Ceramics that are commonly sintered include alumina, aluminum nitride, zirconia, silicon nitride, boron nitride, and silicon carbide. Sintering is a process that involves high temperatures and sometimes additional forces like pressure or electrical currents to reduce material porosity and consolidate the powdery structure. This process is essential for creating durable ceramic objects and is applied in various industries, including pottery and advanced technical ceramics. Different types of ceramics require specific sintering techniques, ranging from simple kilns for porcelain to precisely controlled high-temperature environments for advanced non-oxide ceramics.
Key Points Explained:
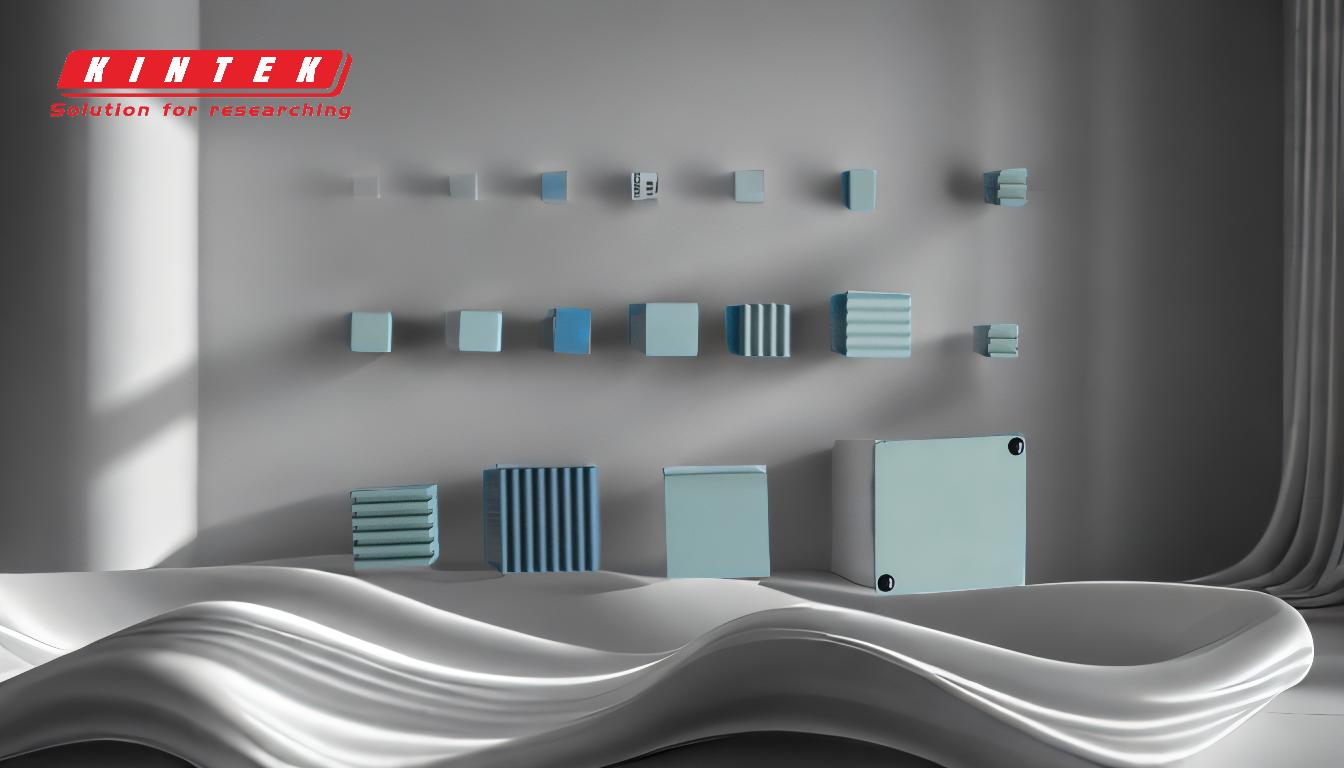
-
Commonly Sintered Ceramics:
- Alumina (Aluminum Oxide): Widely used due to its high strength and thermal stability. It is sintered to produce components for electronics, cutting tools, and biomedical implants.
- Aluminum Nitride: Known for its excellent thermal conductivity and electrical insulation, it is sintered for use in electronic substrates and heat sinks.
- Zirconia (Zirconium Oxide): Valued for its toughness and resistance to wear, it is sintered for applications in dental ceramics, cutting tools, and thermal barrier coatings.
- Silicon Nitride: Offers high strength and thermal shock resistance, making it ideal for use in bearings, engine components, and cutting tools.
- Boron Nitride: Used for its lubricating properties and thermal stability, it is sintered for applications in high-temperature environments and electrical insulators.
- Silicon Carbide: Known for its hardness and thermal conductivity, it is sintered for use in abrasives, refractory materials, and semiconductor devices.
-
Sintering Process:
- High Temperatures: Sintering typically involves heating ceramic powders to temperatures below their melting points, causing the particles to bond and densify.
- Additional Forces: Pressure or electrical currents may be applied to enhance the sintering process, reducing porosity and improving material properties.
- Shrinkage and Consolidation: As the glass phases flow, the material shrinks, and the powdery structure consolidates, resulting in a dense and strong ceramic object.
-
Applications of Sintered Ceramics:
- Pottery: Traditional ceramics like porcelain are sintered in kilns to create durable and aesthetically pleasing objects.
- Advanced Technical Ceramics: Non-oxide ceramics require precisely controlled sintering environments, often involving protective atmospheres to prevent oxidation and ensure material stability.
- Industrial Components: Sintered ceramics are used in various industries for components that require high strength, thermal stability, and wear resistance.
-
Specific Sintering Techniques:
- Simple Kiln Sintering: Suitable for traditional ceramics like porcelain, where cost-effectiveness and simplicity are prioritized.
- High-Temperature Sintering: Essential for advanced ceramics, requiring precise temperature control and sometimes protective atmospheres to achieve the desired material properties.
By understanding the types of ceramics that are sintered and the specific techniques involved, purchasers can make informed decisions about the materials and processes that best meet their needs. This knowledge is crucial for selecting the right ceramics for various applications, ensuring optimal performance and durability.
Summary Table:
Ceramic | Key Properties | Applications |
---|---|---|
Alumina (Al₂O₃) | High strength, thermal stability | Electronics, cutting tools, biomedical implants |
Aluminum Nitride (AlN) | Thermal conductivity, electrical insulation | Electronic substrates, heat sinks |
Zirconia (ZrO₂) | Toughness, wear resistance | Dental ceramics, cutting tools, thermal barrier coatings |
Silicon Nitride (Si₃N₄) | High strength, thermal shock resistance | Bearings, engine components, cutting tools |
Boron Nitride (BN) | Lubrication, thermal stability | High-temperature environments, electrical insulators |
Silicon Carbide (SiC) | Hardness, thermal conductivity | Abrasives, refractory materials, semiconductor devices |
Need help selecting the right sintered ceramics for your application? Contact our experts today for personalized advice!