The remelting process is a specialized metallurgical technique used to refine and improve the quality of metals and alloys. It involves melting a pre-existing metal or alloy and then solidifying it under controlled conditions to achieve a more uniform microstructure, reduce impurities, and enhance mechanical properties. This process is commonly used in industries such as aerospace, power generation, and tool manufacturing, where high-performance materials are critical. Remelting techniques include vacuum arc remelting (VAR), electroslag remelting (ESR), and electron beam remelting (EBR), each offering unique advantages depending on the material and application requirements.
Key Points Explained:
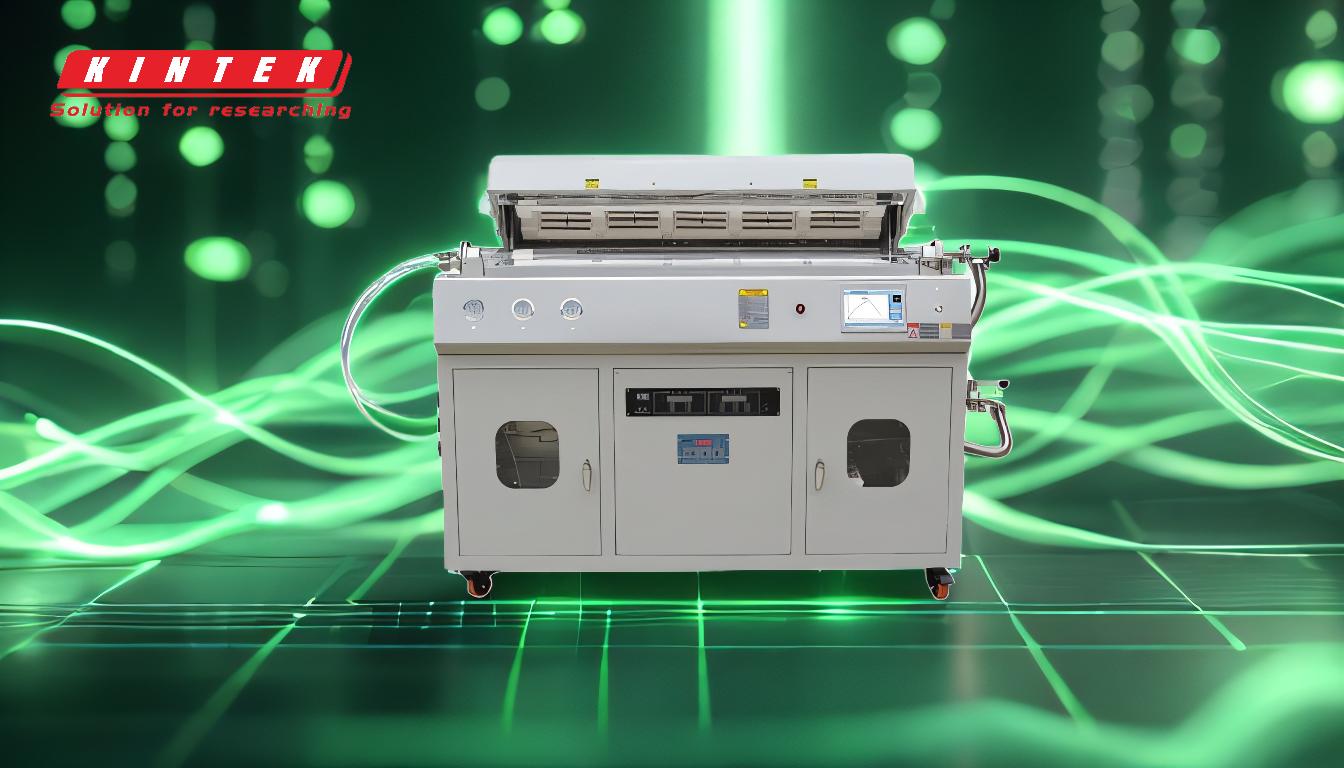
-
Definition and Purpose of Remelting:
- Remelting is a secondary melting process where a previously cast or forged metal is melted again under controlled conditions.
- The primary goal is to refine the material by reducing impurities, eliminating defects, and achieving a more homogeneous microstructure.
- This process is essential for producing high-performance alloys used in demanding applications like aerospace components, turbine blades, and medical implants.
-
Types of Remelting Processes:
-
Vacuum Arc Remelting (VAR):
- VAR is performed in a vacuum to minimize contamination and oxidation.
- An electric arc is used to melt the electrode, and the molten metal solidifies in a water-cooled copper mold.
- This process is ideal for reactive metals like titanium and nickel-based superalloys.
-
Electroslag Remelting (ESR):
- ESR uses a consumable electrode and a molten slag layer to refine the metal.
- The slag acts as a filter, removing impurities and non-metallic inclusions.
- This method is widely used for tool steels and high-alloy steels.
-
Electron Beam Remelting (EBR):
- EBR employs a high-energy electron beam to melt the metal in a vacuum.
- It is suitable for refractory metals like tungsten and molybdenum, which require extremely high melting temperatures.
-
Vacuum Arc Remelting (VAR):
-
Benefits of Remelting:
- Improved Purity: Remelting reduces impurities and non-metallic inclusions, leading to cleaner and more reliable materials.
- Enhanced Microstructure: Controlled solidification results in a finer and more uniform grain structure, improving mechanical properties such as strength and fatigue resistance.
- Reduced Defects: The process minimizes voids, porosity, and segregation, ensuring higher-quality end products.
-
Applications of Remelting:
- Aerospace: Critical components like turbine blades and engine parts require materials with exceptional strength and durability, making remelting essential.
- Power Generation: High-performance alloys used in nuclear reactors and gas turbines benefit from the refined properties achieved through remelting.
- Medical Devices: Implants and surgical tools made from biocompatible metals like titanium rely on remelting for purity and reliability.
-
Challenges and Considerations:
- Cost: Remelting processes are expensive due to the specialized equipment and energy requirements.
- Process Control: Precise control of parameters like temperature, cooling rate, and atmosphere is crucial to achieving the desired material properties.
- Material Limitations: Not all metals and alloys are suitable for remelting, and the choice of process depends on the material's characteristics and intended use.
By understanding the remelting process, manufacturers can produce materials with superior properties, ensuring they meet the stringent demands of modern industries.
Summary Table:
Aspect | Details |
---|---|
Definition | Secondary melting process to refine metals under controlled conditions. |
Purpose | Reduce impurities, eliminate defects, and achieve uniform microstructure. |
Types | - Vacuum Arc Remelting (VAR) |
- Electroslag Remelting (ESR)
- Electron Beam Remelting (EBR) | | Benefits | - Improved purity
- Enhanced microstructure
- Reduced defects | | Applications | Aerospace, power generation, medical devices | | Challenges | High cost, precise process control, material limitations |
Discover how remelting can elevate your material quality—contact our experts today for tailored solutions!