The heat treatment cycle is a controlled process used to alter the physical and sometimes chemical properties of materials, primarily metals and alloys, to achieve desired characteristics such as increased hardness, improved ductility, or enhanced strength. The cycle typically consists of three fundamental stages: heating the material to a specific temperature, holding it at that temperature for a predetermined time (soaking), and then cooling it according to specified methods. The exact parameters of temperature, time, and cooling rate depend on the material being treated and the desired outcome. Common heat treatment techniques include annealing, tempering, quenching, and case hardening, each tailored to achieve specific material properties.
Key Points Explained:
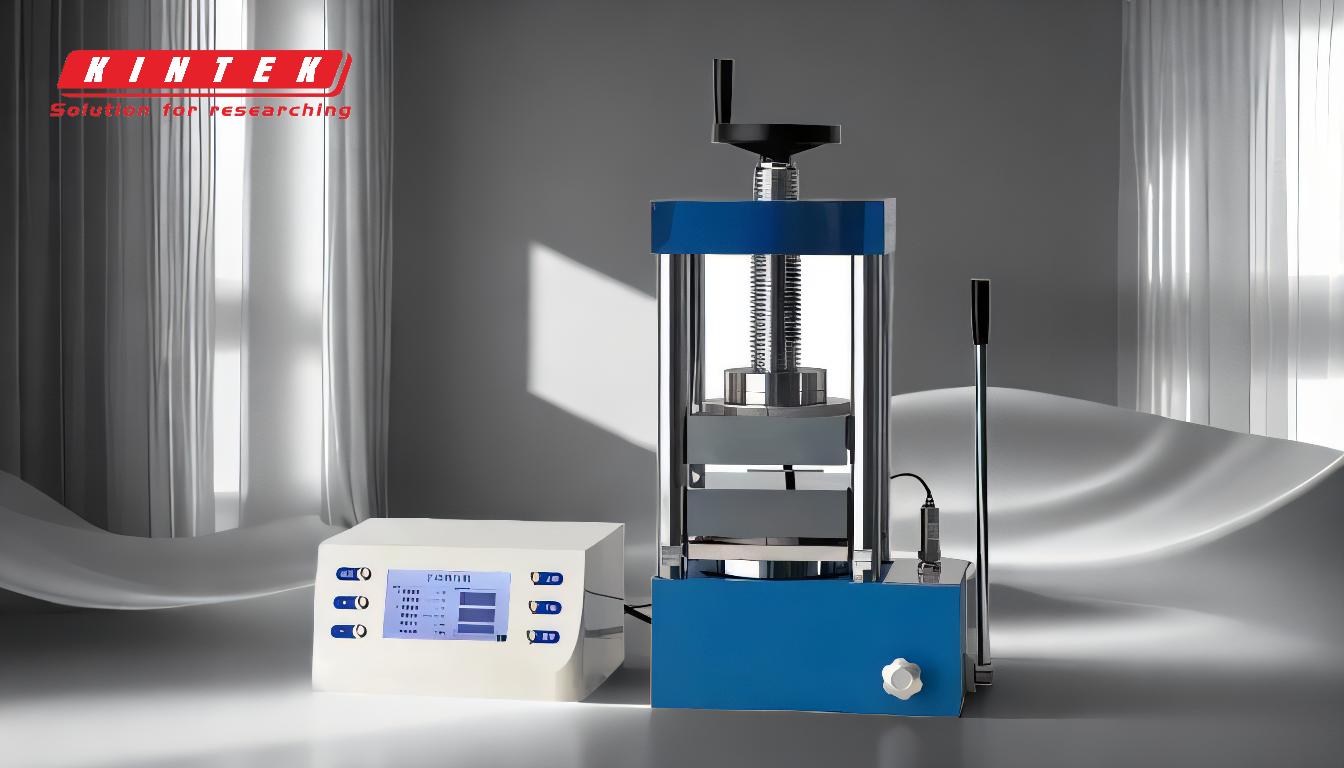
-
Stages of the Heat Treatment Cycle:
- Heating: The material is heated to a specific temperature, which can range from a few hundred degrees to as high as 2,400°F, depending on the material and the desired outcome. This stage ensures the material reaches a uniform temperature to prevent deformation or uneven properties.
- Soaking: The material is held at the target temperature for a specific duration, ranging from seconds to several hours. This step allows the internal structure of the material to transform uniformly, ensuring consistent properties throughout.
- Cooling: The material is cooled according to prescribed methods, such as air cooling, oil quenching, or water quenching. The cooling rate significantly impacts the final properties of the material, such as hardness or ductility.
-
Common Heat Treatment Techniques:
- Annealing: A process that softens metals or changes their physical properties by heating and slow cooling. It reduces internal stresses and improves machinability.
- Tempering: Increases ductility and toughness by reheating quenched or hardened steel to a temperature below its critical point and then cooling it. This reduces brittleness while maintaining strength.
- Quenching: Rapid cooling of heated metal, typically in water, oil, or air, to achieve high hardness and strength. However, this can make the material brittle, which is why tempering often follows.
- Case Hardening: A surface hardening technique, such as carburizing or nitriding, that increases the hardness of the outer layer while maintaining a softer, more ductile core.
- Normalizing: Similar to annealing but involves cooling in air to refine the grain structure and improve mechanical properties.
-
Applications and Outcomes:
- Softening or Hardening: Heat treatment can either soften materials (e.g., annealing) or harden them (e.g., quenching, case hardening).
- Stress Relief: Heat treatment can remove internal stresses caused by machining, forming, or welding, improving the material's stability and performance.
- Enhanced Properties: Processes like tempering and austempering can improve toughness, resilience, and magnetic permeability.
-
Importance of Controlled Parameters:
- Temperature: Precise temperature control is critical to achieving the desired material properties. Overheating or underheating can lead to defects or suboptimal results.
- Time: The duration of heating and soaking must be carefully controlled to ensure uniform transformation of the material's internal structure.
- Cooling Rate: The cooling method directly affects the material's final properties. Rapid cooling (quenching) increases hardness but may cause brittleness, while slow cooling (annealing) enhances ductility.
-
Specialized Heat Treatment Methods:
- Bright Annealing: Minimizes oxidation by using inert atmospheres like hydrogen, nitrogen, or argon, preserving the material's surface finish.
- Sintering: Used in powder metallurgy, this process heats metals to just below their melting point in a protective atmosphere to bond particles.
- Induction and Flame Hardening: Localized heat treatment methods that harden specific areas of a part, useful for components requiring varying properties in different sections.
-
Industry-Specific Applications:
- Aerospace: Heat treatment is critical for ensuring the strength, durability, and reliability of aerospace components. The cycle often includes precise heating, soaking, and cooling to meet stringent performance standards.
- Automotive: Heat treatment enhances the wear resistance and strength of engine components, gears, and drivetrain parts.
- Tool Manufacturing: Tools and dies undergo heat treatment to achieve high hardness and wear resistance, extending their service life.
By understanding the heat treatment cycle and its various techniques, manufacturers can tailor the process to achieve specific material properties, ensuring optimal performance for a wide range of applications.
Summary Table:
Aspect | Details |
---|---|
Stages | Heating, Soaking, Cooling |
Common Techniques | Annealing, Tempering, Quenching, Case Hardening, Normalizing |
Applications | Softening, Hardening, Stress Relief, Enhanced Properties |
Controlled Parameters | Temperature, Time, Cooling Rate |
Specialized Methods | Bright Annealing, Sintering, Induction and Flame Hardening |
Industry Applications | Aerospace, Automotive, Tool Manufacturing |
Optimize your material properties with expert heat treatment solutions—contact us today!