A dual track induction furnace is a specialized type of induction furnace designed for efficient and continuous metal melting processes. It utilizes two separate tracks or chambers, allowing for simultaneous operations such as melting and holding, or melting and alloying. This design enhances productivity by reducing downtime and improving temperature control. The furnace operates by generating an electromagnetic field within a copper coil, which induces eddy currents in the metal charge, producing heat directly within the metal. This method ensures clean, energy-efficient, and precise melting, making it ideal for industries requiring high-quality metal production with minimal contamination. The dual track system also supports flexibility in processing different metals or alloys, making it a versatile solution for various industrial applications.
Key Points Explained:
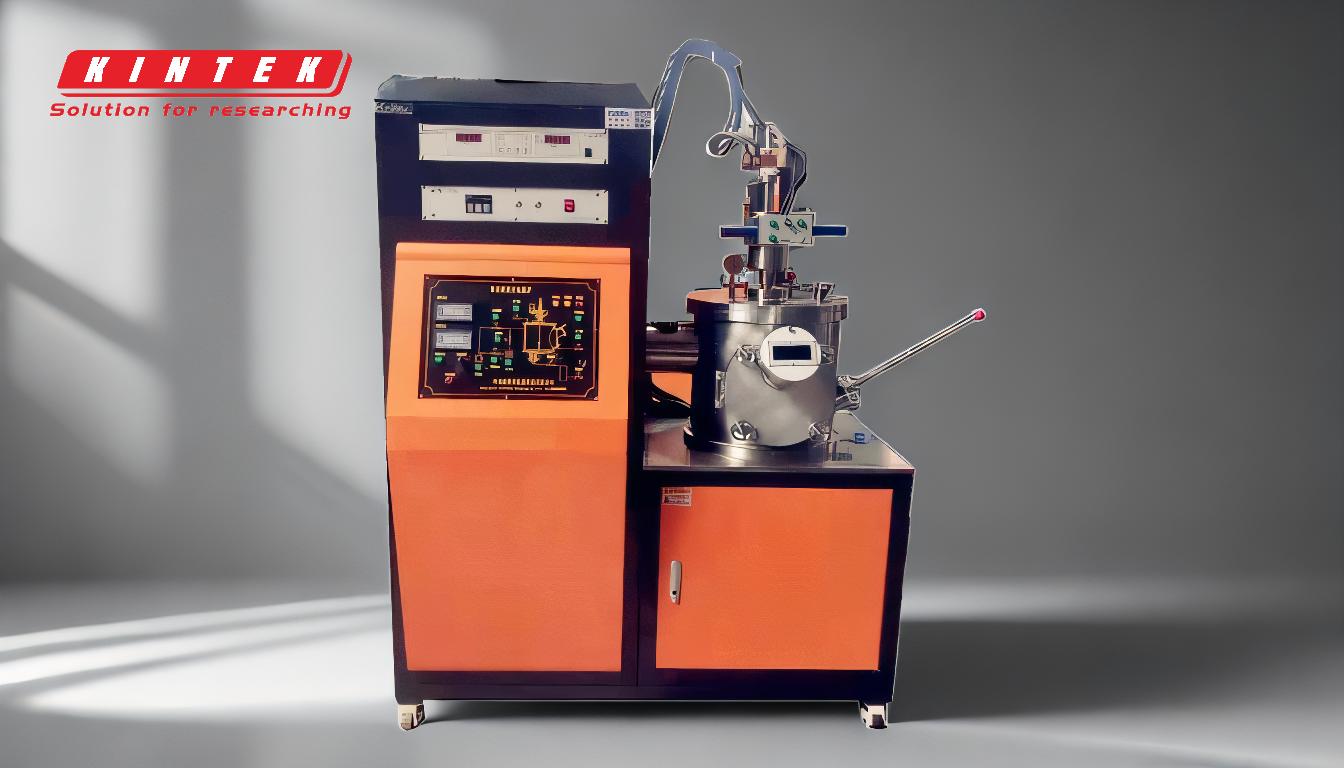
-
Definition and Functionality of a Dual Track Induction Furnace:
- A dual track induction furnace is an advanced melting system featuring two separate tracks or chambers.
- It enables simultaneous operations, such as melting in one track while holding or alloying in the other.
- This design minimizes downtime and maximizes productivity, making it suitable for continuous industrial processes.
-
Working Principle:
- The furnace operates using an induction power unit that generates an electromagnetic field within a hollow copper coil.
- The electromagnetic field induces eddy currents in the conductive metal charge, producing heat directly within the metal.
- This method ensures rapid and efficient melting with precise temperature control.
-
Advantages of Dual Track Design:
- Enhanced Productivity: The dual track system allows for continuous operation, reducing idle time between batches.
- Flexibility: It supports the processing of different metals or alloys simultaneously, catering to diverse industrial needs.
- Improved Temperature Control: The separation of melting and holding/alloying processes ensures consistent and accurate temperature management.
-
Environmental and Operational Benefits:
- Energy Efficiency: Induction furnaces are known for their low energy consumption and minimal heat loss.
- Clean Melting Process: The absence of combustion or arc reduces contamination, preserving the quality of the metal.
- Reduced Waste: The precise control over the melting process minimizes material loss and pollutants, contributing to a smaller carbon footprint.
-
Applications and Suitability:
- Dual track induction furnaces are ideal for industries requiring high-quality metal production, such as automotive, aerospace, and foundries.
- They are particularly beneficial for small to medium-sized businesses due to their scalability and availability in various sizes.
-
Comparison with Single Track Induction Furnaces:
- While single track furnaces are simpler and more cost-effective, dual track furnaces offer greater efficiency and flexibility for continuous operations.
- The dual track design is better suited for applications requiring frequent alloy changes or high-volume production.
By combining the principles of induction heating with a dual track system, this furnace type provides a robust solution for modern metal melting needs, balancing efficiency, precision, and environmental sustainability.
Summary Table:
Feature | Dual Track Induction Furnace |
---|---|
Design | Two separate tracks/chambers for simultaneous operations (melting, holding, alloying). |
Working Principle | Electromagnetic field induces eddy currents in metal, producing heat directly within the charge. |
Advantages | - Enhanced productivity - Flexibility in processing metals/alloys - Improved temperature control |
Environmental Benefits | - Energy-efficient - Clean melting process - Reduced waste and carbon footprint |
Applications | Ideal for automotive, aerospace, and foundries; scalable for small to medium-sized businesses. |
Comparison with Single Track | Greater efficiency and flexibility for continuous operations and frequent alloy changes. |
Ready to optimize your metal melting process? Contact us today to learn more about dual track induction furnaces!