Brazing is a versatile joining process used to bond two or more materials, typically metals or ceramics, by melting a filler material that flows into the gaps between the parts via capillary action. The filler material, which has a lower melting point than the base materials, solidifies upon cooling, creating a strong and durable joint. This process is widely used in industries requiring precision, such as aerospace, automotive, and electronics, due to its ability to join dissimilar materials with minimal deformation and high aesthetic quality. The brazing process involves several critical steps, including cleaning, assembly, heating, and cooling, with variations like furnace brazing and controlled atmosphere brazing offering tailored solutions for specific applications.
Key Points Explained:
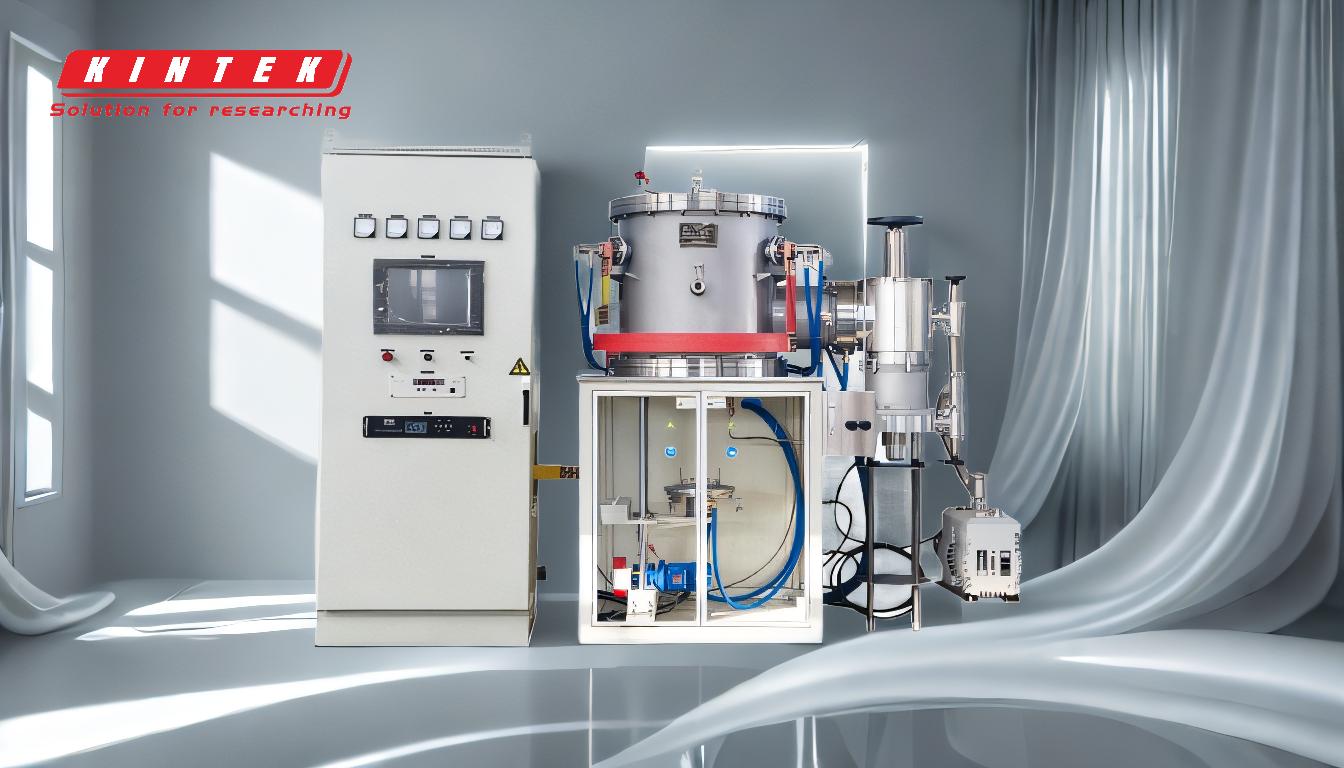
-
Definition and Purpose of Brazing:
- Brazing is a joining process that uses a filler material with a lower melting point than the base materials to create a strong bond.
- It is suitable for joining similar or dissimilar materials, including metals and ceramics, and is valued for its precision and minimal deformation.
-
Filler Materials:
- Common filler materials include alloys of nickel, silver, copper, and other metals.
- The filler material must melt at a temperature lower than the base materials but high enough to ensure proper flow and bonding.
-
Capillary Action:
- The molten filler material flows into the gaps between the parts due to capillary action, ensuring even distribution and strong adhesion.
- Proper joint design and gap width are critical for effective capillary flow.
-
Cleaning and Preparation:
- Cleaning the surfaces to remove oxides, contaminants, and oils is essential for successful brazing.
- Proper surface preparation ensures better wetting and bonding of the filler material.
-
Assembly and Alignment:
- Parts must be precisely aligned and held in place using clamps or fixtures to ensure proper joint formation.
- Misalignment can lead to weak joints or improper filler flow.
-
Heating Methods:
- Furnace Brazing: The entire assembly is heated in a furnace to the filler material's melting point, allowing the filler to flow into the joint. This method is ideal for high-volume production.
- Controlled Atmosphere Brazing: Uses an oxygen-free environment (e.g., nitrogen or hydrogen) to prevent oxidation and ensure clean, strong joints.
- Automatic Brazing Machines: Provide precise temperature control for consistent and accurate results.
-
Cooling and Solidification:
- After the filler material flows into the joint, the assembly is cooled to allow the filler to solidify.
- Rapid cooling can cause distortion or cracking, so controlled cooling is often necessary.
-
Applications and Advantages:
- Brazing is used in industries requiring precision and strength, such as aerospace, automotive, and electronics.
- Advantages include the ability to join dissimilar materials, minimal deformation, and aesthetically pleasing joints.
-
Challenges and Considerations:
- Improper cleaning, heating, or cooling can lead to defects such as poor bonding, distortion, or cracking.
- The furnace cycle, including ramping and stabilization, must be carefully controlled to ensure optimal results.
-
Comparison with Other Joining Methods:
- Unlike welding, brazing does not melt the base materials, reducing the risk of distortion and heat-affected zones.
- It offers greater flexibility in joining dissimilar materials compared to soldering or adhesive bonding.
By understanding these key points, equipment and consumable purchasers can make informed decisions about the brazing process, ensuring they select the right materials and methods for their specific applications.
Summary Table:
Key Aspect | Details |
---|---|
Definition | Joining process using a filler material with a lower melting point. |
Filler Materials | Nickel, silver, copper alloys, etc. |
Capillary Action | Ensures even filler distribution for strong adhesion. |
Cleaning & Preparation | Essential for removing contaminants and ensuring proper bonding. |
Heating Methods | Furnace brazing, controlled atmosphere brazing, and automatic brazing. |
Applications | Aerospace, automotive, electronics, and more. |
Advantages | Joins dissimilar materials, minimal deformation, and aesthetic joints. |
Ready to optimize your joining process? Contact our experts today for tailored brazing solutions!