Tempering is a heat treatment process applied to materials, particularly steel, to improve their mechanical properties. By heating the material to specific temperatures and then cooling it, tempering reduces brittleness while enhancing toughness and ductility. The process transforms the hardened martensite structure into softer and more durable forms like troostite or sorbite, depending on the temperature range. These changes result in a balance between strength, hardness, and flexibility, making the material more suitable for practical applications.
Key Points Explained:
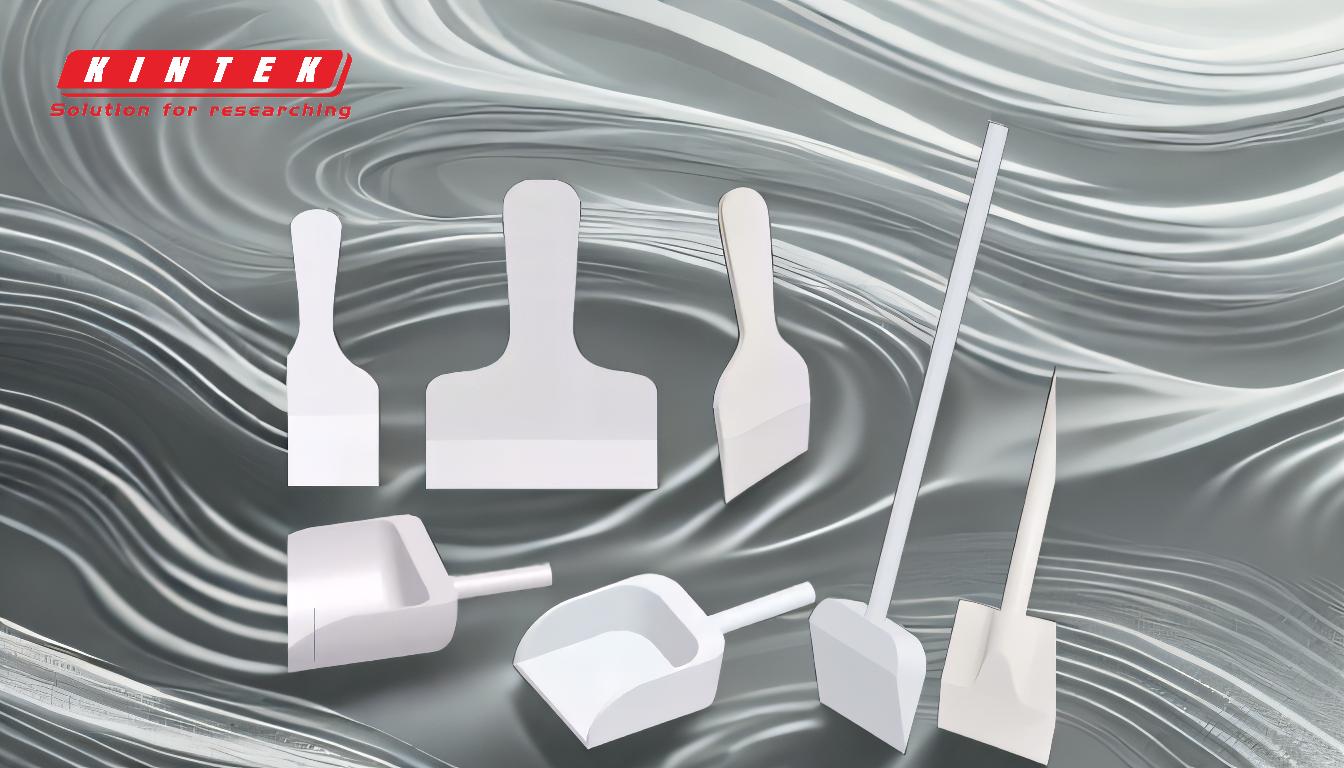
-
Purpose of Tempering:
- Tempering is primarily used to reduce the brittleness of materials, especially steel, after hardening.
- It improves toughness and ductility, making the material less prone to cracking or breaking under stress.
- The process balances hardness with flexibility, ensuring the material can withstand real-world applications.
-
Temperature Ranges and Their Effects:
-
300 to 750°F (149 to 399°C):
- At this range, the hardened martensite structure transforms into troostite.
- Troostite is softer than martensite but significantly tougher, providing a good balance between strength and ductility.
-
750 to 1290°F (399 to 699°C):
- In this higher temperature range, the structure changes into sorbite.
- Sorbite is less strong than troostite but offers greater ductility, making the material more flexible and less brittle.
-
300 to 750°F (149 to 399°C):
-
Microstructural Changes:
- Tempering causes the decomposition of martensite, a hard and brittle structure formed during rapid cooling (quenching).
- The formation of troostite and sorbite involves the precipitation of fine carbides within the ferrite matrix, which softens the material while improving its toughness.
-
Mechanical Property Improvements:
- Reduced Brittleness: Tempering alleviates internal stresses caused by quenching, reducing the risk of cracking.
- Increased Toughness: The material becomes more resistant to impact and shock loading.
- Enhanced Ductility: The material gains the ability to deform plastically without fracturing, making it more workable.
-
Applications of Tempered Materials:
- Tempering is widely used in industries requiring durable and reliable materials, such as automotive, construction, and tool manufacturing.
- Examples include tempered steel springs, gears, and cutting tools, which benefit from the improved balance of hardness and toughness.
-
Trade-offs in Tempering:
- While tempering improves toughness and ductility, it typically reduces hardness and strength compared to the as-quenched state.
- The exact properties depend on the tempering temperature and duration, requiring careful control to achieve the desired material characteristics.
By understanding these key points, a purchaser of equipment or consumables can make informed decisions about the suitability of tempered materials for specific applications, ensuring optimal performance and longevity.
Summary Table:
Aspect | Details |
---|---|
Purpose | Reduces brittleness, improves toughness, and balances hardness with flexibility. |
Temperature Ranges | 300-750°F: Forms troostite (tougher). 750-1290°F: Forms sorbite (more ductile). |
Microstructural Changes | Decomposes martensite into troostite or sorbite, improving toughness. |
Mechanical Improvements | Reduced brittleness, increased toughness, and enhanced ductility. |
Applications | Automotive, construction, tool manufacturing (springs, gears, cutting tools). |
Trade-offs | Reduces hardness and strength while improving flexibility and durability. |
Learn how tempering can optimize your materials for real-world applications—contact our experts today!