Hydrogen brazing is a specialized brazing process that utilizes hydrogen as a deoxidizing agent to create a clean and oxide-free environment for joining metals. This process is particularly effective for reducing oxides of metals like iron, copper, nickel, and cobalt, which enhances the quality and strength of the brazed joint. However, hydrogen brazing is less effective for metals with stable oxides, such as aluminum, beryllium, titanium, and silicon, which may require alternative methods like vacuum brazing or the use of inert gases like helium or argon. The process is often carried out in a hydrogen atmosphere furnace, where hydrogen serves as both a heating medium and a protective atmosphere, ensuring optimal conditions for brazing.
Key Points Explained:
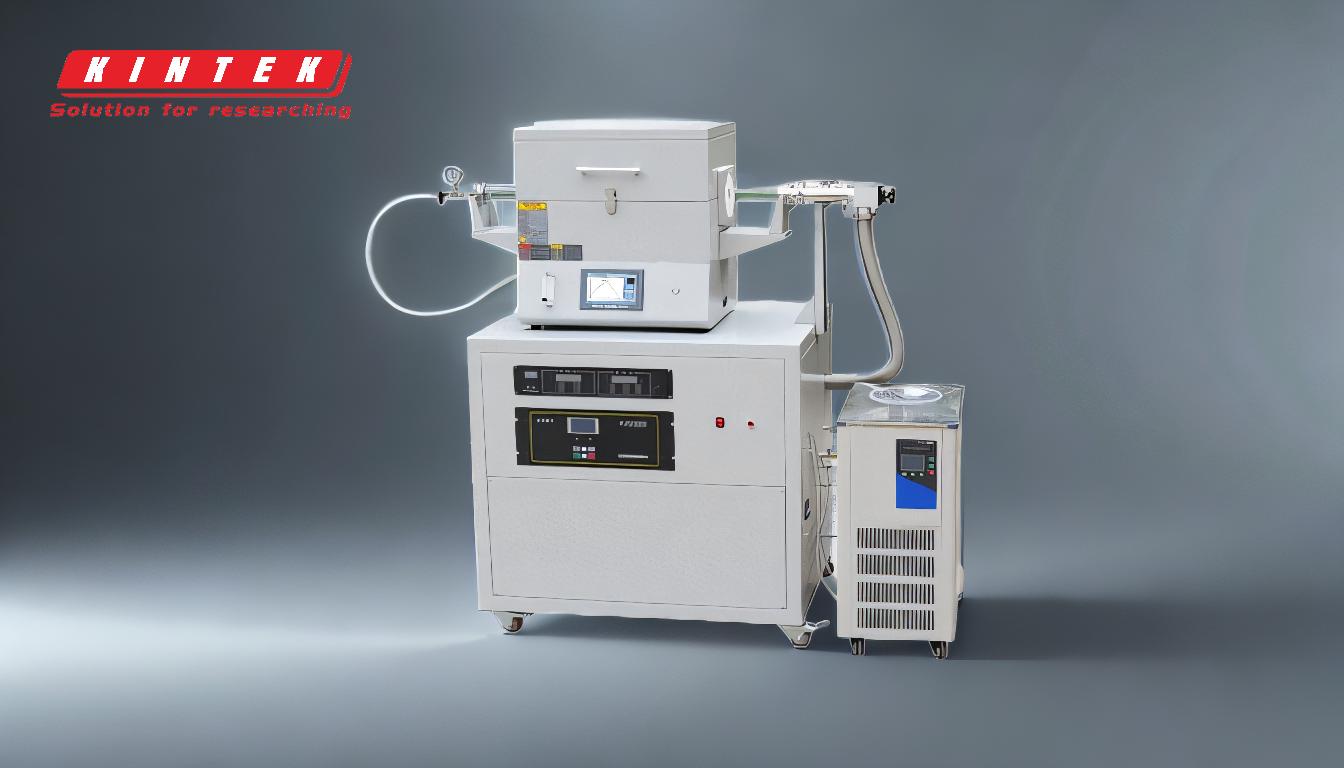
-
Role of Hydrogen in Brazing:
- Hydrogen acts as a deoxidizer in the brazing process, effectively reducing oxides on the surface of metals like iron, copper, nickel, and cobalt. This reduction of oxides is crucial for achieving strong and clean brazed joints.
- The deoxidizing properties of hydrogen help in creating a clean surface, which is essential for proper wetting and bonding of the brazing filler material.
-
Limitations of Hydrogen Brazing:
- While hydrogen is effective for reducing many metal oxides, it is less effective with oxides of aluminum, beryllium, titanium, and silicon. These metals form highly stable oxides that are not easily reduced by hydrogen.
- For such metals, alternative brazing methods like vacuum brazing or the use of inert gases (helium or argon) are more suitable. These methods prevent oxidation and ensure a clean brazing environment.
-
Hydrogen Atmosphere Furnace:
- The hydrogen atmosphere furnace is a key piece of equipment used in hydrogen brazing. It provides a controlled environment where hydrogen is used as the heating medium and protective atmosphere.
- The furnace operates at high temperatures, and the hydrogen atmosphere ensures that the materials being brazed are free from oxidation, which is critical for achieving high-quality brazed joints.
-
Advantages of Hydrogen Brazing:
- Hydrogen brazing offers several advantages, including the ability to produce clean, oxide-free joints with high strength and reliability.
- The process is particularly beneficial for joining metals that are prone to oxidation, as the hydrogen atmosphere effectively prevents the formation of oxides during the brazing process.
-
Applications of Hydrogen Brazing:
- Hydrogen brazing is widely used in industries where high-quality, oxidation-free joints are required. This includes applications in the aerospace, automotive, and electronics industries.
- The process is also used in the production of components that require precise and reliable joints, such as heat exchangers, vacuum tubes, and semiconductor devices.
-
Safety Considerations:
- Handling hydrogen requires strict safety precautions due to its flammability and explosive nature. Proper ventilation, leak detection, and safety protocols must be in place to ensure safe operation during hydrogen brazing.
- The use of hydrogen atmosphere furnaces also requires careful monitoring and control to prevent any potential hazards associated with hydrogen gas.
In summary, hydrogen brazing is a highly effective method for joining metals, particularly those that are prone to oxidation. The use of hydrogen as a deoxidizer and the controlled environment of a hydrogen atmosphere furnace ensure the production of strong, clean, and reliable brazed joints. However, for metals with highly stable oxides, alternative brazing methods may be necessary.
Summary Table:
Aspect | Details |
---|---|
Process | Uses hydrogen as a deoxidizing agent to create a clean, oxide-free environment. |
Effective For | Metals like iron, copper, nickel, and cobalt. |
Limitations | Less effective for metals with stable oxides (e.g., aluminum, titanium). |
Equipment | Hydrogen atmosphere furnace for controlled, high-temperature brazing. |
Advantages | Produces clean, strong, and reliable joints; prevents oxidation. |
Applications | Aerospace, automotive, electronics, heat exchangers, and semiconductor devices. |
Safety | Requires strict precautions due to hydrogen's flammability and explosiveness. |
Discover how hydrogen brazing can enhance your metal joining processes—contact our experts today!