Thin film and thick film coatings differ primarily in their thickness, deposition methods, and applications. Thin films are typically less than one micron thick, created by depositing individual atoms or molecules onto a substrate. They are used for enhancing properties like transparency, durability, and electrical conductivity. Thick films, on the other hand, involve the deposition of particles and are generally thicker, often used in applications requiring robust mechanical properties. Both types of coatings are tailored to specific needs, with thin films being ideal for precision and thin-layer applications, while thick films are suited for durability and structural enhancements.
Key Points Explained:
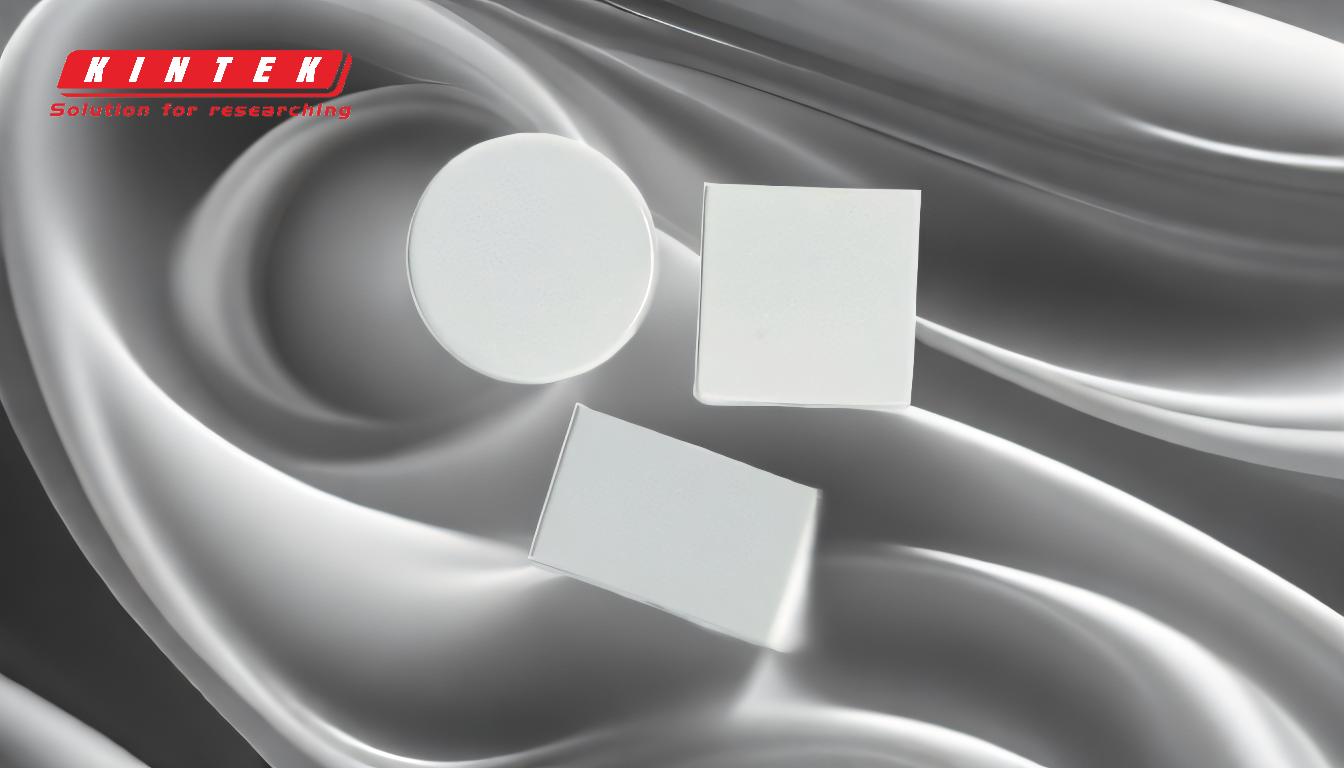
-
Thickness Differences:
- Thin Films: These coatings are extremely thin, ranging from a fraction of a nanometer to one micron in thickness. This thinness allows for precise control over the properties of the coating, making them ideal for applications requiring fine detail and specific characteristics like transparency or electrical conductivity.
- Thick Films: In contrast, thick films are much thicker and involve the deposition of particles rather than individual atoms or molecules. This makes them more suitable for applications where durability and mechanical strength are required.
-
Deposition Methods:
- Thin Film Deposition: This process involves the deposition of individual atoms or molecules onto a substrate. Techniques such as chemical vapor deposition (CVD) and physical vapor deposition (PVD) are commonly used. These methods allow for the creation of very thin, uniform layers with specific properties.
- Thick Film Deposition: This method involves the application of thicker layers, often through processes like screen printing or spraying. The particles used in thick film deposition are larger, resulting in a more robust coating that can withstand harsher conditions.
-
Applications and Characteristics:
- Thin Films: These coatings are used in a variety of applications where precise control over the coating's properties is essential. For example, they are used in optical coatings to enhance transparency, in electronic devices to modify electrical conductivity, and in protective coatings to improve durability and scratch resistance.
- Thick Films: These are typically used in applications requiring enhanced mechanical properties. For instance, they are used in the manufacturing of sensors, resistors, and other electronic components where a thicker, more durable coating is necessary.
-
Material Examples and Properties:
- Thin Films: Prominent materials include Al-Cr-N, Ti-Al-N, Cr-N, and Ti-C-N. These materials are chosen for their ability to enhance surface properties such as hardness, corrosion resistance, wear resistance, and cutting ability. For example, Ti-Al-N increases hardness and reduces the coefficient of friction, while Al-Cr-N improves tool life and thermal resistance.
- Thick Films: While specific materials for thick films are not detailed in the references, they generally include a variety of ceramics and metals that provide enhanced mechanical strength and durability.
-
Functional Benefits:
- Thin Films: The primary benefits of thin films include their ability to modify the surface properties of a substrate with a very thin layer. This can include improvements in optical properties, electrical conductivity, and protective qualities.
- Thick Films: The main advantage of thick films is their robustness and ability to provide structural support and protection. They are often used in environments where the coating must withstand significant mechanical stress or harsh conditions.
By understanding these key differences, purchasers and engineers can make informed decisions about which type of coating is best suited for their specific application needs.
Summary Table:
Aspect | Thin Film Coatings | Thick Film Coatings |
---|---|---|
Thickness | Less than one micron (fraction of a nanometer to one micron) | Thicker, involving particle deposition |
Deposition Methods | Chemical vapor deposition (CVD), physical vapor deposition (PVD) | Screen printing, spraying |
Applications | Optical coatings, electronic devices, protective coatings | Sensors, resistors, structural enhancements |
Material Examples | Al-Cr-N, Ti-Al-N, Cr-N, Ti-C-N | Ceramics, metals (general) |
Functional Benefits | Precision, transparency, electrical conductivity, durability | Durability, mechanical strength, structural support |
Need help choosing the right coating for your application? Contact our experts today!