Quenching is a heat treatment process where a material, typically metal, is rapidly cooled to achieve desired mechanical properties such as increased hardness or strength. An example of quenching involves heating a metal to a high temperature and then rapidly cooling it by immersing it in a quenching medium like water, oil, or air. This process alters the microstructure of the metal, enhancing its properties. In the context of advanced manufacturing, quenching can also be applied to materials processed using techniques like cold isostatic pressing machine, which compresses powders into dense, high-performance components. These components may later undergo quenching to further refine their mechanical properties.
Key Points Explained:
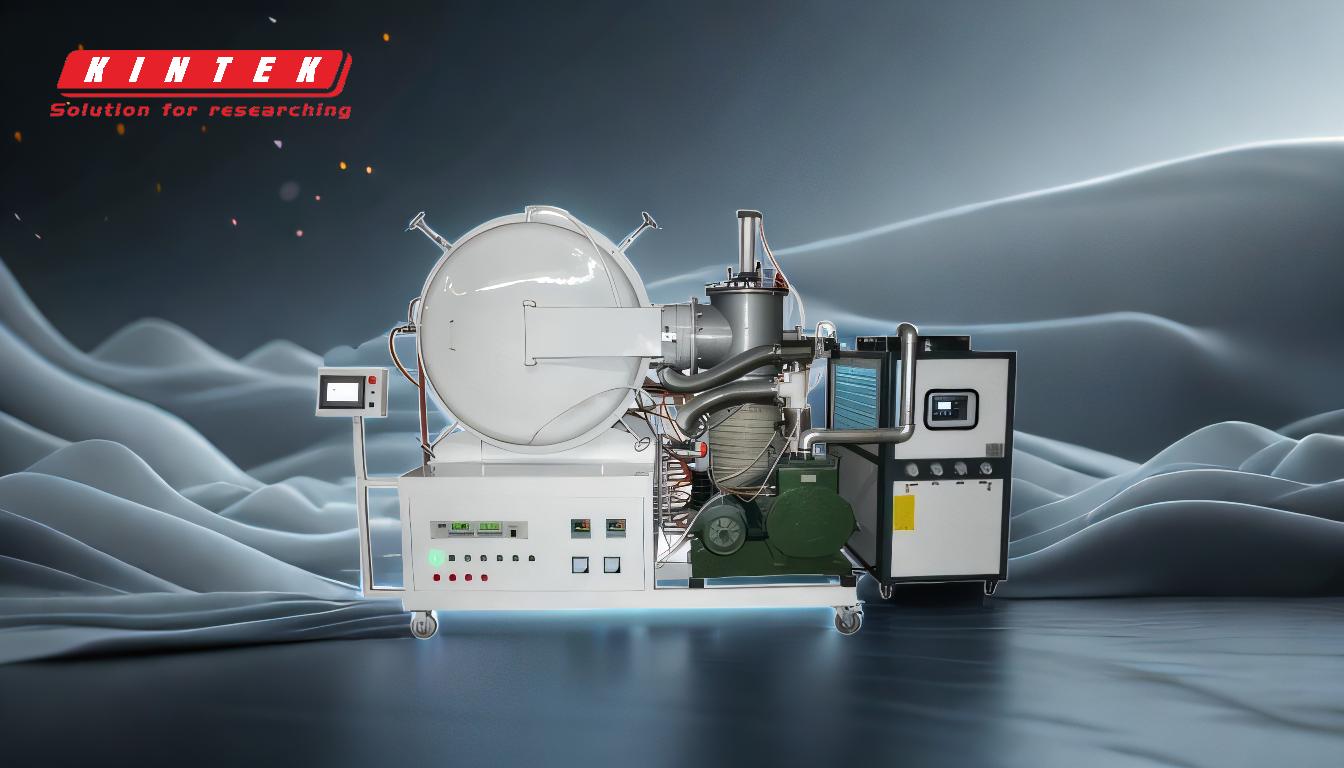
-
Definition and Purpose of Quenching:
- Quenching is a thermal process used to rapidly cool a material, typically metal, to alter its microstructure and improve mechanical properties such as hardness, strength, and wear resistance.
- The process involves heating the material to a specific temperature and then cooling it rapidly using a quenching medium like water, oil, or air.
-
Example of Quenching in Metal Processing:
- A common example of quenching is the heat treatment of steel. The steel is heated to a high temperature (austenitizing temperature) and then rapidly cooled in water or oil. This transforms the microstructure from austenite to martensite, resulting in increased hardness and strength.
- Quenching is widely used in industries such as automotive, aerospace, and tool manufacturing to produce components with enhanced mechanical properties.
-
Connection to Cold Isostatic Pressing (CIP):
- Cold isostatic pressing machine is a manufacturing technique that uses uniform pressure to compress powders into dense, high-performance components. These components often require further heat treatment, such as quenching, to achieve optimal mechanical properties.
- For example, a metal part produced via CIP may undergo quenching to enhance its hardness and wear resistance, making it suitable for critical applications.
-
Advantages of Combining CIP and Quenching:
- CIP produces components with uniform density and complex shapes, which are difficult to achieve with conventional methods. Quenching further refines these components, improving their mechanical properties.
- This combination is particularly useful in industries requiring high-performance materials, such as aerospace, where components must withstand extreme conditions.
-
Applications of Quenching in Advanced Manufacturing:
- Quenching is applied to materials like ceramics, powder metallurgy products, and sputtering targets, which are often processed using CIP. These materials are used in industries such as electronics, energy, and medical devices.
- For instance, a dense ceramic component produced via CIP may undergo quenching to enhance its thermal stability and mechanical strength for use in high-temperature environments.
-
Technical Considerations in Quenching:
- The choice of quenching medium (water, oil, or air) depends on the material and desired properties. Water provides rapid cooling, while oil offers slower cooling to reduce the risk of cracking.
- The quenching process must be carefully controlled to avoid defects such as distortion or cracking, especially in complex shapes produced via CIP.
-
Future Trends in Quenching and CIP:
- Advances in quenching technologies, such as controlled atmosphere quenching and high-pressure gas quenching, are improving the precision and efficiency of the process.
- The integration of CIP with advanced quenching techniques is expanding the application of these methods in emerging fields like solid-state batteries and additive manufacturing.
By understanding the principles of quenching and its application in conjunction with techniques like cold isostatic pressing machine, manufacturers can produce high-performance materials tailored to specific industrial requirements.
Summary Table:
Aspect | Details |
---|---|
Definition | Rapid cooling of materials to alter microstructure and enhance properties. |
Example | Steel heated to high temperature and cooled in water or oil for hardness. |
Connection to CIP | Cold isostatic pressing produces dense components, often followed by quenching. |
Applications | Automotive, aerospace, electronics, and medical devices. |
Quenching Mediums | Water, oil, or air, chosen based on material and desired properties. |
Future Trends | Controlled atmosphere quenching and integration with CIP for advanced uses. |
Discover how quenching can optimize your manufacturing process—contact our experts today!