Hardening is a critical process in metallurgy that significantly enhances the mechanical properties of metals, particularly steel. By altering the microstructure of the material through heat treatment and rapid cooling, hardening increases hardness, strength, and wear resistance. However, it often comes at the expense of reduced ductility and toughness, making the material more brittle. The process involves heating the metal to a specific temperature, holding it to allow for uniform heat distribution, and then quenching it in a cooling medium like oil or water. This rapid cooling transforms the microstructure, leading to improved mechanical properties. Understanding the effects of hardening is essential for engineers and material scientists to optimize material performance for specific applications, balancing strength with other critical properties.
Key Points Explained:
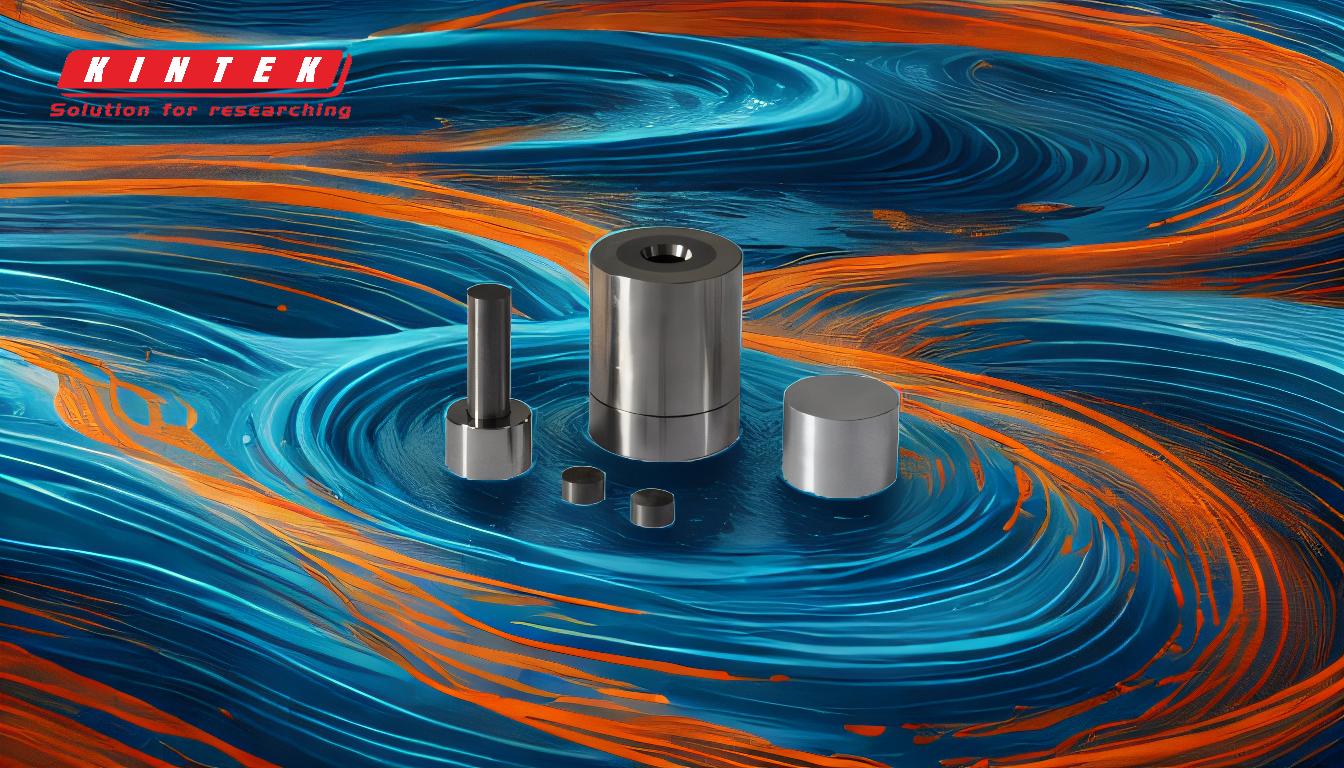
-
Increased Hardness and Strength:
- Hardening significantly increases the hardness and tensile strength of metals. This is achieved by transforming the microstructure, particularly in steels, from a softer phase like pearlite to a harder phase like martensite. The rapid cooling (quenching) locks the carbon atoms in place, creating a more rigid and dense atomic structure.
- This makes the material more resistant to deformation and wear, which is crucial for applications like cutting tools, gears, and structural components subjected to high stress.
-
Reduced Ductility and Toughness:
- While hardening improves hardness and strength, it often reduces ductility and toughness. Ductility refers to the ability of a material to deform plastically before fracturing, while toughness is the ability to absorb energy and resist fracture.
- The formation of martensite, which is very hard but brittle, can make the material prone to cracking under impact or sudden loads. This trade-off must be carefully managed, especially in applications where both strength and toughness are required.
-
Microstructural Changes:
- The hardening process involves heating the metal to a temperature where it becomes austenitic (a high-temperature phase of steel), followed by rapid cooling. This transforms the microstructure from austenite to martensite, a hard and brittle phase.
- The cooling rate and the medium used (e.g., water, oil, or air) play a crucial role in determining the final microstructure and, consequently, the mechanical properties.
-
Importance of Tempering:
- To mitigate the brittleness caused by hardening, a subsequent tempering process is often employed. Tempering involves reheating the hardened material to a temperature below its critical point and then cooling it slowly.
- This process reduces internal stresses, improves toughness, and restores some ductility while retaining a significant portion of the hardness gained during hardening.
-
Application-Specific Considerations:
- The effects of hardening must be tailored to the specific application. For example, in tools and dies, high hardness and wear resistance are prioritized, even if it means sacrificing some toughness.
- In contrast, structural components like beams or shafts may require a balance of strength and toughness to withstand dynamic loads and impacts.
-
Material Selection and Process Control:
- The effectiveness of hardening depends on the composition of the material. Alloying elements like carbon, chromium, and nickel can enhance hardenability, allowing for deeper and more uniform hardening.
- Precise control of heating and cooling rates is essential to achieve the desired mechanical properties and avoid defects like cracking or warping.
By understanding these key points, engineers and material scientists can optimize the hardening process to achieve the desired balance of mechanical properties for specific applications.
Summary Table:
Effect | Description |
---|---|
Increased Hardness | Transforms microstructure to martensite, enhancing resistance to deformation. |
Improved Strength | Rapid cooling locks carbon atoms, increasing tensile strength. |
Reduced Ductility | Martensite formation makes the material more brittle, reducing plastic deformation. |
Microstructural Changes | Heating and quenching alter the microstructure, impacting mechanical properties. |
Tempering Importance | Reheating reduces brittleness, restoring toughness while retaining hardness. |
Application-Specific | Tailor hardening for tools (high hardness) or structural components (balanced toughness). |
Optimize your material performance with expert hardening solutions—contact us today!