An electric arc furnace (EAF) is a type of furnace that uses electricity to generate extremely high temperatures for melting and refining metals. It operates by creating an electric arc between electrodes and the metal charge, which produces the heat necessary for melting. EAFs are widely used in steelmaking and other metallurgical processes due to their efficiency, flexibility, and ability to recycle scrap metal. The furnace consists of key components such as electrodes, a hearth, a roof, and a side wall, all designed to withstand high temperatures and facilitate the melting process. EAFs are distinct from other heating systems as they rely solely on electricity, making them environmentally friendly and cost-effective for industrial applications.
Key Points Explained:
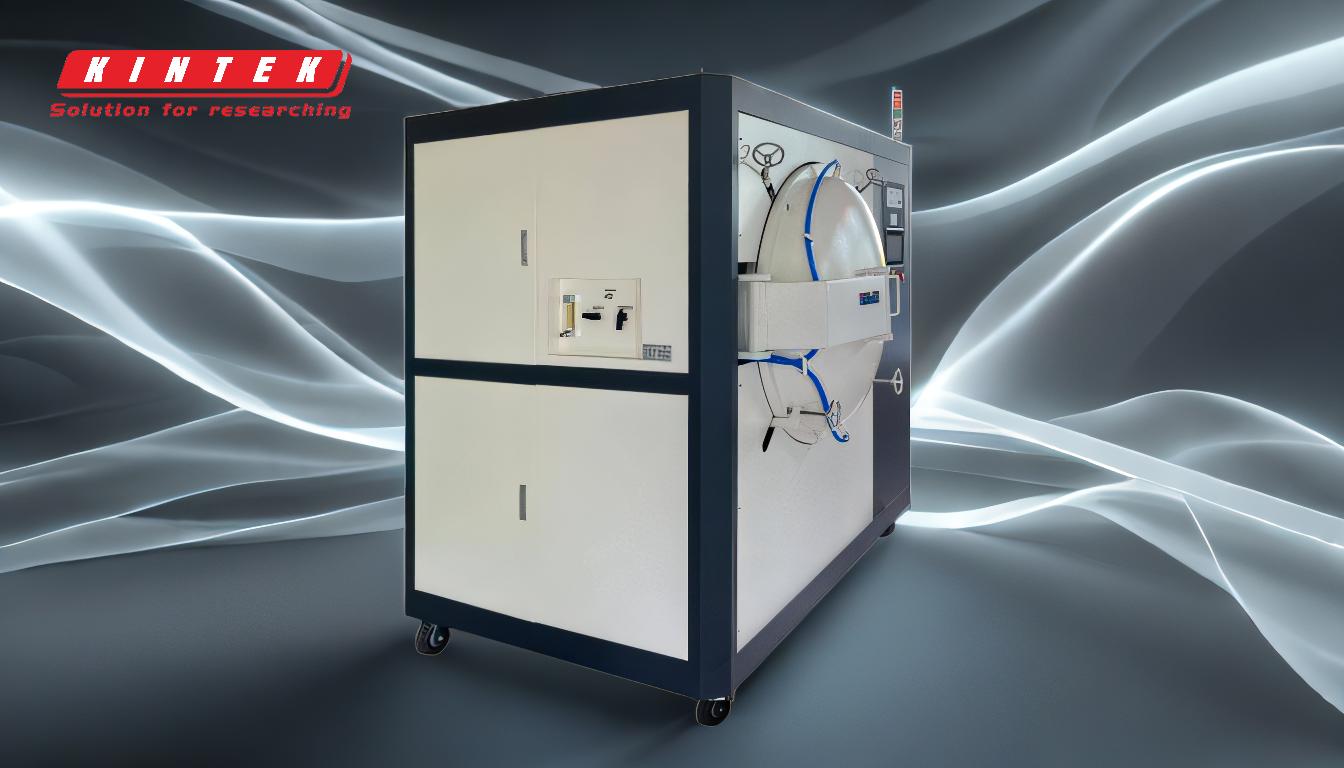
-
Definition and Purpose of an Electric Arc Furnace:
- An electric arc furnace is a heating chamber that uses electricity to generate high temperatures for melting metals and refractories. Unlike traditional furnaces, it does not rely on fossil fuels, making it a cleaner and more sustainable option for industrial processes.
- The primary purpose of an EAF is to melt and refine metals, particularly in steelmaking. It is also used for alloying and recycling scrap metal, contributing to resource efficiency.
-
Key Components of an Electric Arc Furnace:
- Electrodes: Typically made of graphite or carbon, electrodes are responsible for creating the electric arc. They are inserted through holes in the furnace roof and positioned close to the metal charge.
- Hearth: The hearth is the bottom part of the furnace where molten metal collects. It is designed to withstand high temperatures and is often lined with refractory materials.
- Roof: The roof of the furnace has holes for the electrodes and is removable to allow for loading the charge. It is also lined with refractory materials to protect against heat.
- Side Walls: These walls are constructed to contain the molten metal and withstand the intense heat generated during operation.
-
Working Principle of an Electric Arc Furnace:
- The furnace operates by creating an electric arc between the electrodes and the metal charge. This arc generates temperatures high enough to melt the metal. The process begins with the electrodes creating a short circuit, which triggers the arc. Once established, the arc maintains a stable discharge, providing continuous heat.
- The electricity used in the furnace is typically converted from high voltage to low voltage and high current, ensuring efficient heat generation.
-
Advantages of Electric Arc Furnaces:
- Energy Efficiency: EAFs are highly efficient as they convert electrical energy directly into heat with minimal losses.
- Environmental Benefits: Since EAFs use electricity instead of fossil fuels, they produce fewer emissions and are more environmentally friendly.
- Flexibility: EAFs can process a wide range of metal charges, including scrap metal, making them versatile for various industrial applications.
-
Applications of Electric Arc Furnaces:
- Steelmaking: EAFs are extensively used in the steel industry for melting and refining steel. They are particularly useful for recycling scrap steel, reducing the need for raw materials.
- Alloy Production: EAFs are employed in the production of various alloys by melting and mixing different metals.
- Refractory Melting: The high temperatures achieved in EAFs make them suitable for melting refractory materials used in industrial processes.
-
Comparison with Other Furnace Types:
- Unlike gas or oil-fired furnaces, EAFs rely entirely on electricity, eliminating the need for fossil fuels and reducing operational costs.
- EAFs are more adaptable to smaller-scale operations and can be started and stopped more easily than traditional blast furnaces.
In summary, an electric arc furnace is a critical piece of equipment in modern metallurgy, offering a sustainable and efficient solution for melting and refining metals. Its reliance on electricity, combined with its ability to recycle materials, makes it an essential tool in industries focused on sustainability and cost-effectiveness.
Summary Table:
Aspect | Details |
---|---|
Definition | A furnace using electricity to generate high temperatures for melting metals. |
Key Components | Electrodes, hearth, roof, and side walls. |
Working Principle | Electric arc between electrodes and metal charge generates heat for melting. |
Advantages | Energy-efficient, eco-friendly, and versatile for various metal charges. |
Applications | Steelmaking, alloy production, and refractory melting. |
Learn more about how electric arc furnaces can optimize your industrial processes—contact our experts today!