Annealing in an air atmosphere is a heat treatment process where metal is heated to a specific temperature to alter its microstructure, making it more ductile and less brittle. Unlike annealing in a vacuum or controlled atmosphere (e.g., hydrogen or argon), annealing in air does not prioritize surface finish or prevent oxidation. This method is typically used when surface appearance is not critical, and the focus is on improving the material's mechanical properties. The process involves heating the metal to a temperature where its crystalline structure becomes fluid, holding it at that temperature to allow defects to repair, and then cooling it slowly to achieve a more ductile structure.
Key Points Explained:
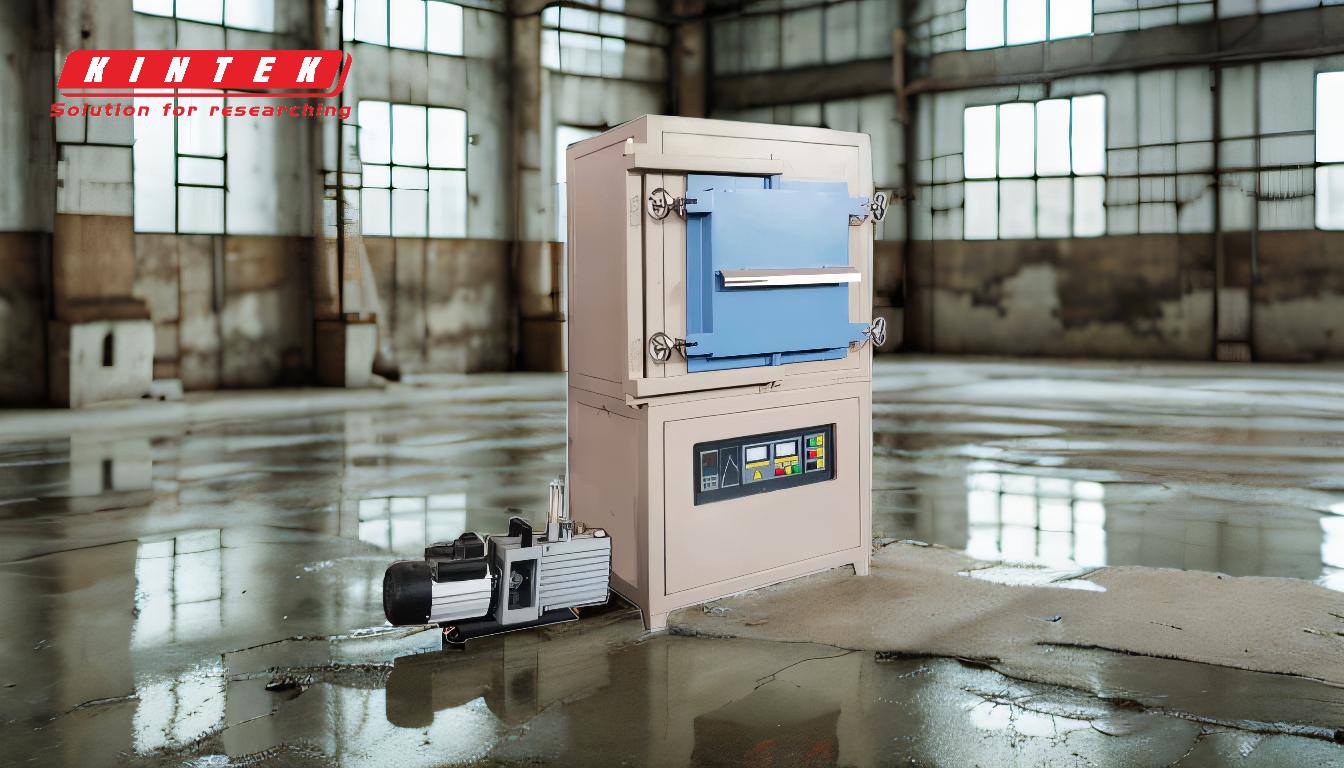
-
Definition of Annealing in Air Atmosphere:
- Annealing in air involves heating metal in an open-air environment to a temperature where its crystalline structure becomes fluid but remains solid.
- This process is distinct from annealing in controlled atmospheres (e.g., vacuum, hydrogen, or argon), which are used to achieve specific surface finishes or prevent oxidation.
-
Purpose of Annealing in Air:
- The primary goal is to improve the metal's mechanical properties, such as ductility and toughness, by reducing internal stresses and refining the grain structure.
- Surface finish is not a priority in this method, making it suitable for applications where appearance is less critical.
-
Process Steps:
- Heating: The metal is heated to a specific temperature, typically below its melting point, where the crystalline structure becomes fluid.
- Holding: The metal is held at this temperature for a set duration to allow defects (e.g., dislocations) to repair themselves.
- Cooling: The metal is cooled slowly to room temperature, which helps achieve a more ductile and less brittle structure.
-
Comparison with Controlled Atmosphere Annealing:
- Surface Finish: Annealing in air often results in oxidation, leading to a less refined surface compared to vacuum or reducing atmosphere annealing.
- Decarburization: In air, decarburization (loss of carbon from the surface) can occur, which may affect the material's properties. Controlled atmospheres (e.g., endothermic or neutral) are used to minimize this effect.
-
Applications:
- Annealing in air is commonly used for materials where surface finish is not critical, such as structural components or parts that will undergo further processing (e.g., machining or coating).
- It is also used when cost-effectiveness is a priority, as air annealing does not require specialized equipment or gases.
-
Advantages and Disadvantages:
-
Advantages:
- Cost-effective due to the lack of need for controlled atmospheres or specialized equipment.
- Effective for improving ductility and reducing brittleness in a wide range of metals.
-
Disadvantages:
- Oxidation and decarburization can occur, affecting surface quality and material properties.
- Not suitable for applications requiring a bright or pristine surface finish.
-
Advantages:
-
Material Considerations:
- The effectiveness of air annealing depends on the type of metal and its intended use. For example, steels, copper, and aluminum alloys are commonly annealed in air.
- Materials prone to severe oxidation or decarburization may require alternative annealing methods.
-
Practical Insights for Purchasers:
- When selecting annealing services or equipment, consider whether surface finish is a critical factor. If not, air annealing may be a cost-effective solution.
- For materials sensitive to oxidation or decarburization, explore options for controlled atmosphere annealing to ensure optimal results.
By understanding these key points, purchasers and engineers can make informed decisions about whether annealing in air is suitable for their specific applications and material requirements.
Summary Table:
Aspect | Details |
---|---|
Definition | Heating metal in open air to alter microstructure, improving ductility. |
Purpose | Improve mechanical properties like ductility and toughness. |
Process Steps | Heating, holding at temperature, slow cooling. |
Surface Finish | Oxidation occurs; less refined compared to controlled atmosphere annealing. |
Applications | Structural components, cost-effective solutions for non-critical finishes. |
Advantages | Cost-effective, improves ductility in various metals. |
Disadvantages | Oxidation and decarburization may occur. |
Material Considerations | Suitable for steels, copper, and aluminum alloys. |
Ready to optimize your metal properties with air annealing? Contact us today for expert advice and solutions!