Vulcanizing a tire is a critical process that repairs damage such as cracks or punctures while enhancing the tire's durability and performance. By applying heat and pressure, vulcanization creates a strong bond between the tire and a rubber vulcanizer , ensuring a long-lasting repair. Additionally, vulcanization transforms rubber into a more durable, water-resistant, and insulating material through crosslinking, making it suitable for various industrial applications. This process not only repairs tires but also improves their overall strength and resistance to wear, ensuring safer and more reliable performance.
Key Points Explained:
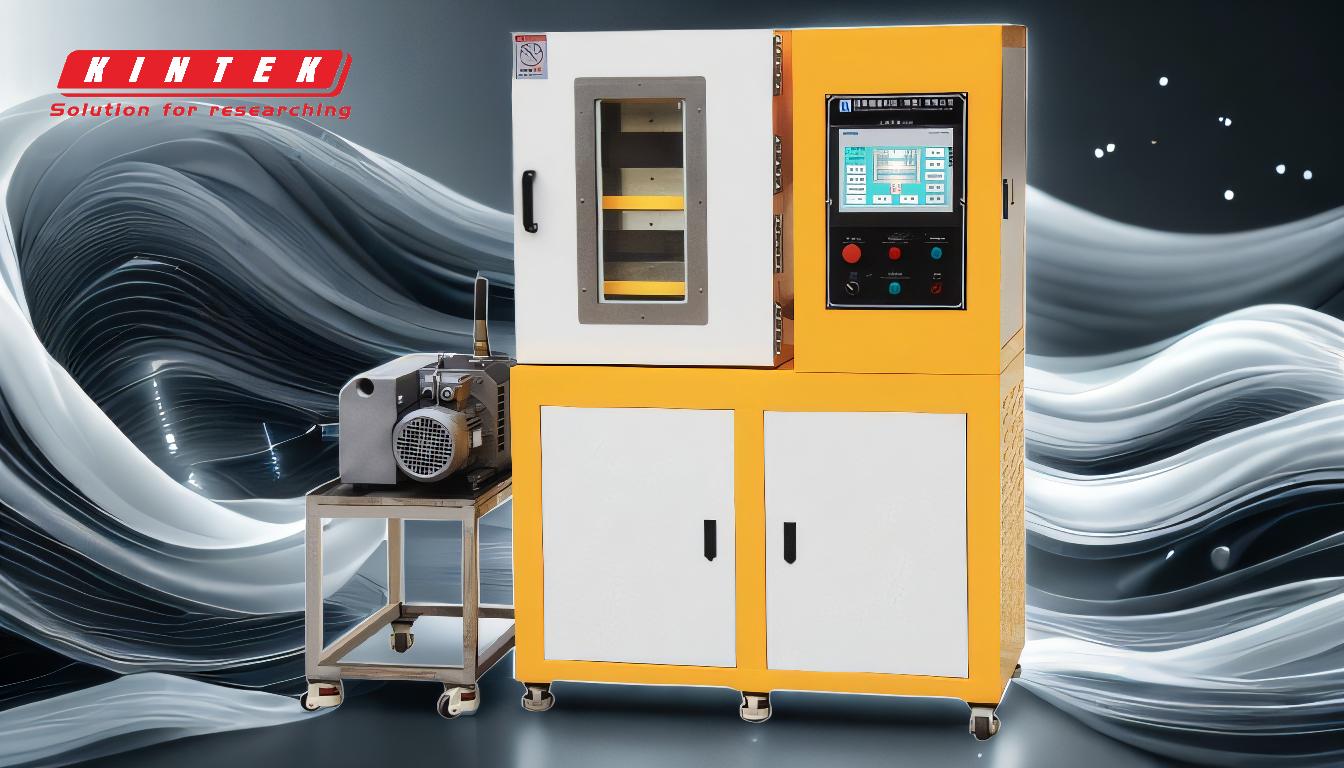
-
What is Tire Vulcanization?
- Tire vulcanization is a repair process that addresses damage like cracks, punctures, or tears in a tire. It involves applying a rubber patch to the damaged area and then using heat and pressure to bond the patch to the tire.
- This process ensures a strong, durable repair that restores the tire's integrity and extends its lifespan.
-
How Vulcanization Works
- Vulcanization involves crosslinking rubber molecules through the application of heat and pressure. This chemical process transforms the rubber, making it stronger, more elastic, and resistant to wear and tear.
- For tire repairs, the heat and pressure activate the bonding agents in the rubber patch, creating a seamless connection with the tire's surface.
-
Benefits of Vulcanizing a Tire
- Durability: Vulcanization strengthens the rubber, making the repaired area as robust as the original tire material.
- Water Resistance: The process makes the rubber resistant to moisture, preventing further damage from water infiltration.
- Insulation: Vulcanized rubber provides better insulation, which is particularly important for tires exposed to extreme temperatures.
- Cost-Effectiveness: Repairing a tire through vulcanization is often more economical than replacing it, especially for high-quality or specialty tires.
-
Applications Beyond Tire Repair
- Vulcanization is not limited to tires; it is widely used in industries such as automotive, aerospace, energy, and medicine. The process enhances rubber's properties, making it suitable for seals, gaskets, hoses, and other critical components.
- In these industries, vulcanized rubber is valued for its durability, resistance to environmental factors, and ability to maintain shape under stress.
-
Importance in Tire Maintenance
- Vulcanization plays a vital role in tire maintenance by ensuring that repairs are long-lasting and reliable. This is especially important for heavy-duty vehicles, where tire failure can have severe consequences.
- Properly vulcanized repairs help maintain tire performance, including traction, load-bearing capacity, and fuel efficiency.
-
Process Details
- The vulcanization process typically involves cleaning the damaged area, applying a rubber patch or compound, and then using specialized equipment like a heated hydraulic press to apply heat and pressure.
- The temperature and duration of the process are carefully controlled to ensure optimal bonding and material transformation.
By understanding the vulcanization process, tire owners and industry professionals can make informed decisions about tire repair and maintenance, ensuring safety, performance, and cost savings.
Summary Table:
Key Aspect | Details |
---|---|
Process | Applies heat and pressure to bond rubber patches to damaged tires. |
Benefits | Enhances durability, water resistance, insulation, and cost-effectiveness. |
Applications | Used in automotive, aerospace, energy, and medical industries. |
Importance in Tires | Ensures long-lasting repairs, maintains traction, and improves fuel efficiency. |
Process Steps | Clean, apply patch, and use specialized equipment for heat and pressure. |
Discover how vulcanization can extend your tire's lifespan— contact our experts today for professional advice!