Calcination is a thermal treatment process used to induce thermal decomposition, phase transition, or removal of volatile fractions at high temperatures. The furnaces used for calcination are specifically designed to handle high temperatures and provide uniform heating, which is critical for achieving the desired chemical or physical changes. Based on the references provided, the most common furnaces used for calcination include muffle furnaces, reverberatory furnaces, shaft furnaces, and kilns. These furnaces are chosen based on the material being processed, the scale of operation (laboratory or industrial), and the specific temperature requirements. Below is a detailed explanation of the key points related to calcination furnaces.
Key Points Explained:
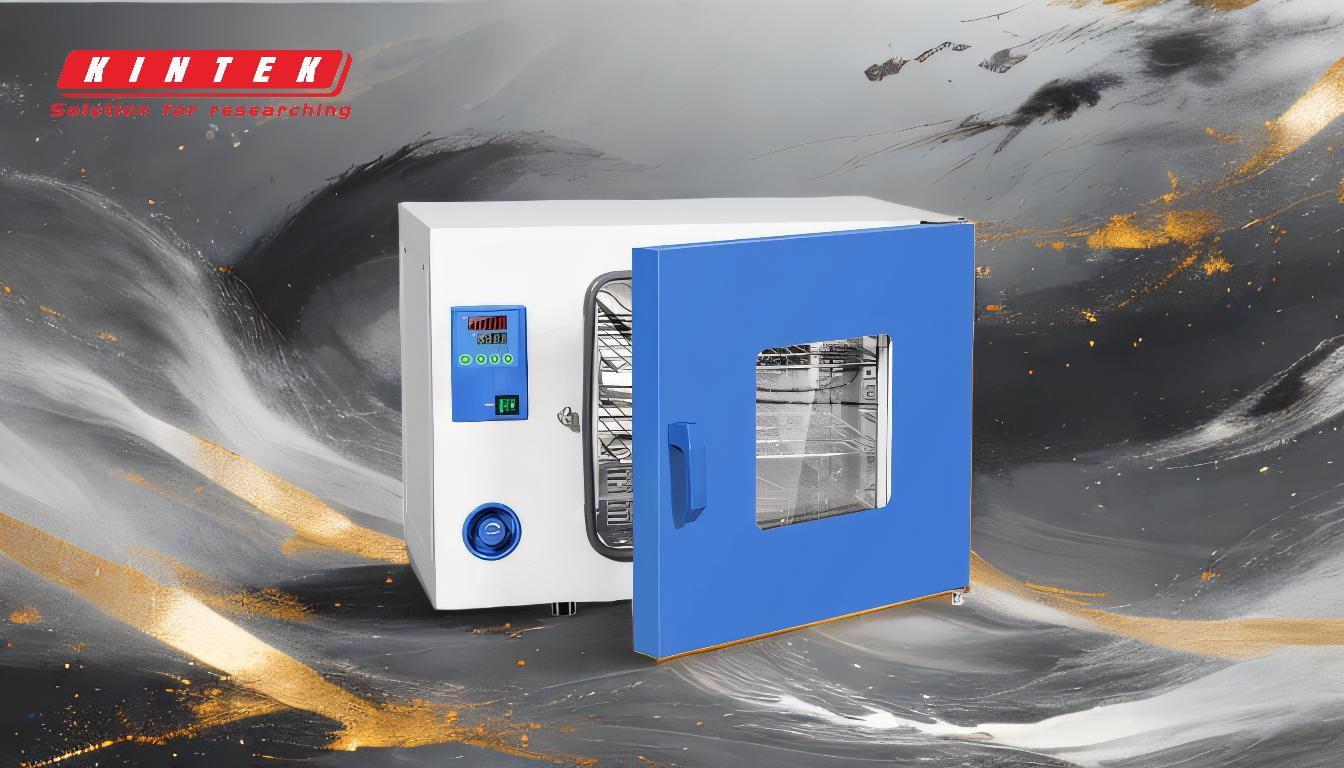
-
Types of Furnaces Used for Calcination:
- Muffle Furnaces: These are widely used in both laboratory and industrial settings. They feature a chamber surrounded by heating elements, ensuring uniform temperature distribution. Muffle furnaces are ideal for calcination because they prevent contamination of the material being processed by isolating it from combustion gases.
