Sintering is a critical manufacturing process that compacts and fuses solid materials, such as powders, into a dense and cohesive mass by applying heat and pressure below the material's melting point. This process reduces porosity, enhances strength, and improves material properties, making it essential in industries like powder metallurgy, ceramics, and steel production. Direct current sintering, a specialized form of sintering, uses electrical current to generate heat internally within the material, enabling precise control over the sintering process and resulting in high-quality, uniform products.
Key Points Explained:
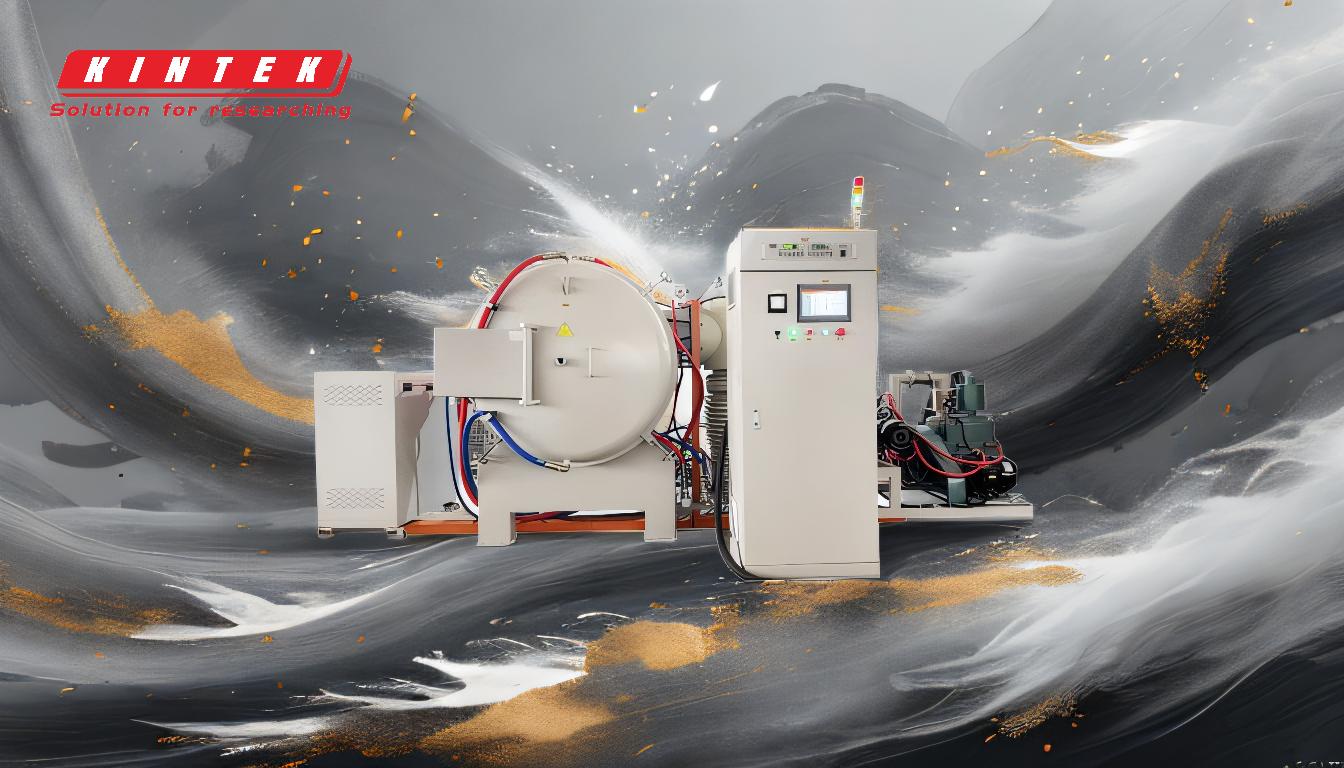
-
Definition of Sintering:
- Sintering is a process that compacts loose or powdered materials into a solid mass by applying heat and pressure below the material's melting point. This reduces porosity and strengthens the material by fusing particles together.
- It is widely used in industries such as powder metallurgy, ceramics, and steel production to create durable and complex components.
-
Stages of Sintering:
- Compaction: The first stage involves compressing the powder into a desired shape, forming a weak and oversized component.
- Thermal Fusion: The second stage involves heating the compacted shape to a temperature below the melting point of the primary material, allowing particles to bond and any binders to burn away, resulting in a strong, integrated part.
-
Applications of Sintering:
- Steel Production: Sintering is used to produce sintered ore from iron ore powder, coal, and lime. This sintered ore improves blast furnace efficiency by enhancing permeability and reducing the coking ratio.
- Powder Metallurgy: Sintering is essential for creating metal parts with high strength and durability, often used in automotive and aerospace industries.
- Ceramics: The process is used to produce ceramic components with precise shapes and high thermal resistance.
-
Liquid-Phase Sintering:
- In this variant, small amounts of additives form a liquid at the sintering temperature. This liquid facilitates particle rearrangement, dissolution, and re-precipitation, leading to denser and pore-free materials.
-
Direct Current Sintering:
- Direct current sintering is an advanced technique where an electrical current is passed through the material, generating heat internally. This method allows for precise temperature control and uniform heating, resulting in high-quality sintered products with minimal defects.
- It is particularly useful for materials with high melting points, such as tungsten and molybdenum, where traditional sintering methods may be less effective.
-
Benefits of Sintering:
- Improved Material Properties: Sintering enhances strength, durability, and density by reducing porosity and fusing particles.
- Resource Efficiency: The process optimizes raw material usage and reduces waste, aligning with principles of sustainability.
- Versatility: Sintering can be applied to a wide range of materials, including metals, ceramics, and composites, making it a versatile manufacturing technique.
By understanding the principles and applications of sintering, particularly direct current sintering, manufacturers can produce high-performance materials and components with precision and efficiency.
Summary Table:
Aspect | Details |
---|---|
Definition | A process using electrical current to generate internal heat for sintering. |
Key Benefit | Precise temperature control and uniform heating. |
Applications | Ideal for high-melting-point materials like tungsten and molybdenum. |
Advantages | High-quality products, minimal defects, and improved material properties. |
Industries | Powder metallurgy, ceramics, and steel production. |
Ready to enhance your material manufacturing process? Contact our experts today to learn more about direct current sintering!