Spark plasma sintering (SPS) has its roots in the 1960s when a spark sintering method was first investigated and patented for compacting metal powders. However, this early method faced significant challenges, including high equipment costs and low sintering efficiency, which limited its widespread adoption. The concept was revitalized and refined from the mid-1980s to the early 1990s with the development of Plasma Activated Sintering (PAS) and Spark Plasma Sintering (SPS). These advancements introduced the use of pulsed direct current to enhance densification, marking a significant improvement over earlier methods and paving the way for modern SPS techniques.
Key Points Explained:
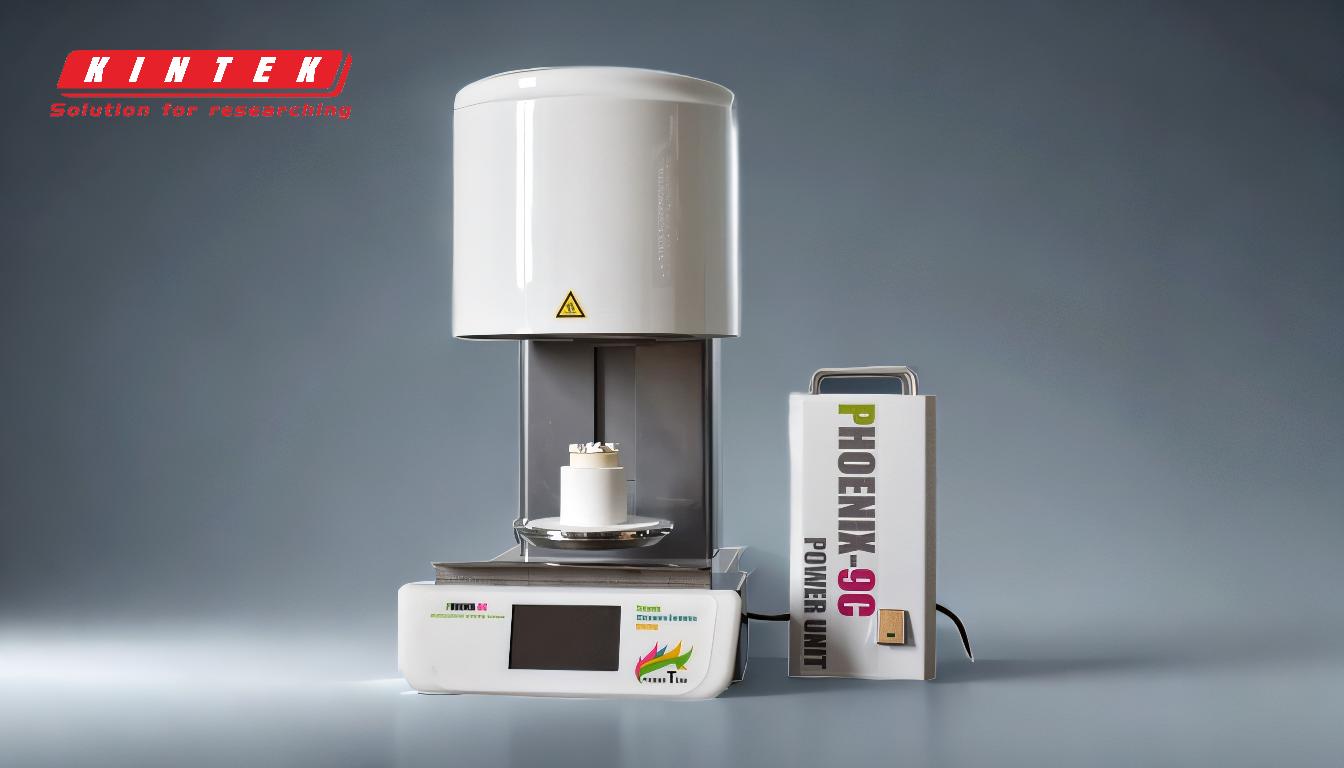
-
Origins in the 1960s:
- The concept of spark sintering was first explored and patented in the 1960s.
- This early method was primarily used for compacting metal powders.
- Despite its innovative approach, it was not widely adopted due to high equipment costs and low sintering efficiency.
-
Challenges of Early Methods:
- High equipment costs made the technology inaccessible to many potential users.
- Low sintering efficiency meant that the process was not as effective as desired, limiting its practical applications.
-
Revival and Development in the 1980s and 1990s:
- From the mid-1980s to the early 1990s, the concept of spark sintering was revisited and significantly improved.
- This period saw the introduction of Plasma Activated Sintering (PAS) and Spark Plasma Sintering (SPS).
- These new methods utilized pulsed direct current to enhance densification, addressing some of the inefficiencies of the earlier spark sintering techniques.
-
Introduction of Pulsed Direct Current:
- The use of pulsed direct current in PAS and SPS was a key innovation.
- This technology allowed for better control over the sintering process, leading to improved densification and material properties.
- The pulsed current helps in generating localized high temperatures, which facilitates faster and more efficient sintering.
-
Modern SPS Techniques:
- Today, SPS is recognized for its ability to produce high-density materials with fine microstructures.
- It is widely used in various fields, including materials science, ceramics, and metallurgy.
- The method is valued for its ability to sinter materials at lower temperatures and in shorter times compared to conventional sintering methods.
-
Impact and Applications:
- The development of SPS has had a significant impact on the field of materials science.
- It has enabled the production of advanced materials with unique properties, such as nanocrystalline materials and composites.
- The technique is also used for the synthesis of functionally graded materials and the consolidation of difficult-to-sinter powders.
By understanding the history and evolution of spark plasma sintering, we can appreciate the technological advancements that have made SPS a valuable tool in modern materials science. The journey from the initial spark sintering method to the sophisticated SPS techniques of today highlights the importance of continuous innovation and improvement in scientific research and industrial applications.
Summary Table:
Key Milestones | Details |
---|---|
1960s Origins | Spark sintering method patented for compacting metal powders. |
Challenges | High equipment costs and low sintering efficiency limited adoption. |
1980s-1990s Revival | Introduction of PAS and SPS with pulsed direct current for better densification. |
Modern SPS Techniques | High-density materials with fine microstructures; used in ceramics, metallurgy. |
Applications | Advanced materials, nanocrystalline composites, functionally graded materials. |
Discover how spark plasma sintering can revolutionize your materials research—contact us today to learn more!