- Reverberatory Furnaces: These furnaces are designed for large-scale industrial applications. They use a flame to heat the material indirectly, with the heat reflecting off the furnace walls. This design is suitable for calcining materials like ores and minerals.
- Shaft Furnaces: Commonly used for continuous calcination processes, shaft furnaces are vertical structures where materials move downward while being heated. They are efficient for processing large quantities of materials, such as limestone or cement clinker.
- Kilns: Kilns are versatile and can be used for calcination in industries like ceramics and cement production. They operate at high temperatures and can be designed as rotary or stationary units, depending on the application.
-
Key Features of Calcination Furnaces:
- High-Temperature Capability: Calcination typically requires temperatures ranging from 500°C to over 1000°C. Furnaces used for this process must be capable of maintaining these temperatures consistently.
- Uniform Heating: Uniform temperature distribution is critical to ensure complete and consistent calcination. Furnaces like muffle and reverberatory types are designed to achieve this.
- Controlled Atmosphere: Some calcination processes require a specific atmosphere (e.g., inert or oxidizing). Muffle furnaces, for example, can be sealed to control the internal environment.
- Durability and Insulation: Calcination furnaces must withstand prolonged exposure to high temperatures and corrosive materials. High-quality insulation materials, such as ceramic fiber, are often used to improve energy efficiency and durability.
-
Industrial vs. Laboratory Use:
- Industrial Furnaces: Industrial calcination furnaces, such as reverberatory and shaft furnaces, are designed for large-scale production. They are robust, energy-efficient, and capable of handling high throughput.
- Laboratory Furnaces: Muffle furnaces are commonly used in laboratories for small-scale calcination experiments. They offer precise temperature control and are compact, making them suitable for research and development.
-
Applications of Calcination Furnaces:
- Cement Production: Calcination of limestone to produce lime is a key step in cement manufacturing. Shaft kilns and rotary kilns are commonly used for this purpose.
- Metal Processing: Calcination is used to remove impurities from metal ores. Reverberatory furnaces are often employed in this industry.
- Ceramics and Glass: Kilns are used to calcine raw materials like clay and silica, which are essential for ceramics and glass production.
- Chemical Industry: Calcination is used to produce chemicals like alumina and titanium dioxide. Muffle furnaces are often used in laboratory settings to develop and test these processes.
-
Advantages of Different Furnace Types:
- Muffle Furnaces: Ideal for small-scale and contamination-sensitive processes due to their enclosed design.
- Reverberatory Furnaces: Suitable for large-scale operations and materials that require indirect heating.
- Shaft Furnaces: Efficient for continuous processing and high-volume production.
- Kilns: Versatile and adaptable to various materials and industries.
-
Considerations for Selecting a Calcination Furnace:
- Material Properties: The type of material being calcined (e.g., thermal stability, particle size) influences the choice of furnace.
- Temperature Requirements: The furnace must be capable of reaching and maintaining the required calcination temperature.
- Scale of Operation: Industrial-scale processes require robust, high-capacity furnaces, while laboratory-scale processes benefit from precise and compact designs.
- Energy Efficiency: The furnace's design and insulation should minimize energy consumption, especially for large-scale operations.
- Environmental Impact: Electric furnaces are preferred in settings where reducing emissions is a priority.
In summary, the choice of furnace for calcination depends on the specific application, material properties, and operational scale. Muffle, reverberatory, shaft furnaces, and kilns are the most commonly used types, each offering unique advantages for different calcination processes. Understanding the key features and applications of these furnaces is essential for selecting the right equipment for your needs.
Summary Table:
Furnace Type | Key Features | Applications |
---|---|---|
Muffle Furnace | Uniform heating, contamination-free, precise temperature control | Laboratory research, small-scale calcination, chemical processing |
Reverberatory Furnace | Indirect heating, large-scale, robust design | Metal ore processing, industrial calcination |
Shaft Furnace | Continuous processing, high throughput, vertical design | Cement production, limestone calcination |
Kiln | Versatile, high-temperature, rotary or stationary design | Ceramics, glass production, cement manufacturing |
Need help selecting the right calcination furnace for your application? Contact our experts today for personalized advice!