The batch process for heat treating involves a systematic approach to altering the physical and mechanical properties of materials, primarily metals and plastics, through controlled heating and cooling. This process is essential for achieving desired characteristics such as hardness, softness, stress relief, and resilience. The batch process typically includes three fundamental steps: heating the material to a specified temperature, maintaining that temperature for a predetermined duration, and cooling the material using specific methods. Each step is carefully controlled to ensure the material achieves the desired properties, with temperatures potentially reaching up to 2,400°F and holding times ranging from seconds to several hours. The batch process is versatile, accommodating various heat treatment techniques like annealing, hardening, and stress relief, tailored to the material and the intended application.
Key Points Explained:
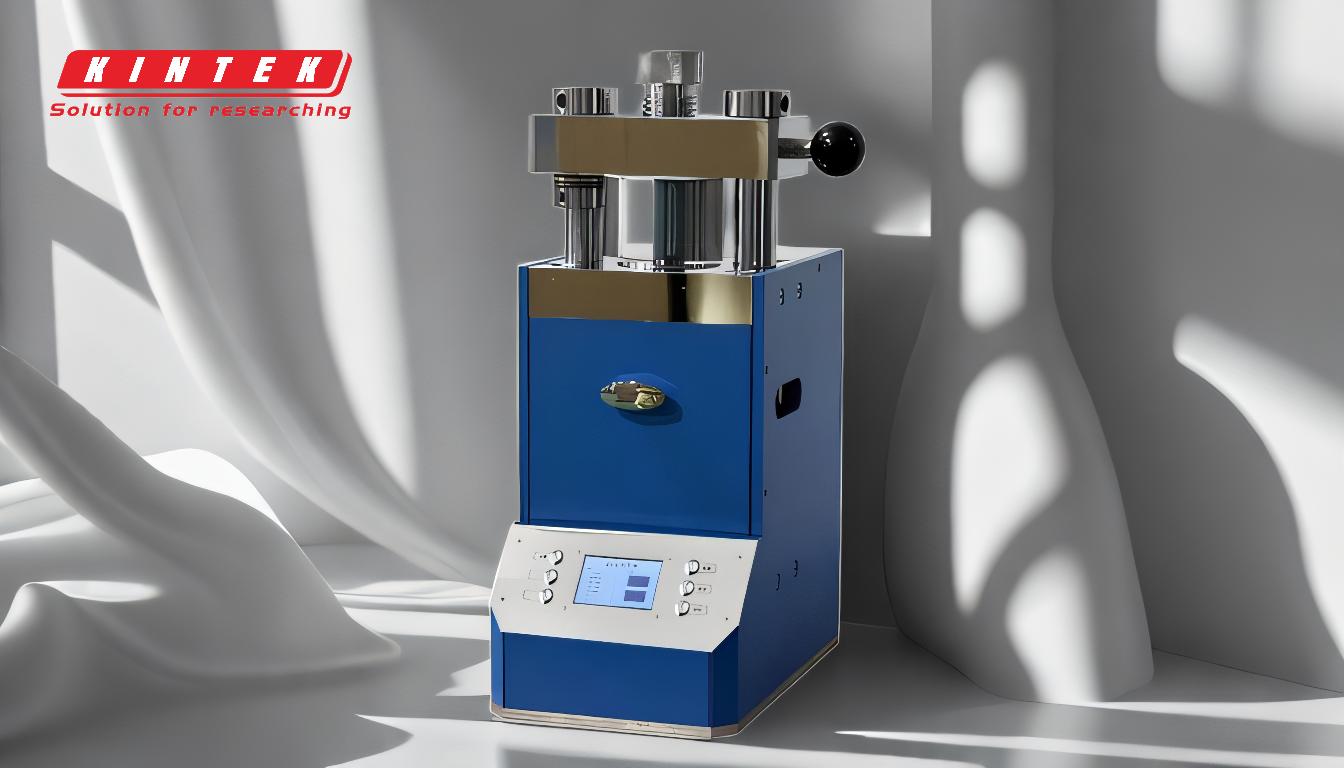
-
Heating to a Specified Temperature:
- Purpose: The first step in the batch process is to heat the material to a specific temperature. This temperature is critical as it determines the material's transformation phase, which is essential for achieving the desired properties.
