PVD (Physical Vapor Deposition) and traditional plating (such as electroplating) are both surface coating techniques, but they differ significantly in their processes, properties, and applications. PVD involves depositing thin layers of material onto a surface in a vacuum environment, creating a durable, corrosion-resistant, and environmentally friendly coating. Traditional plating, on the other hand, relies on electrochemical processes to deposit a layer of metal onto a substrate, often requiring a clear coat that can degrade over time. PVD coatings are known for their superior durability, resistance to tarnishing, and environmental safety, making them a preferred choice in industries like aerospace, medical, and marine applications.
Key Points Explained:
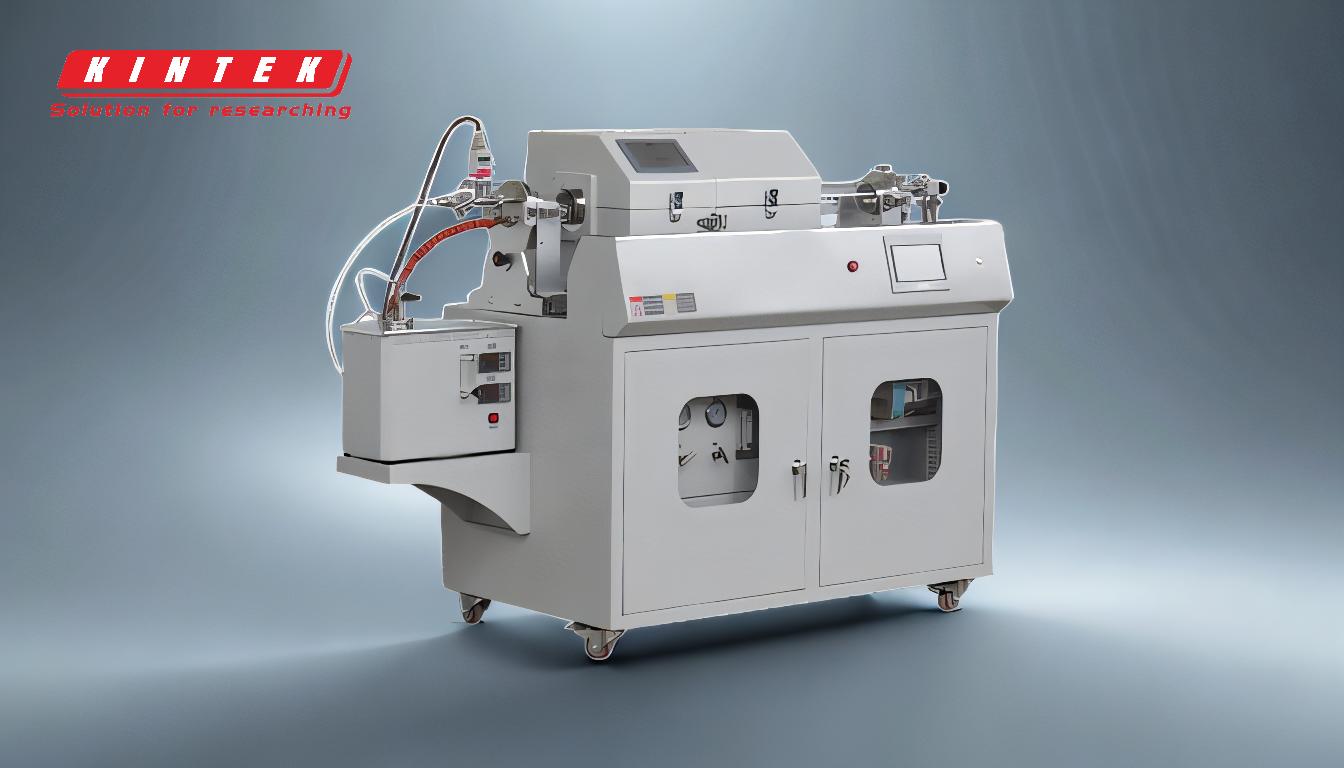
-
Process Differences:
-
PVD:
- Involves vaporizing the coating material in a vacuum chamber and depositing it onto the substrate through condensation.
- Uses low-voltage, high-current arc discharge technology to create a thin, ultra-hard film (3–5μm).
- Operates at lower temperatures (around 500 °C), making it suitable for materials sensitive to high heat.
-
Plating (Electroplating):
- Relies on an electrochemical process where metal ions in a solution are deposited onto the substrate using an electric current.
- Often requires a clear top coat to protect the metal layer, which can degrade over time, leading to tarnishing or corrosion.
-
PVD:
-
Coating Properties:
-
PVD:
- Forms a robust and resilient layer due to atomic-level bonding, ensuring exceptional adhesion and preventing peeling or chipping.
- Offers superior hardness, wear resistance, and resistance to UV light, corrosion, scratching, and saltwater.
- Does not require a clear top coat, making it more durable and long-lasting.
-
Plating:
- Typically produces a thinner and less durable coating compared to PVD.
- Requires a clear coat for protection, which can degrade over time, leading to tarnishing or corrosion.
-
PVD:
-
Environmental Impact:
-
PVD:
- Considered environmentally friendly as it does not release harmful chemicals into the atmosphere.
- Does not generate toxic substances during the coating process.
-
Plating:
- Often involves the use of toxic chemicals and produces hazardous waste, making it less environmentally friendly.
-
PVD:
-
Applications:
-
PVD:
- Widely used in industries requiring high durability and resistance, such as aerospace, medical, and marine applications.
- Suitable for interrupted cutting processes like milling due to its compressive stress properties.
-
Plating:
- Commonly used for decorative purposes, such as jewelry, automotive trim, and household fixtures.
- Less suitable for high-stress or harsh environments due to its lower durability.
-
PVD:
-
Durability and Maintenance:
-
PVD:
- Extremely tough and durable, reducing maintenance costs and increasing product longevity.
- Retains its elegance and attractiveness for many years with proper care.
-
Plating:
- More prone to wear and tear, requiring frequent maintenance or re-plating to maintain appearance and functionality.
-
PVD:
-
Material Options:
-
PVD:
- Uses advanced materials like titanium nitride, which offer excellent hardness and wear resistance.
-
Plating:
- Typically uses traditional metals like brass, nickel, and gold, which may not offer the same level of durability.
-
PVD:
In summary, PVD coatings are superior to traditional plating in terms of durability, environmental safety, and resistance to wear and corrosion. They are ideal for high-performance applications, while traditional plating remains suitable for decorative purposes where extreme durability is not a primary concern.
Summary Table:
Aspect | PVD | Traditional Plating |
---|---|---|
Process | Vaporization in a vacuum chamber; low-temperature, high-current arc discharge. | Electrochemical deposition; requires a clear top coat. |
Coating Properties | Durable, corrosion-resistant, UV-resistant; no clear coat needed. | Thinner, less durable; requires a clear coat that degrades over time. |
Environmental Impact | Environmentally friendly; no toxic chemicals released. | Uses toxic chemicals; produces hazardous waste. |
Applications | Aerospace, medical, marine; high-durability applications. | Decorative purposes like jewelry, automotive trim, and household fixtures. |
Durability | Extremely tough; reduces maintenance costs and increases longevity. | Prone to wear and tear; requires frequent maintenance. |
Material Options | Advanced materials like titanium nitride for superior hardness. | Traditional metals like brass, nickel, and gold. |
Upgrade your coating solutions with PVD technology—contact our experts today!