The size of a heating element is determined by a combination of factors, including the required operating temperature, power load, furnace atmosphere, material properties, and application-specific requirements. Heating elements must be designed to handle the maximum temperature and power demands of the system while ensuring uniform heat distribution and longevity. The choice of material, such as ferrochromium-aluminum or silicon carbide, depends on the temperature range and environmental conditions, such as the presence of reactive gases. Additionally, the size must account for the need to maintain temperature uniformity and efficiency in the hot zone. Below, the key factors influencing the size of a heating element are explained in detail.
Key Points Explained:
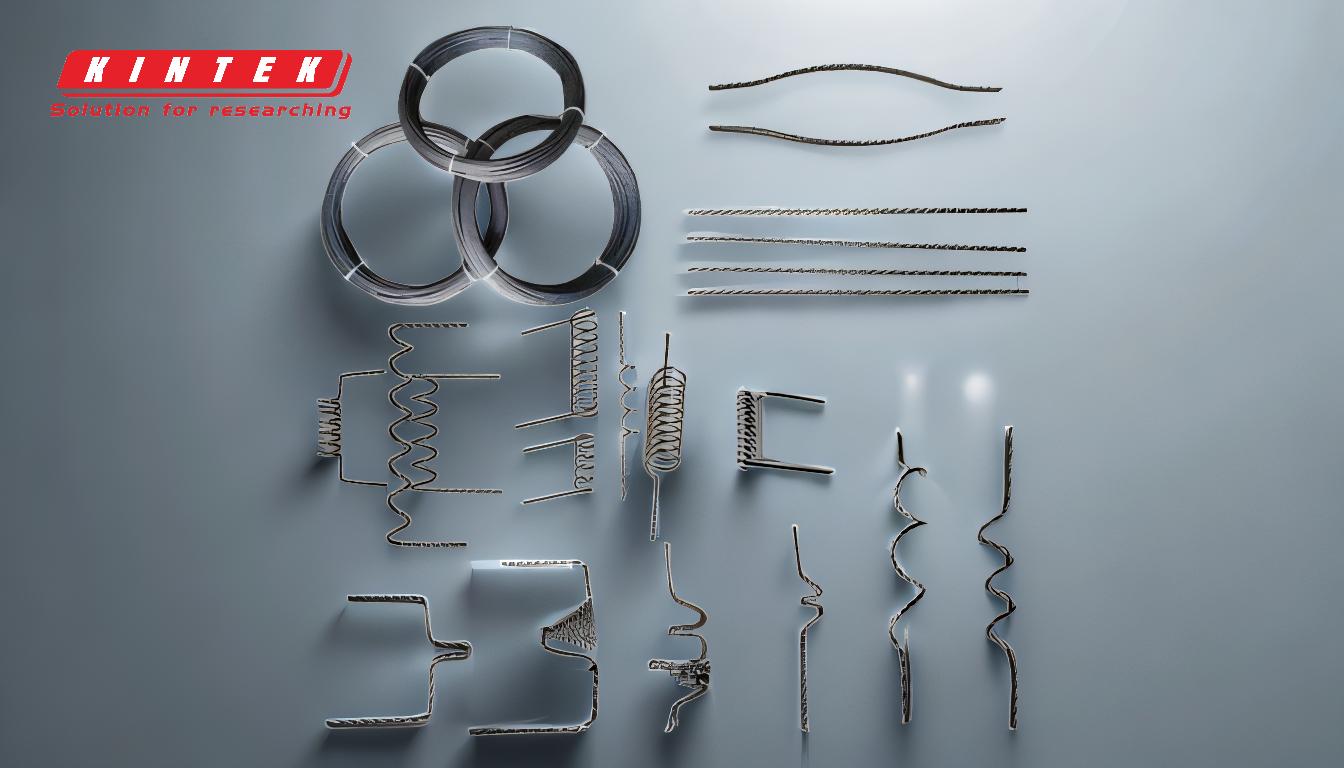
-
Operating Temperature Requirements
- The maximum operating temperature of the heating element is a critical factor in determining its size and material.
- For example, ferrochromium-aluminum wire furnaces are suitable for temperatures up to 1200°C, while silicon carbide bars can handle temperatures up to 1400°C.
- Higher temperatures may require larger or more robust elements to ensure durability and performance.
-
Power Load and Heat Output
- The power load (measured in watts) required to achieve the desired temperature directly influences the size of the heating element.
- Larger workloads or higher heat output requirements may necessitate larger or more numerous heating elements to ensure efficient and uniform heating.
-
Furnace Atmosphere and Environmental Conditions
- The type of furnace atmosphere (e.g., endo gas, low-pressure carburizing, or oxygen-rich environments) affects the choice of heating element material and size.
- Reactive atmospheres may require protective coatings or specific materials to prevent degradation, which can influence the element's size and design.
-
Material Properties and Suitability
- The material of the heating element must be chosen based on its thermal conductivity, resistance to oxidation, and ability to maintain structural integrity at high temperatures.
- For example, materials like silicon carbide are preferred for high-temperature applications due to their stability, while ferrochromium-aluminum is cost-effective for lower-temperature ranges.
-
Temperature Uniformity and Heat Distribution
- The size and arrangement of heating elements must ensure uniform heat distribution across the workload.
- Larger or more complex heating zones may require multiple elements or specific geometries to achieve tight temperature uniformity.
-
Life Expectancy and Durability
- The expected lifespan of the heating element influences its size and material selection.
- Elements designed for long-term use may be larger or made from more durable materials to withstand thermal cycling and environmental stresses.
-
Cost and Efficiency Considerations
- The cost of materials and energy efficiency are practical factors that influence the size and design of heating elements.
- Larger elements may provide better performance but could increase costs, so a balance must be struck between efficiency and affordability.
-
Application-Specific Requirements
- The specific application (e.g., heat treatment, industrial furnaces, or laboratory equipment) dictates the size and type of heating element.
- For instance, industrial furnaces may require larger elements with higher power ratings, while laboratory equipment may prioritize precision and compactness.
In summary, the size of a heating element is determined by a combination of technical requirements (temperature, power load, and material properties) and practical considerations (cost, efficiency, and application-specific needs). By carefully evaluating these factors, the optimal size and design of the heating element can be selected to ensure reliable and efficient performance.
Summary Table:
Factor | Description |
---|---|
Operating Temperature | Determines material and size; higher temps require robust elements. |
Power Load | Influences size based on heat output and workload requirements. |
Furnace Atmosphere | Affects material choice and size due to reactive or protective conditions. |
Material Properties | Thermal conductivity and durability guide material and size selection. |
Temperature Uniformity | Ensures even heat distribution; larger zones may need multiple elements. |
Life Expectancy | Long-term use requires durable materials and appropriate sizing. |
Cost and Efficiency | Balances performance with affordability and energy efficiency. |
Application-Specific Needs | Dictates size and type based on industrial or laboratory requirements. |
Need help selecting the right heating element for your application? Contact our experts today for personalized guidance!