To achieve optimal brazing results, several critical factors must be carefully managed. These include the selection of the appropriate filler metal with the correct melting temperature, ensuring clean joint surfaces, precise mechanical processing to create the correct gap dimensions, and careful control of the brazing process to avoid overheating the base material. Additionally, the brazing material should have properties that match the parent material, including chemical stability and corrosion resistance. The type of brazing machine and process used also play a significant role in achieving high-quality brazed joints.
Key Points Explained:
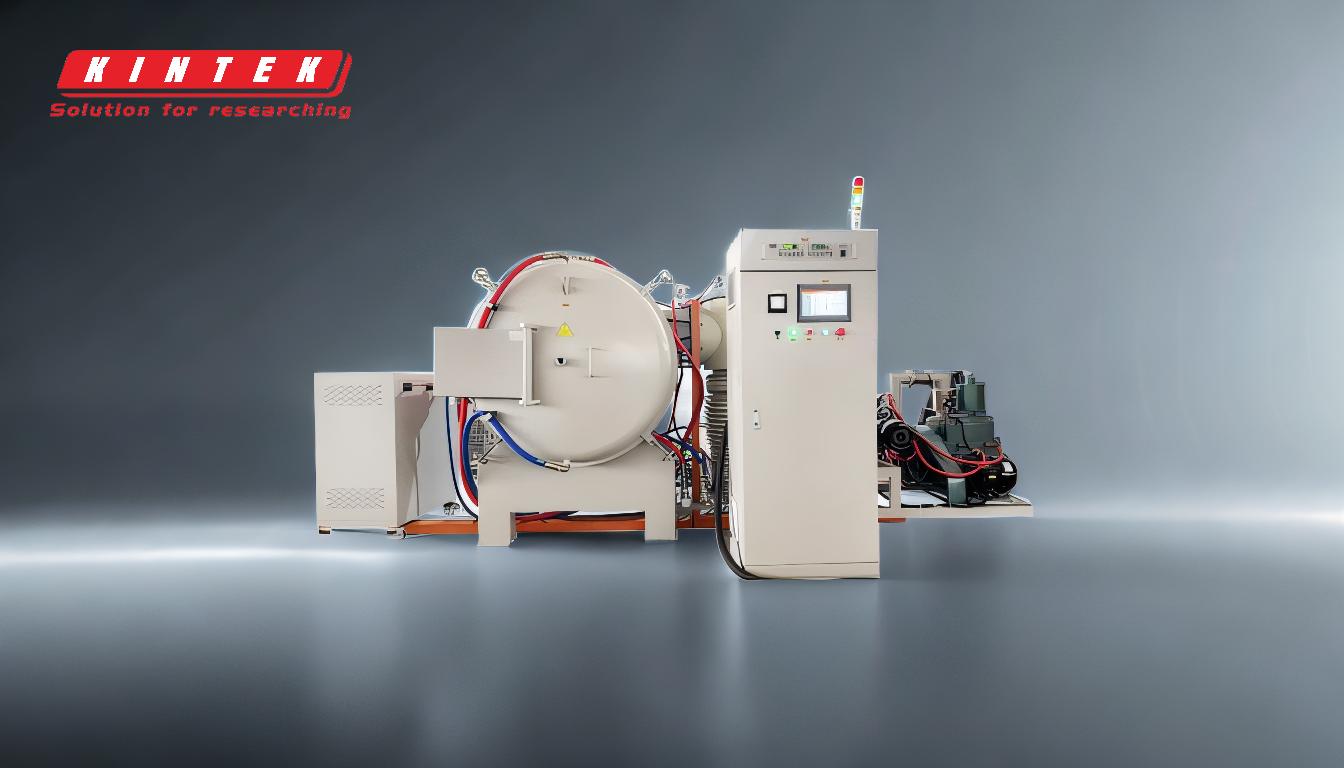
-
Filler Metal Selection:
- The filler metal must have a specific melting temperature that allows it to melt and flow properly within the joint cavity. This ensures good wetting and spreading, which are essential for a strong bond.
- The alloy used should have a melting temperature that is significantly lower than that of the metals being joined but still provides suitable mechanical characteristics for the joint.
- The brazing material should have a small difference between its solidus and liquidus temperatures to ensure uniform melting and solidification.
-
Joint Surface Preparation:
- Cleanliness of the joint surfaces is paramount. Any contamination, such as oils or greases, can hinder the wetting ability of the filler metal, leading to poor joint quality.
- Proper cleaning methods, such as degreasing or chemical cleaning, should be employed to ensure that the surfaces are free from any contaminants.
-
Mechanical Processing:
- Precise mechanical processing is required to create the correct gap dimensions between the parts being joined. The gap size is critical as it affects the capillary action, which is necessary for the filler metal to flow and fill the joint properly.
- The gap should be neither too wide nor too narrow; an optimal gap ensures that the filler metal can flow and distribute evenly within the joint.
-
Brazing Process Control:
- Care must be taken to avoid overheating the base material. Overheating can lead to damage or deformation of the base material, especially since the melting point of the brazing flux is close to that of the base material.
- The flame of the brazing torch should be controlled to be a weak reducing flame, which helps in minimizing oxidation and ensuring a clean joint.
-
Brazing Material Properties:
- The main components of the brazing material should match those of the parent material to ensure good corrosion resistance and chemical stability.
- The brazing material should exhibit high chemical stability at the brazing temperature, including low oxidation properties and low vapor pressure.
- The liquidus temperature of the brazing material should be at least 30°C lower than the solidus temperature of the parent material. A smaller temperature difference requires higher precision in furnace temperature control and uniformity.
-
Brazing Machine and Process Selection:
- The choice of brazing machine and process should be based on the specific requirements of the job, including the type of brazing process and the application.
- Different types of brazing machines offer various advantages, and selecting the right one can significantly impact the quality of the brazed joints.
By carefully considering these factors and ensuring that each step of the brazing process is meticulously controlled, optimal brazing results can be achieved, leading to strong, durable, and high-quality brazed joints.
Summary Table:
Key Factor | Description |
---|---|
Filler Metal Selection | Choose a filler metal with the correct melting temperature and small solidus-liquidus gap. |
Joint Surface Preparation | Ensure surfaces are clean and free from contaminants for proper wetting and bonding. |
Mechanical Processing | Create precise gap dimensions to enable proper capillary action and filler flow. |
Brazing Process Control | Avoid overheating the base material and use a weak reducing flame for oxidation control. |
Brazing Material Properties | Match material properties with the parent material for corrosion resistance and stability. |
Brazing Machine Selection | Select the right brazing machine and process based on application requirements. |
Achieve flawless brazing results—contact our experts today for tailored solutions!