Spark Plasma Sintering (SPS) is an advanced powder metallurgy technique that uses pulsed direct current (DC) to rapidly densify materials at lower temperatures and shorter times compared to conventional sintering methods. The process involves applying a high-energy pulsed current to powder particles, generating localized high temperatures (up to 10,000°C) and plasma, which removes impurities and activates particle surfaces. This results in rapid heating, melting, and fusion of particle interfaces, forming dense structures with over 99% solid density. SPS is also known as Field-Assisted Sintering Technique (FAST) or Electric Field-Assisted Sintering (EFAS) and is widely used for producing high-quality metal, ceramic, and composite materials.
Key Points Explained:
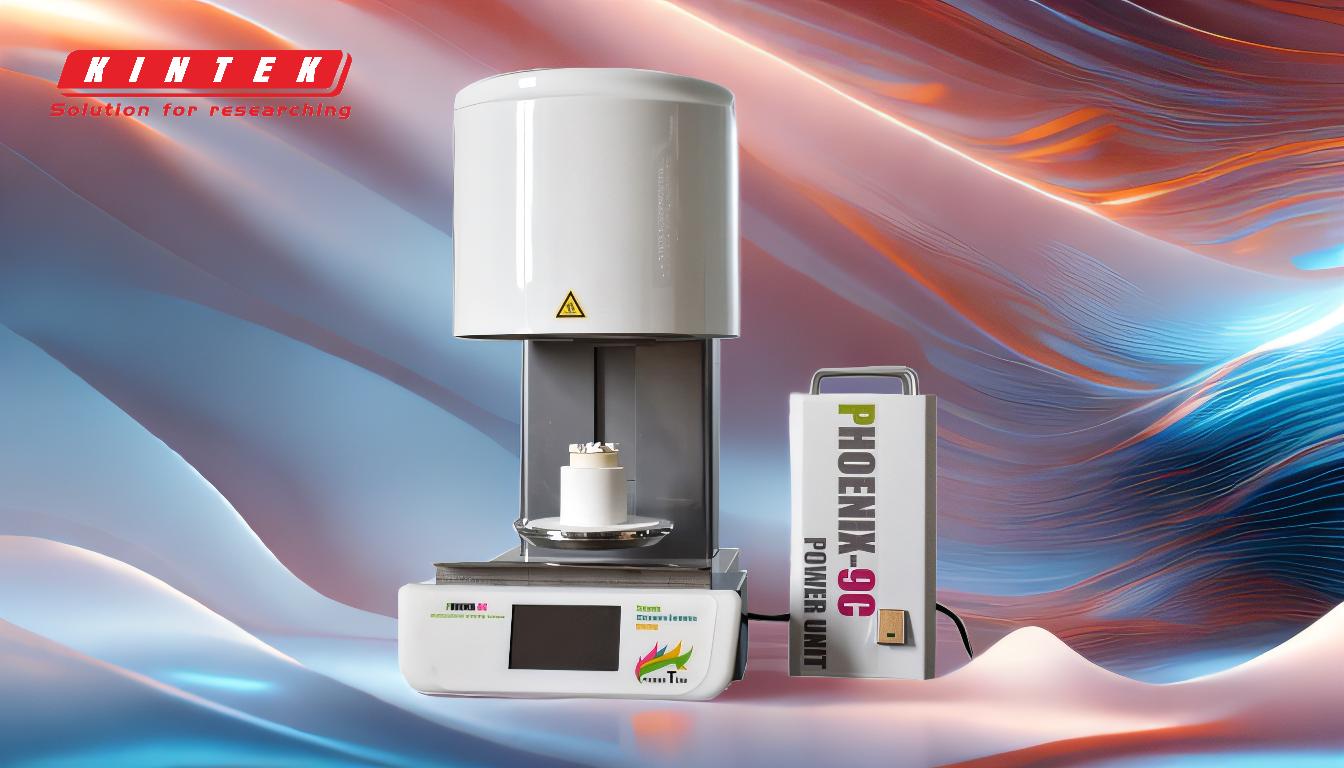
-
Principle of Spark Plasma Sintering (SPS):
- SPS works by applying a pulsed DC current directly to powder particles, generating electric spark discharge and plasma.
- The high-energy pulses create localized temperatures of up to 10,000°C, which removes contaminants and activates particle surfaces.
- This process facilitates rapid densification by melting and fusing particle interfaces, forming dense structures called "necks."
-
Heating Mechanism:
- The pulsed current passes through a conductive graphite die and, if applicable, through the material itself.
- The die acts as an external heat source, while the material is heated internally by the electric current.
- This dual heating mechanism allows for extremely rapid heating and cooling rates, reducing sintering times significantly.
-
Advantages of SPS:
- Lower Sintering Temperatures: SPS achieves densification at temperatures several hundred degrees lower than conventional sintering methods.
- Shorter Processing Times: Rapid heating and cooling rates enable sintering in minutes rather than hours.
- High Density and Quality: The process produces materials with over 99% solid density and minimal impurities.
- Versatility: SPS can be used for metals, ceramics, and composite materials.
-
Applications of SPS:
- Ceramics: SPS is used to produce dense ceramic materials, such as silicon carbide (SiC) with sintering aids like Al2O3 and Y2O3.
- Metals: It is effective for sintering metallic powders into high-density components.
- Composites: SPS enables the fabrication of complex composite materials with enhanced properties.
-
Misconceptions About SPS:
- Despite its name, research has shown that no plasma is generated during the process. Alternative names like Field-Assisted Sintering Technique (FAST) or Direct Current Sintering (DCS) are more accurate.
- The term "spark plasma" is derived from the localized high temperatures and spark discharge effects, not the presence of plasma.
-
Process Control and Parameters:
- Key parameters include pulse current intensity, heating rate, pressure applied, and holding time.
- Precise control of these parameters ensures optimal densification and material properties.
-
Comparison with Conventional Sintering:
- Conventional sintering relies on external heating sources and longer processing times, often resulting in lower density and higher impurity levels.
- SPS offers superior control over microstructure and material properties due to its rapid and localized heating mechanism.
-
Challenges and Limitations:
- Material Conductivity: Materials with low electrical conductivity may require conductive dies or additives to facilitate the process.
- Equipment Cost: SPS systems are more expensive than conventional sintering setups.
- Scalability: While SPS is effective for laboratory-scale production, scaling up for industrial applications remains a challenge.
In summary, Spark Plasma Sintering is a cutting-edge technique that leverages pulsed electric currents to achieve rapid, high-quality densification of materials. Its ability to operate at lower temperatures and shorter times makes it a valuable tool for producing advanced materials with superior properties. However, challenges related to cost and scalability must be addressed for broader industrial adoption.
Summary Table:
Aspect | Details |
---|---|
Principle | Pulsed DC current generates localized high temps (up to 10,000°C), removes impurities, and activates particle surfaces. |
Heating Mechanism | Dual heating: external (graphite die) and internal (electric current). |
Advantages | Lower temps, shorter times, high density (99%+), and versatility for metals, ceramics, and composites. |
Applications | Ceramics (e.g., SiC), metals, and composite materials. |
Misconceptions | No actual plasma is generated; alternative names include FAST or EFAS. |
Process Control | Key parameters: pulse current, heating rate, pressure, and holding time. |
Challenges | Material conductivity, high equipment cost, and scalability limitations. |
Learn how Spark Plasma Sintering can transform your material production—contact us today!