Resistance heating and induction heating are two distinct methods of generating heat, each with unique mechanisms and applications. Resistance heating relies on the principle of electrical resistance, where heat is produced as electric current passes through a resistive material, such as a coil or wire. This heat is then transferred to the target object via conduction. In contrast, induction heating uses electromagnetic induction to generate heat directly within the target object. An alternating magnetic field induces eddy currents in the object, causing it to heat up due to its internal resistance. This method eliminates the need for direct contact between the heat source and the object, making it more efficient for certain applications. The differences in design, efficiency, and application make each method suitable for specific use cases, such as soldering, where inductive systems integrate the heater and tip into a single piece, while resistive systems separate the heater and tip.
Key Points Explained:
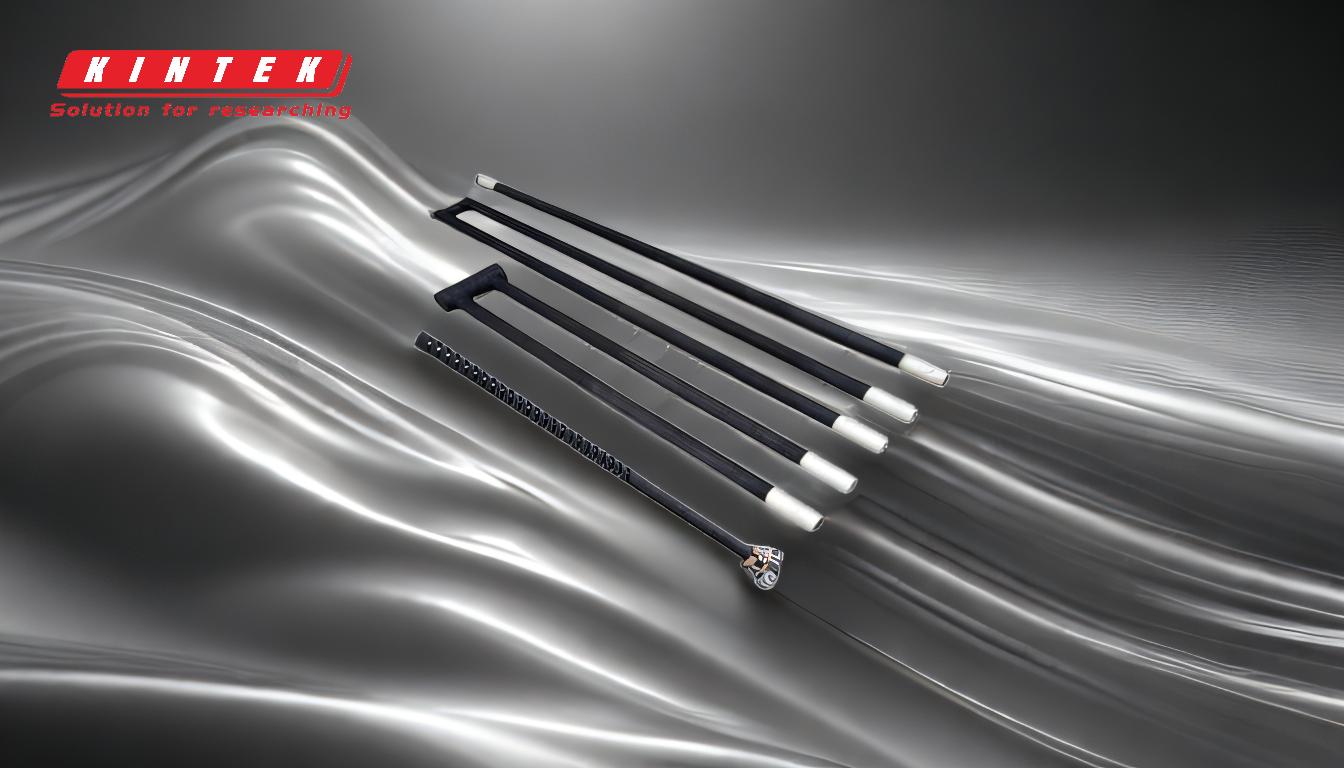
-
Mechanism of Heat Generation:
- Resistance Heating: Heat is generated when electric current flows through a resistive material, such as a coil or wire. The material's resistance to the current causes it to heat up, and this heat is then transferred to the target object via conduction.
- Induction Heating: Heat is generated directly within the target object through electromagnetic induction. An alternating magnetic field induces eddy currents in the object, which produce heat due to the object's internal resistance.
-
Design and Construction:
- Resistance Heating: Typically involves a two-piece design, where the heat is generated in a separate heater coil and then conducted to the tip or target object. This design can lead to heat loss during transfer.
- Induction Heating: Often features a one-piece design, where the heater is integrated into the tip or target object. This design minimizes heat loss and improves efficiency.
-
Efficiency and Heat Transfer:
- Resistance Heating: Less efficient due to heat loss during conduction from the heater to the target object. The efficiency depends on the thermal conductivity of the materials involved.
- Induction Heating: More efficient as heat is generated directly within the target object, reducing heat loss. This method is particularly effective for materials with high electrical conductivity.
-
Applications:
- Resistance Heating: Commonly used in applications where direct contact heating is acceptable, such as soldering irons, space heaters, and industrial furnaces.
- Induction Heating: Preferred for applications requiring precise and localized heating, such as inductive soldering, metal hardening, and cooking appliances like induction cooktops.
-
Advantages and Disadvantages:
-
Resistance Heating:
- Advantages: Simpler design, lower initial cost, and suitability for a wide range of materials.
- Disadvantages: Lower efficiency, slower heating times, and potential for heat loss.
-
Induction Heating:
- Advantages: Higher efficiency, faster heating times, and precise control over heating.
- Disadvantages: Higher initial cost, complexity in design, and limited to materials that can be inductively heated.
-
Resistance Heating:
By understanding these key differences, equipment and consumable purchasers can make informed decisions based on the specific requirements of their applications.
Summary Table:
Aspect | Resistance Heating | Induction Heating |
---|---|---|
Mechanism | Heat generated via electrical resistance in a coil or wire; transferred by conduction. | Heat generated directly in the object via electromagnetic induction and eddy currents. |
Design | Two-piece design (separate heater and target). | One-piece design (heater integrated into the target). |
Efficiency | Less efficient due to heat loss during conduction. | More efficient with minimal heat loss. |
Applications | Soldering irons, space heaters, industrial furnaces. | Inductive soldering, metal hardening, induction cooktops. |
Advantages | Simpler design, lower cost, versatile for many materials. | Higher efficiency, faster heating, precise control. |
Disadvantages | Slower heating, potential heat loss. | Higher cost, complex design, limited to conductive materials. |
Need help choosing the right heating method for your application? Contact our experts today for personalized advice!