- Temperature Range: Depending on the material and the desired outcome, temperatures can vary significantly, sometimes reaching as high as 2,400°F. For instance, annealing typically requires lower temperatures compared to hardening processes like carburizing or nitriding.
- Control: Precise temperature control is crucial. Overheating can lead to undesirable grain growth, while insufficient heating may not achieve the necessary phase changes.
-
Holding at Temperature:
- Duration: After reaching the target temperature, the material is held at that temperature for a specific period. The duration can range from a few seconds to several hours, depending on the material and the heat treatment process.
- Purpose: This holding period allows the material to undergo the necessary microstructural changes. For example, in annealing, the material is held at temperature to allow for recrystallization and grain refinement, which softens the material.
- Uniformity: Ensuring that the entire batch of material is uniformly heated and held at the correct temperature is essential for consistent results. Variations can lead to uneven properties within the batch.
-
Cooling According to Prescribed Methods:
- Cooling Rate: The method and rate of cooling are critical in determining the final properties of the material. Different cooling methods, such as air cooling, oil quenching, or water quenching, are used depending on the desired outcome.
- Purpose: Rapid cooling (quenching) is often used to harden metals by trapping the material in a high-strength phase. Slower cooling rates, such as those used in annealing, allow for the development of softer, more ductile structures.
- Control: The cooling process must be carefully controlled to avoid cracking or warping, especially in materials that are sensitive to thermal shock.
-
Types of Heat Treating Processes:
- Annealing: This process involves heating the material to a specific temperature and then slowly cooling it to soften the material, relieve internal stresses, and improve machinability.
- Hardening: Techniques like through hardening, case hardening, carburizing, and nitriding are used to increase the hardness and strength of metals. These processes often involve rapid cooling after heating.
- Stress Relief: This process is used to remove internal stresses from materials that have been formed, extruded, cut, or bent. It typically involves heating the material to a lower temperature and then cooling it slowly.
- Specialized Processes: Techniques like austempering and marquenching are used to add resilience or springiness to metals, while magnetic annealing is used to alter magnetic permeability.
-
Batch Process Considerations:
- Batch Size: The size of the batch can affect the uniformity of the heat treatment. Larger batches may require more sophisticated equipment to ensure even heating and cooling.
- Material Variability: Different materials within the same batch may require slightly different treatment parameters. It's essential to account for these variations to achieve consistent results.
- Equipment: The type of furnace or heating equipment used can impact the efficiency and effectiveness of the batch process. Modern furnaces often come with advanced controls to maintain precise temperatures and cooling rates.
In summary, the batch process for heat treating is a meticulously controlled sequence of heating, holding, and cooling designed to alter the properties of materials to meet specific requirements. Each step must be carefully managed to ensure the material achieves the desired characteristics, making the process both an art and a science.
Summary Table:
Step | Key Details |
---|---|
Heating | - Purpose: Achieve material transformation phase. |
- Temperature Range: Up to 2,400°F. | |
- Control: Precise temperature to avoid grain growth or insufficient heating. | |
Holding at Temp | - Duration: Seconds to hours. |
- Purpose: Enable microstructural changes (e.g., recrystallization). | |
- Uniformity: Ensures consistent results across the batch. | |
Cooling | - Methods: Air, oil, or water quenching. |
- Purpose: Determines final properties (e.g., hardness or ductility). | |
- Control: Prevents cracking or warping. | |
Process Types | - Annealing: Softens material, relieves stress. |
- Hardening: Increases strength via rapid cooling. | |
- Stress Relief: Removes internal stresses. | |
- Specialized: Techniques like austempering or magnetic annealing. | |
Considerations | - Batch Size: Affects uniformity. |
- Material Variability: Adjust parameters for consistency. | |
- Equipment: Advanced furnaces for precise control. |
Optimize your heat treating process—contact our experts today for tailored solutions!