Cold isostatic pressing (CIP) is a versatile manufacturing process used to compact and shape materials at ambient temperatures. It is widely employed across industries such as aerospace, automotive, energy, medical, and electronics due to its ability to produce uniform and high-density parts. CIP is particularly valuable for powder forming, enabling the creation of complex shapes with consistent material properties. It is also used as a post-processing technique in additive manufacturing to enhance dimensional accuracy and reduce residual stresses. The process involves applying uniform pressure using a liquid medium, making it suitable for a wide range of materials, including refractory metals, ceramics, and composites. CIP is divided into wet bag and dry bag methods, each tailored to specific part sizes and complexities.
Key Points Explained:
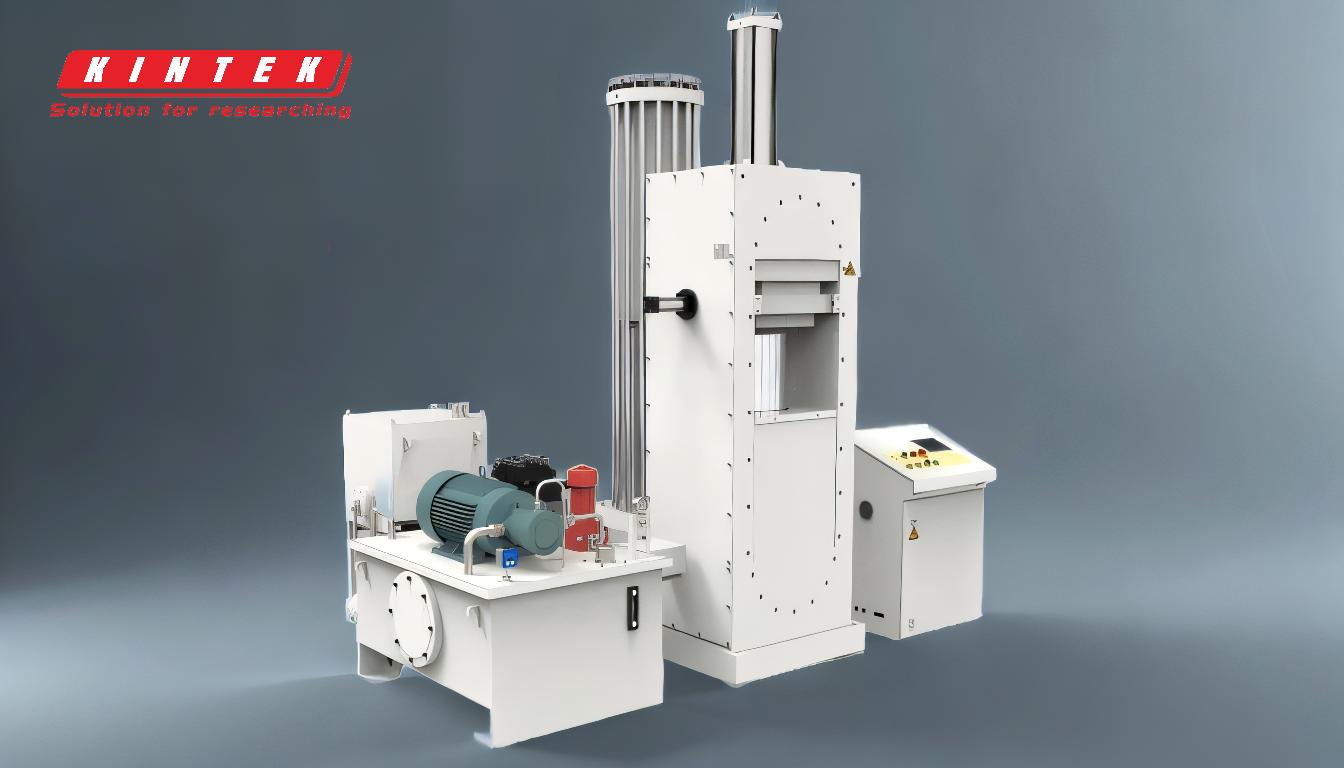
-
Applications of Cold Isostatic Pressing (CIP):
- CIP is used in industries such as aerospace, automotive, energy, medical, and electronics for producing high-quality components.
- It is particularly effective for powder forming of materials like refractory metals, insulators, cemented carbides, and tool steel.
- CIP is also utilized in the production of artificial bones, resin powders, and even food processing applications.
-
Role in Additive Manufacturing:
- CIP serves as a post-processing technique for additive manufacturing, ensuring dimensional accuracy and stability.
- By applying uniform pressure, CIP reduces or eliminates residual stresses and distortions in 3D-printed parts, ensuring they meet required specifications.
-
Types of CIP Methods:
- Wet Bag Method: Suitable for large and complex parts, the mold is removed and refilled after each pressure cycle.
- Dry Bag Method: Ideal for simpler and smaller parts, the mold is an integral part of the vessel, allowing for faster processing.
-
Process Mechanics:
- In CIP, powder material is placed in a mold and subjected to uniform pressure from all sides using a liquid medium, often an oil-water mixture.
- Pressures in a CIP chamber can reach up to 100,000 psi, ensuring high-density and uniform compaction.
-
Material Versatility:
- CIP is compatible with a wide range of materials, including high-melting-point metals, ceramics, and composites.
- This versatility makes it a preferred method for industries requiring precise and high-performance components.
-
Comparison with Hot Isostatic Pressing (HIP):
- Unlike CIP, which operates at ambient temperatures, HIP involves elevated temperatures and solid-state diffusion to fully consolidate parts.
- CIP is primarily used for compaction, while HIP is used for densification and improving material properties.
-
Industry-Specific Benefits:
- In the pharmaceutical and medical industries, CIP is used to produce components with high precision and biocompatibility.
- For the energy sector, CIP helps create durable and efficient components for turbines and other high-stress applications.
By leveraging the unique advantages of CIP, manufacturers can achieve superior material properties, complex geometries, and consistent quality across a wide range of applications.
Summary Table:
Aspect | Details |
---|---|
Key Applications | Aerospace, automotive, energy, medical, electronics, and food processing. |
Material Compatibility | Refractory metals, ceramics, composites, insulators, and tool steel. |
Process Mechanics | Uniform pressure up to 100,000 psi using a liquid medium (oil-water mix). |
CIP Methods | Wet Bag (large/complex parts) and Dry Bag (smaller/simpler parts). |
Role in Additive Manufacturing | Post-processing to reduce residual stresses and improve dimensional accuracy. |
Industry Benefits | High precision, biocompatibility, and durability for critical components. |
Interested in leveraging cold isostatic pressing for your manufacturing needs? Contact us today to learn more!