A CVD Tube Furnace, or Chemical Vapor Deposition Tube Furnace, is a specialized heating device designed for high-temperature processes such as chemical vapor deposition (CVD), sintering, and material testing. It features a vertically standing chamber with a fixed well tube reactor, allowing for precise control over temperature and atmosphere. The furnace is equipped with high alumina fiber insulation and powerful heaters to ensure uniform heating. It supports both vacuum and atmospheric conditions, making it versatile for various applications like quenching, annealing, and material synthesis. With microprocessor PID control, fast heating/cooling rates, and options for quartz or alumina tubes, it is widely used in laboratories, universities, and industrial settings for advanced material research and processing.
Key Points Explained:
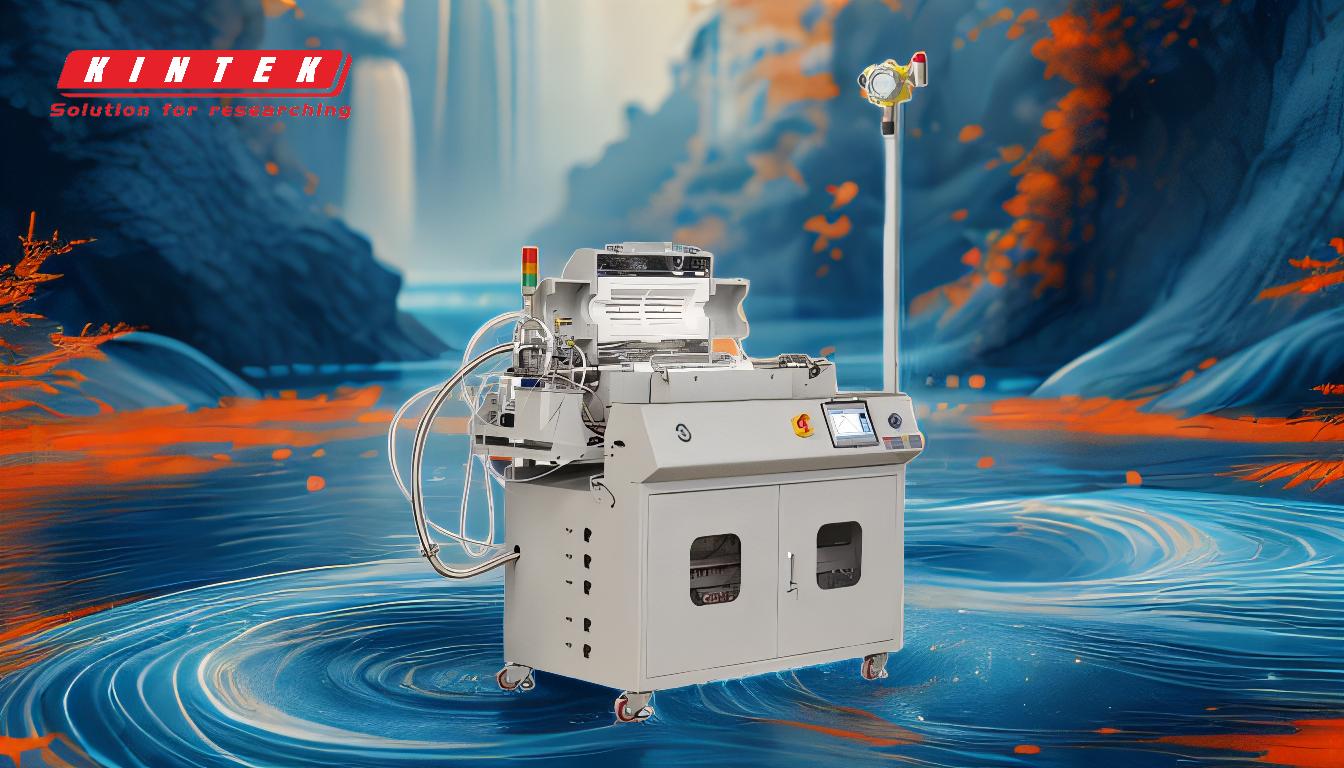
-
Definition and Purpose:
- A CVD Tube Furnace is a type of furnace specifically designed for Chemical Vapor Deposition (CVD) processes, as well as other high-temperature applications like sintering, quenching, and material synthesis.
- It is used in both laboratory and industrial settings for precise temperature control and atmosphere regulation.
-
Design and Structure:
- The furnace features a vertically standing chamber with a fixed well tube reactor, which allows for efficient heating and cooling of materials.
- The chamber is typically cylindrical or semi-cylindrical, lined with high alumina fibers for insulation and equipped with all-round heaters to ensure uniform temperature distribution.
-
Key Components:
- Vacuum Tubes with SS KF Flanges: These enable vacuum pumping and gas purging, allowing the furnace to operate under controlled atmospheres or vacuum conditions.
- Furnace Tubes: Available in quartz (25mm to 300mm diameter, max 1200°C) or alumina (25mm to 100mm diameter, max 1700°C), depending on the required temperature range and material compatibility.
- Microprocessor PID Control: Ensures precise temperature regulation, fast heating/cooling rates, and low energy consumption.
-
Applications:
- Material Processing: Used for quenching, annealing, sintering, and tempering of materials, especially wire-shaped or small steel pieces.
- Chemical and Physical Processes: Suitable for chemical analysis, physical decomposition, purification, sublimation, and degassing.
- Advanced Research: Ideal for vacuum coating, nanofilm preparation, nanowire growth, and battery material drying and sintering.
-
Atmosphere Control:
- The furnace can operate under vacuum or controlled atmospheres (e.g., inert gases), making it suitable for processes requiring precise environmental conditions, such as CVD/CVI experiments or atmosphere reduction.
-
Versatility and Use Cases:
- Widely used in universities, research institutes, and industrial enterprises for high-temperature experiments and material synthesis.
- Common applications include high-temperature atmosphere sintering, nanowire growth, and the preparation of advanced materials like electronic ceramics and nanofilms.
-
Advantages:
- Temperature Uniformity: The powerful all-round heaters and high alumina fiber insulation ensure consistent heating across the chamber.
- Energy Efficiency: Fast heating and cooling rates reduce energy consumption.
- Flexibility: Compatible with a wide range of materials and processes, thanks to the availability of different furnace tube materials and diameters.
-
Industrial and Research Relevance:
- Essential for industries and research units involved in material science, electronics, and nanotechnology.
- Supports periodic operations in laboratories and industrial settings, such as element analysis, material testing, and new material development.
By combining precise temperature control, versatile atmosphere options, and robust design, a CVD Tube Furnace is a critical tool for advanced material research and high-temperature processing in both academic and industrial environments.
Summary Table:
Feature | Description |
---|---|
Purpose | Designed for CVD, sintering, annealing, and material synthesis. |
Design | Vertical chamber with high alumina fiber insulation and all-round heaters. |
Temperature Range | Up to 1700°C (alumina tubes) or 1200°C (quartz tubes). |
Atmosphere Control | Supports vacuum and controlled atmospheres (e.g., inert gases). |
Applications | Quenching, annealing, nanowire growth, nanofilm preparation, and more. |
Advantages | Uniform heating, energy efficiency, and compatibility with diverse materials. |
Ready to elevate your material research? Contact us today to find the perfect CVD Tube Furnace for your needs!