by direct contact or through pipes (for fluids).
- Conduction: Solids are heated by direct contact with hot surfaces or gases.
-
Furnace Design Features:
- Rotating Drum: Some furnaces feature a rotating drum with a hydraulic tilting system, ensuring even heating of the material.
- Burner System: Located on a hydraulic opening-closing door, the burner system ensures efficient combustion and heat distribution.
- Heating Zones: Furnaces may have multiple heating zones, each with independent temperature control for better uniformity.
-
Energy Efficiency:
- Furnaces use energy-saving materials like ceramic fiber in a double-layer structure to reduce external temperatures and improve internal temperature uniformity.
- Lightweight construction and fast temperature rise capabilities contribute to energy savings of over 50%.
-
Environmental Considerations:
- Advanced technologies like oscillating combustion (OCT) are used to reduce nitrous oxide (NOx) emissions, making furnaces more environmentally friendly.
- Furnaces can operate in various atmospheres, including air, oxidized gas, inert gas, reducing gas, salt bath, or vacuum, depending on the process requirements.
-
Applications and Material Processing:
- Furnaces are used to heat solids directly or fluids indirectly (via pipes) for processes like melting, annealing, or heat treatment.
- The choice of furnace type and design depends on the material being processed and the desired outcome.
By understanding these principles, equipment and consumable purchasers can make informed decisions about the type of furnace best suited for their specific industrial needs.
Summary Table:
Aspect | Details |
---|---|
Heat Generation | Combustion of fuels (gas, oil, biomass) or electric heating elements. |
Heat Transfer | Radiation, convection, and conduction for effective material heating. |
Design Features | Rotating drum, burner system, multiple heating zones for uniform heating. |
Energy Efficiency | Ceramic fiber insulation, lightweight construction, and fast temperature rise. |
Environmental Impact | Oscillating combustion (OCT) reduces NOx emissions. |
Applications | Melting, annealing, heat treatment for solids and fluids. |
Ready to optimize your industrial processes with the right furnace? Contact our experts today for tailored solutions!