Ceramics are a class of materials known for their exceptional properties, including high temperature resistance, corrosion resistance, good insulation, high abrasion resistance, and oxidation resistance. These properties make ceramics suitable for a wide range of applications, from industrial machinery to household items. One of the key characteristics of ceramics is their density, which plays a significant role in determining their performance in various applications. Density is a measure of how tightly packed the atoms or molecules are within a material, and it directly influences properties such as strength, thermal conductivity, and weight.
Key Points Explained:
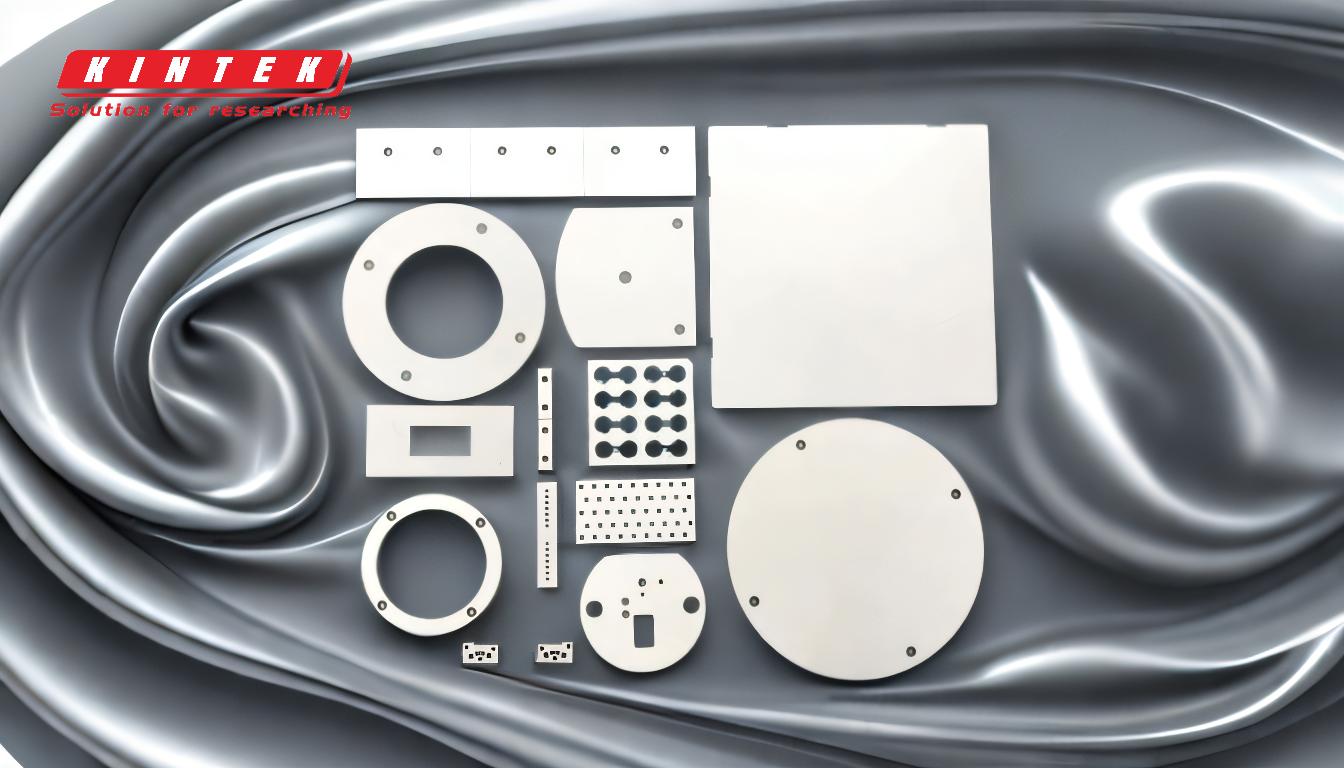
-
Definition of Density in Ceramics:
- Density is defined as the mass per unit volume of a material. For ceramics, this is typically measured in grams per cubic centimeter (g/cm³) or kilograms per cubic meter (kg/m³).
- The density of ceramics can vary widely depending on the type of ceramic and its composition. For example, alumina ceramics have a density of about 3.95 g/cm³, while zirconia ceramics can have a density of up to 6.05 g/cm³.
-
Factors Influencing Ceramic Density:
- Composition: The chemical composition of the ceramic material significantly affects its density. For instance, ceramics with a higher percentage of heavy elements like zirconium will generally have a higher density.
- Porosity: The presence of pores or voids within the ceramic material can reduce its overall density. High-density ceramics are typically those with minimal porosity.
- Processing Techniques: The method used to manufacture the ceramic, such as sintering or hot pressing, can also influence its density. Processes that minimize porosity and promote densification will result in higher-density ceramics.
-
Importance of Density in Ceramic Applications:
- Mechanical Strength: Higher density generally correlates with greater mechanical strength and durability. This is crucial for applications where the ceramic must withstand significant stress or wear.
- Thermal Conductivity: Density can affect the thermal conductivity of ceramics. Higher-density ceramics often have better thermal conductivity, which is important in applications like heat exchangers or thermal insulators.
- Weight Considerations: In applications where weight is a critical factor, such as aerospace or automotive components, the density of the ceramic material must be carefully considered to balance strength and weight.
-
Typical Density Ranges for Common Ceramics:
- Alumina (Al₂O₃): 3.95 g/cm³
- Zirconia (ZrO₂): 5.68 - 6.05 g/cm³
- Silicon Carbide (SiC): 3.10 - 3.21 g/cm³
- Boron Carbide (B₄C): 2.52 g/cm³
- Tungsten Carbide (WC): 15.63 g/cm³
-
Measurement of Ceramic Density:
- Archimedes' Principle: This is a common method for measuring the density of ceramics. It involves submerging the ceramic in a liquid and measuring the displacement to determine the volume, then calculating the density based on the mass and volume.
- Pycnometry: This technique uses a gas pycnometer to measure the volume of a ceramic sample by detecting the pressure change when a gas is introduced into a chamber containing the sample.
-
Applications Based on Density:
- High-Density Ceramics: Used in applications requiring high strength and durability, such as cutting tools, armor plating, and wear-resistant components.
- Low-Density Ceramics: Often used in applications where weight reduction is critical, such as in aerospace components or lightweight structural materials.
Understanding the density of ceramic properties is essential for selecting the right material for specific applications. By considering factors such as composition, porosity, and processing techniques, engineers and designers can optimize the performance of ceramic materials in various industries.
Summary Table:
Ceramic Type | Density (g/cm³) |
---|---|
Alumina (Al₂O₃) | 3.95 |
Zirconia (ZrO₂) | 5.68 - 6.05 |
Silicon Carbide (SiC) | 3.10 - 3.21 |
Boron Carbide (B₄C) | 2.52 |
Tungsten Carbide (WC) | 15.63 |
Need help selecting the right ceramic material for your application? Contact our experts today!