Vertical and horizontal furnaces differ primarily in their orientation, heating chamber design, heat transfer mechanisms, and suitability for specific applications. Vertical furnaces, particularly upflow models, are known for their energy efficiency and uniform temperature distribution, making them ideal for processes requiring consistent heating. Horizontal furnaces, on the other hand, are often preferred in high-performance production environments due to their unique heating chamber design, though they may experience slight temperature variations along the sample length. Both types have distinct advantages and limitations, depending on the intended use case and operational requirements.
Key Points Explained:
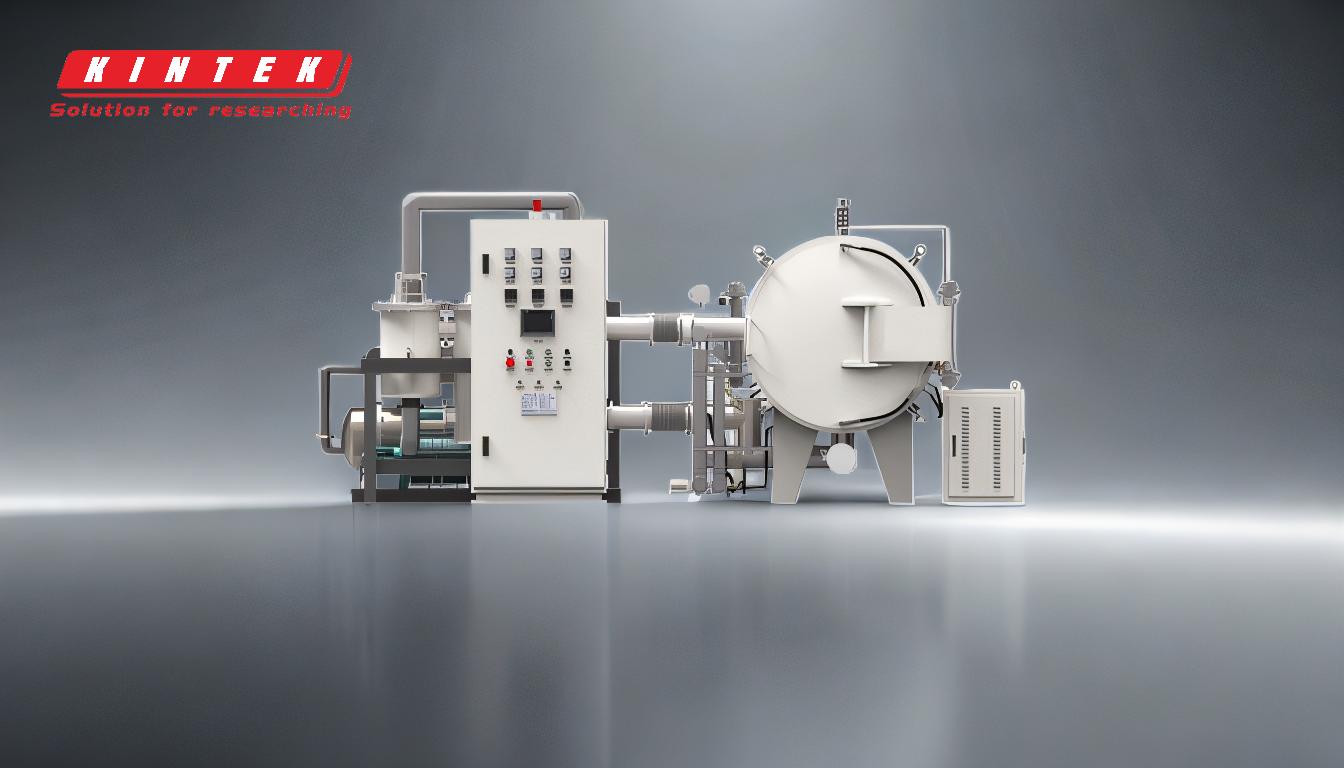
-
Orientation and Energy Efficiency:
- Vertical furnaces, especially upflow models, are designed to maximize energy efficiency by allowing warm air to flow upward naturally, reducing energy consumption.
- Horizontal furnaces, while efficient, do not inherently benefit from the same natural airflow dynamics, potentially leading to higher energy usage in some configurations.
-
Heating Chamber Design:
- Vertical furnaces typically feature a heating chamber where the heating element surrounds the tube, ensuring efficient heat transfer through radiation or convection.
- Horizontal furnaces often have a unique heating chamber design, such as a continuous piece of high-temperature insulation or two semi-cylindrical elements, which may influence their performance in specific applications.
-
Heat Transfer Mechanisms:
- In vertical tube furnaces, heat transfer occurs through both radiation and convection, facilitating uniform temperature distribution along the length of the sample.
- Horizontal tube furnaces rely primarily on radiation for heat transfer, which can result in slight temperature variations along the sample length, requiring careful optimization of temperature profiles.
-
Temperature Uniformity:
- Vertical tube furnaces provide excellent temperature uniformity due to their orientation and surrounding heating elements, ensuring consistent heating and reliable results.
- Horizontal tube furnaces may experience slight temperature variations along the sample length, which can be mitigated through proper design and optimization but may still pose challenges in achieving perfect uniformity.
-
Application Suitability:
- Vertical furnaces are often preferred for processes requiring precise temperature control and minimal particle generation, such as in semiconductor manufacturing or research applications.
- Horizontal furnaces are well-suited for high-performance production environments, where their unique design characteristics can be leveraged for specific industrial processes.
-
Operational Considerations:
- Vertical furnaces are less prone to issues like non-uniform film thicknesses, particle generation, or natural oxide film formation, which are more common in horizontal furnaces.
- Horizontal furnaces may require more frequent maintenance or optimization to address potential temperature variations and ensure consistent performance.
-
Cost and Maintenance:
- While the initial cost of vertical and horizontal furnaces may be similar, vertical furnaces often offer long-term cost savings due to their energy efficiency and reduced maintenance requirements.
- Horizontal furnaces, though potentially more costly to operate in some scenarios, may provide advantages in specific high-performance applications that justify their use.
By understanding these key differences, purchasers can make informed decisions based on their specific needs, whether prioritizing energy efficiency, temperature uniformity, or suitability for high-performance production environments.
Summary Table:
Feature | Vertical Furnaces | Horizontal Furnaces |
---|---|---|
Orientation | Upflow design maximizes energy efficiency | Natural airflow dynamics less effective |
Heating Chamber Design | Heating element surrounds the tube for efficient heat transfer | Unique designs like continuous insulation or semi-cylindrical elements |
Heat Transfer | Radiation and convection for uniform temperature distribution | Primarily radiation, may cause slight temperature variations |
Temperature Uniformity | Excellent uniformity due to surrounding heating elements | Slight variations along sample length, requires optimization |
Applications | Ideal for precise temperature control (e.g., semiconductor manufacturing) | Suited for high-performance production environments |
Operational Considerations | Less prone to particle generation or non-uniform film thicknesses | May require frequent maintenance to address temperature variations |
Cost and Maintenance | Long-term cost savings due to energy efficiency and reduced maintenance | Potentially higher operational costs, justified in specific high-performance uses |
Need help choosing the right furnace for your needs? Contact us today for expert advice!