Regenerated carbon, also known as reactivated carbon, is a type of activated carbon that has undergone a regeneration process to restore its adsorption properties after it has been used and saturated with adsorbed materials. This process involves removing the adsorbed contaminants from the carbon's surface through physical or chemical methods, without damaging its original porous structure. The goal of regeneration is to make the carbon reusable, offering a cost-effective and environmentally sustainable alternative to disposing of spent carbon and purchasing new material. Regenerated carbon retains its adsorption capacity, making it suitable for reuse in various applications such as water purification, air filtration, and industrial processes.
Key Points Explained:
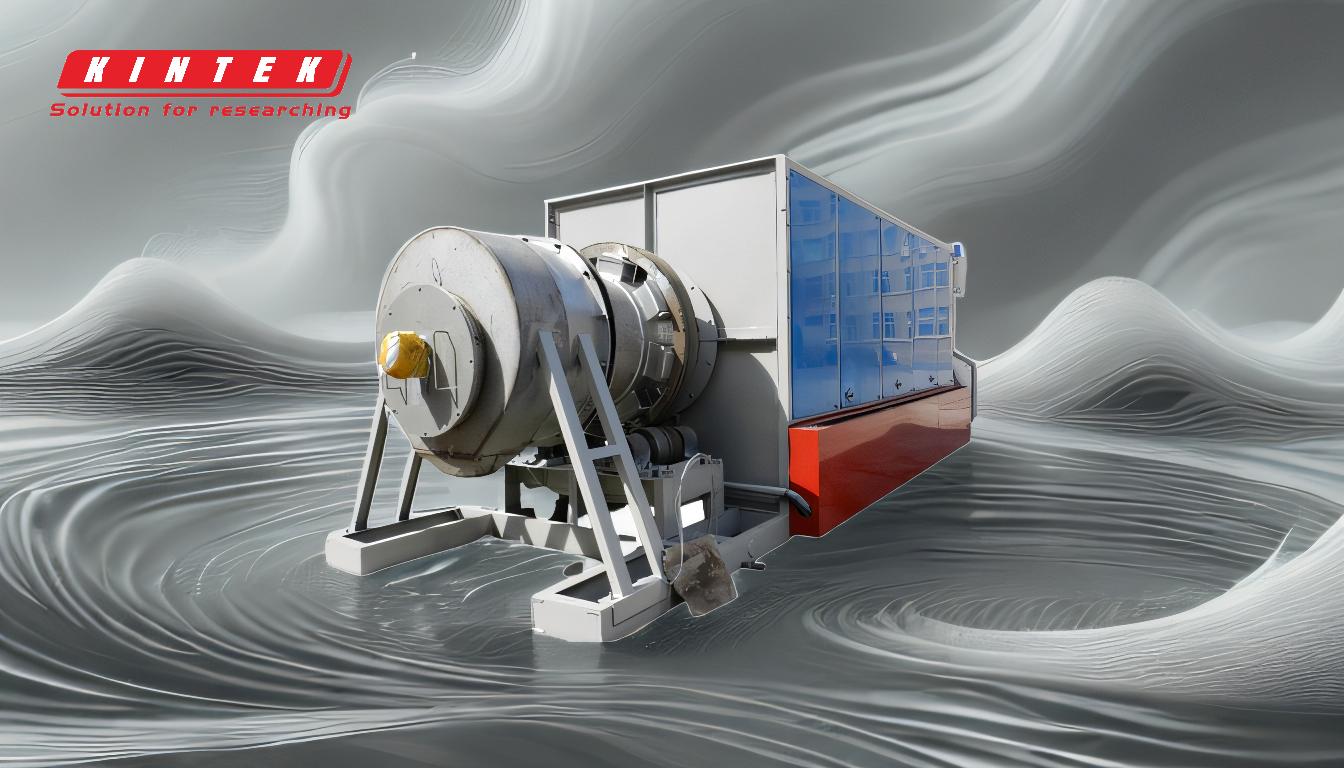
-
Definition of Regenerated Carbon:
- Regenerated carbon is activated carbon that has been treated to remove adsorbed contaminants and restore its adsorption capabilities. This process allows the carbon to be reused multiple times, extending its lifecycle and reducing waste.
-
Regeneration Process:
- The regeneration process involves physical or chemical methods to remove adsorbed materials from the carbon's surface. Common techniques include thermal regeneration, chemical washing, and steam reactivation.
- Thermal Regeneration: This method involves heating the spent carbon in a controlled environment (e.g., a furnace) to high temperatures (600–900°C) to vaporize and burn off the adsorbed contaminants.
- Chemical Regeneration: Chemicals are used to desorb contaminants from the carbon, often followed by rinsing to remove residual chemicals.
- Steam Reactivation: Steam is passed through the carbon bed to strip away adsorbed materials, often used in combination with thermal methods.
-
Preservation of Carbon Structure:
- A key aspect of regeneration is ensuring that the original porous structure of the activated carbon is not damaged during the process. This structure is critical for maintaining the carbon's high surface area and adsorption capacity.
-
Applications of Regenerated Carbon:
- Regenerated carbon is reused in various industries, including:
- Water Treatment: For removing organic contaminants, chlorine, and heavy metals from drinking water and wastewater.
- Air Purification: For capturing volatile organic compounds (VOCs) and odors in air filtration systems.
- Industrial Processes: For solvent recovery, gas purification, and catalysis in manufacturing.
- Regenerated carbon is reused in various industries, including:
-
Benefits of Regenerated Carbon:
- Cost-Effectiveness: Regeneration is often more economical than purchasing new activated carbon, especially for large-scale operations.
- Sustainability: Reusing carbon reduces waste and minimizes the environmental impact associated with producing and disposing of activated carbon.
- Performance: Properly regenerated carbon can achieve adsorption performance comparable to virgin activated carbon.
-
Challenges in Regeneration:
- Loss of Adsorption Capacity: Over multiple regeneration cycles, the carbon may experience a gradual decline in adsorption efficiency due to structural changes or incomplete removal of contaminants.
- Energy Consumption: Thermal regeneration, in particular, requires significant energy input, which can offset some of the environmental benefits.
- Contaminant Residues: Certain contaminants may not be fully removed during regeneration, potentially affecting the carbon's performance in subsequent uses.
-
Comparison with Virgin Activated Carbon:
- Virgin activated carbon is newly produced and has never been used, offering maximum adsorption capacity. Regenerated carbon, while cost-effective and sustainable, may have slightly reduced adsorption performance depending on the regeneration process and the nature of the contaminants.
In summary, regenerated carbon is a sustainable and cost-effective solution for industries that rely on activated carbon for adsorption processes. By restoring the carbon's adsorption properties through regeneration, it can be reused multiple times, reducing waste and environmental impact while maintaining performance. However, careful consideration of the regeneration method and potential challenges is necessary to ensure optimal results.
Summary Table:
Aspect | Details |
---|---|
Definition | Activated carbon treated to remove contaminants and restore adsorption. |
Regeneration Methods | Thermal, chemical, and steam reactivation. |
Applications | Water treatment, air purification, industrial processes. |
Benefits | Cost-effective, sustainable, retains adsorption capacity. |
Challenges | Gradual capacity loss, high energy use, potential contaminant residues. |
Comparison | Slightly reduced performance vs. virgin carbon, but more sustainable. |
Interested in sustainable adsorption solutions? Contact us today to learn more about regenerated carbon!