A hydraulic forging press is a powerful machine used in metalworking to shape and form metal parts through the application of high pressure. It operates using hydraulic fluid to generate force, which is then applied to the workpiece. The primary function of a hydraulic forging press is to deform metal into desired shapes by compressing it between two dies. This process is essential in industries such as automotive, aerospace, and manufacturing, where precision and strength are critical. The machine's ability to apply consistent and controlled pressure ensures high-quality results, making it indispensable for producing complex and durable metal components.
Key Points Explained:
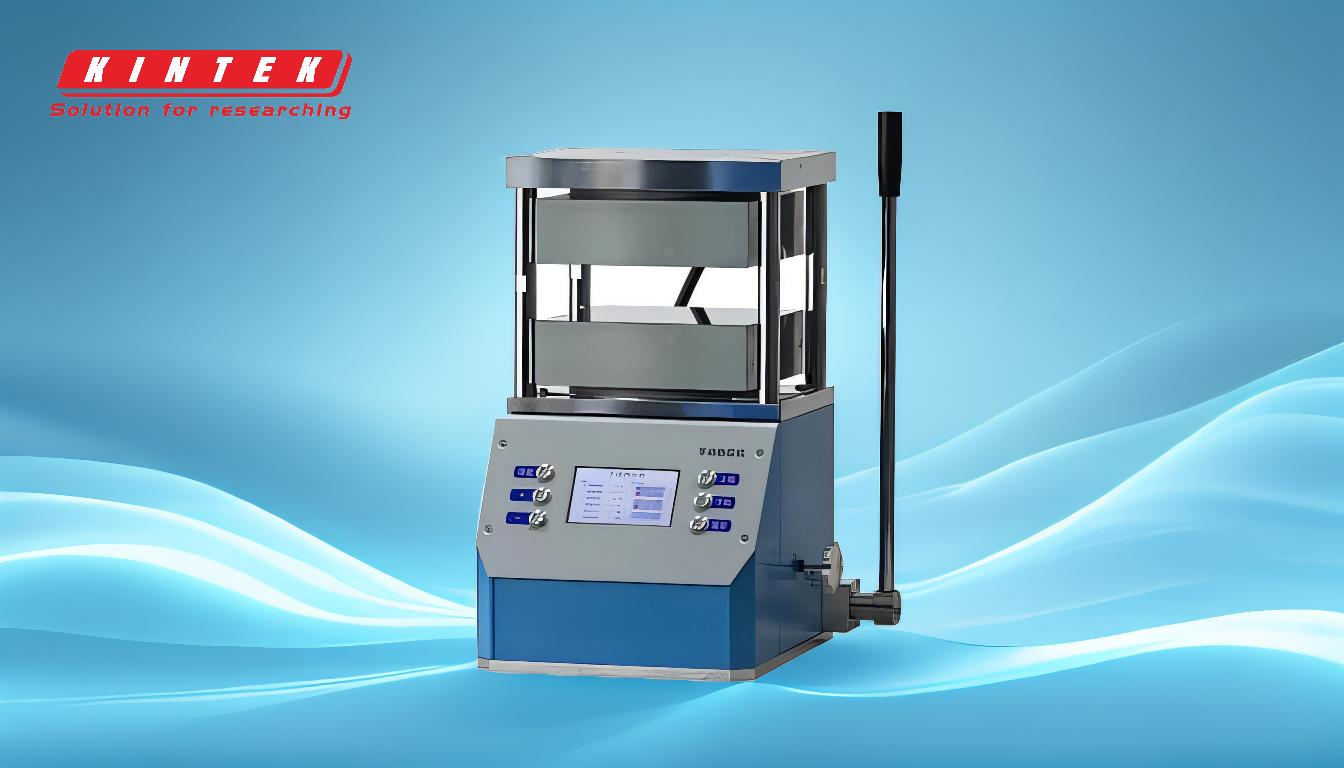
-
Primary Function of Hydraulic Forging Press:
- The hydraulic forging press is designed to shape metal by applying high pressure. This is achieved through the use of hydraulic fluid, which generates the necessary force to compress the metal between two dies. The process is known as forging, and it is used to create parts that are strong, durable, and precise.
-
Key Components of a Hydraulic Forging Press:
- Safety Door: Ensures operator safety by preventing access to the press during operation.
- Limit Switch: Controls the movement of the press to prevent over-travel and ensure precise operation.
- Manual Control Valve: Allows for manual control of the hydraulic system, providing flexibility in operation.
- Relief Valve: Protects the system from overpressure by releasing excess hydraulic fluid.
- Pressure Gauge: Monitors the pressure within the hydraulic system to ensure it operates within safe limits.
- Hydraulic Cylinder: The core component that generates the force needed for forging.
- Oil Tank: Stores the hydraulic fluid required for the system's operation.
- Pressing Plate: The surface that applies pressure to the workpiece, shaping it according to the die's design.
-
Advantages of Using a Hydraulic Forging Press:
- Consistent Pressure: The hydraulic system ensures that the pressure applied to the workpiece is consistent, leading to uniform deformation and high-quality results.
- Precision: The ability to control the pressure and movement of the press allows for precise shaping of complex parts.
- Versatility: Hydraulic forging presses can be used for a wide range of materials and part sizes, making them versatile tools in metalworking.
- Efficiency: The machine's design allows for efficient operation, reducing the time and energy required to produce forged parts.
-
Comparison with Mechanical Forging Press:
- While both hydraulic and mechanical forging presses are used for shaping metal, they differ in their operation. A mechanical forging press uses a motor-driven mechanism to generate force, whereas a hydraulic forging press relies on hydraulic fluid. The hydraulic press offers more control over the forging process, allowing for precise adjustments in pressure and speed. This makes it more suitable for applications requiring high precision and consistency.
-
Applications of Hydraulic Forging Press:
- Automotive Industry: Used to produce critical components such as engine parts, transmission components, and suspension parts.
- Aerospace Industry: Essential for manufacturing high-strength, lightweight components used in aircraft and spacecraft.
- Manufacturing: Widely used in the production of tools, machinery, and other metal products that require high durability and precision.
-
Role of Hydraulic Hot Press Machine in Forging:
- The hydraulic hot press machine plays a crucial role in the forging process, especially when working with materials that require heating. The machine's fast heating capabilities ensure that workpieces, particularly those under twenty millimeters thick, are heated uniformly and efficiently. This uniform heating enhances the quality of the forged parts by ensuring that the adhesive curing strength is maintained throughout the workpiece. The design of the hydraulic hot press machine minimizes the influence of workpiece thickness on heating, making it an essential tool for producing high-quality forged components.
In summary, the hydraulic forging press is a vital machine in the metalworking industry, offering precise control, consistent pressure, and versatility in shaping metal parts. Its key components work together to ensure safe and efficient operation, making it indispensable for producing high-quality forged components in various industries. The integration of a hydraulic hot press machine further enhances its capabilities, especially in applications requiring uniform heating and precise temperature control.
Summary Table:
Aspect | Details |
---|---|
Primary Function | Shapes metal by applying high pressure through hydraulic fluid. |
Key Components | Safety door, limit switch, manual control valve, relief valve, pressure gauge, hydraulic cylinder, oil tank, pressing plate. |
Advantages | Consistent pressure, precision, versatility, efficiency. |
Applications | Automotive, aerospace, manufacturing. |
Comparison with Mechanical | Offers better control over pressure and speed for high-precision forging. |
Ready to enhance your metalworking process? Contact us today to learn more about hydraulic forging presses!