Vertical and horizontal furnace semiconductors differ primarily in their design, heat transfer mechanisms, and the resulting impact on wafer processing. Vertical furnaces minimize contamination risks by allowing dust to settle only on the top wafer, whereas horizontal furnaces expose all wafers to potential contamination. Additionally, vertical furnaces provide better temperature uniformity across wafers, which is crucial for consistent oxide growth and other semiconductor processes. Horizontal furnaces, while also effective, may experience slight temperature variations due to their heat transfer mechanisms. These differences make vertical furnaces more suitable for high-precision semiconductor manufacturing.
Key Points Explained:
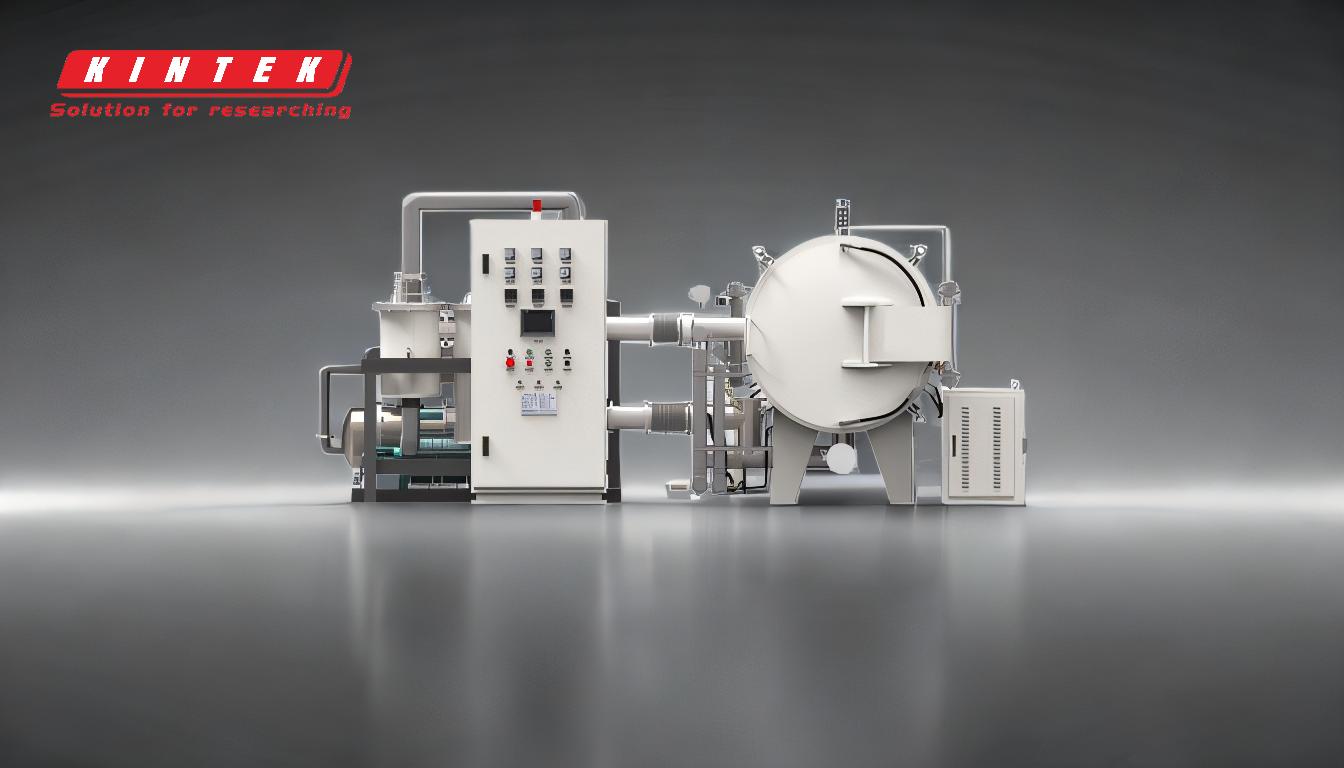
-
Contamination Control:
- Vertical Furnaces: In vertical furnaces, wafers are stacked vertically, so any falling dust or particles will only affect the top wafer in the stack. This design significantly reduces contamination risks for the rest of the wafers, ensuring higher yield and quality.
- Horizontal Furnaces: In horizontal furnaces, wafers are placed horizontally, making all wafers equally susceptible to contamination from falling particles. This can lead to higher defect rates and reduced process reliability.
-
Temperature Uniformity:
- Vertical Furnaces: The heating element in vertical furnaces surrounds the tube, allowing heat to be transferred efficiently through radiation or convection. This design ensures a more uniform temperature distribution along the length of the wafers, which is critical for processes like oxide growth.
- Horizontal Furnaces: While horizontal furnaces also have heating elements surrounding the tube, heat transfer primarily occurs through radiation. This can result in slight temperature variations along the length of the wafers, potentially affecting process uniformity.
-
Heat Transfer Mechanisms:
- Vertical Furnaces: The vertical orientation facilitates better heat distribution through both radiation and convection. Convection currents help maintain a consistent temperature profile, which is essential for uniform processing.
- Horizontal Furnaces: In horizontal furnaces, the lack of convection currents means that heat transfer relies more heavily on radiation. This can lead to localized hot or cold spots, which may impact the consistency of semiconductor processes.
-
Process Uniformity:
- Vertical Furnaces: The combination of reduced contamination and better temperature uniformity makes vertical furnaces ideal for high-precision semiconductor manufacturing. They are particularly effective for processes requiring consistent oxide growth and other critical steps.
- Horizontal Furnaces: While still effective for many applications, horizontal furnaces may require additional measures to compensate for temperature variations and contamination risks, making them less suitable for high-precision processes.
-
Application Suitability:
- Vertical Furnaces: Due to their superior contamination control and temperature uniformity, vertical furnaces are often preferred for advanced semiconductor manufacturing, where even minor defects can significantly impact performance.
- Horizontal Furnaces: Horizontal furnaces are still widely used, especially in less critical applications or where cost considerations are paramount. They are also easier to integrate into existing production lines due to their more traditional design.
In summary, the choice between vertical and horizontal furnace semiconductors depends on the specific requirements of the manufacturing process. Vertical furnaces offer significant advantages in terms of contamination control and temperature uniformity, making them the preferred choice for high-precision applications. Horizontal furnaces, while more susceptible to contamination and temperature variations, remain a viable option for less critical processes or cost-sensitive operations.
Summary Table:
Aspect | Vertical Furnaces | Horizontal Furnaces |
---|---|---|
Contamination Control | Dust settles only on the top wafer, reducing contamination risks. | All wafers are exposed to contamination, increasing defect rates. |
Temperature Uniformity | Superior uniformity due to efficient heat transfer via radiation and convection. | Slight variations due to reliance on radiation, leading to potential hot/cold spots. |
Heat Transfer | Better heat distribution through convection and radiation. | Heat transfer relies more on radiation, limiting uniformity. |
Process Uniformity | Ideal for high-precision processes like oxide growth. | Requires additional measures for high-precision applications. |
Application Suitability | Preferred for advanced semiconductor manufacturing. | Suitable for less critical or cost-sensitive operations. |
Need help choosing the right furnace for your semiconductor manufacturing? Contact our experts today!