The hot press technique is a manufacturing process that combines heat and pressure to create dense, high-quality materials. It involves placing a powder compact in a die and simultaneously applying temperature and pressure, often using induction heating and hydraulic systems. This method is particularly effective for sintering high-temperature materials, as it enhances densification, reduces sintering time, and lowers the required temperature and pressure compared to traditional methods. Hot pressing is widely used in industries requiring strong, precise, and uniform materials, such as electronics, aerospace, and advanced ceramics. The process offers numerous advantages, including rapid heating, precise temperature control, and the ability to form permanent electromechanical connections.
Key Points Explained:
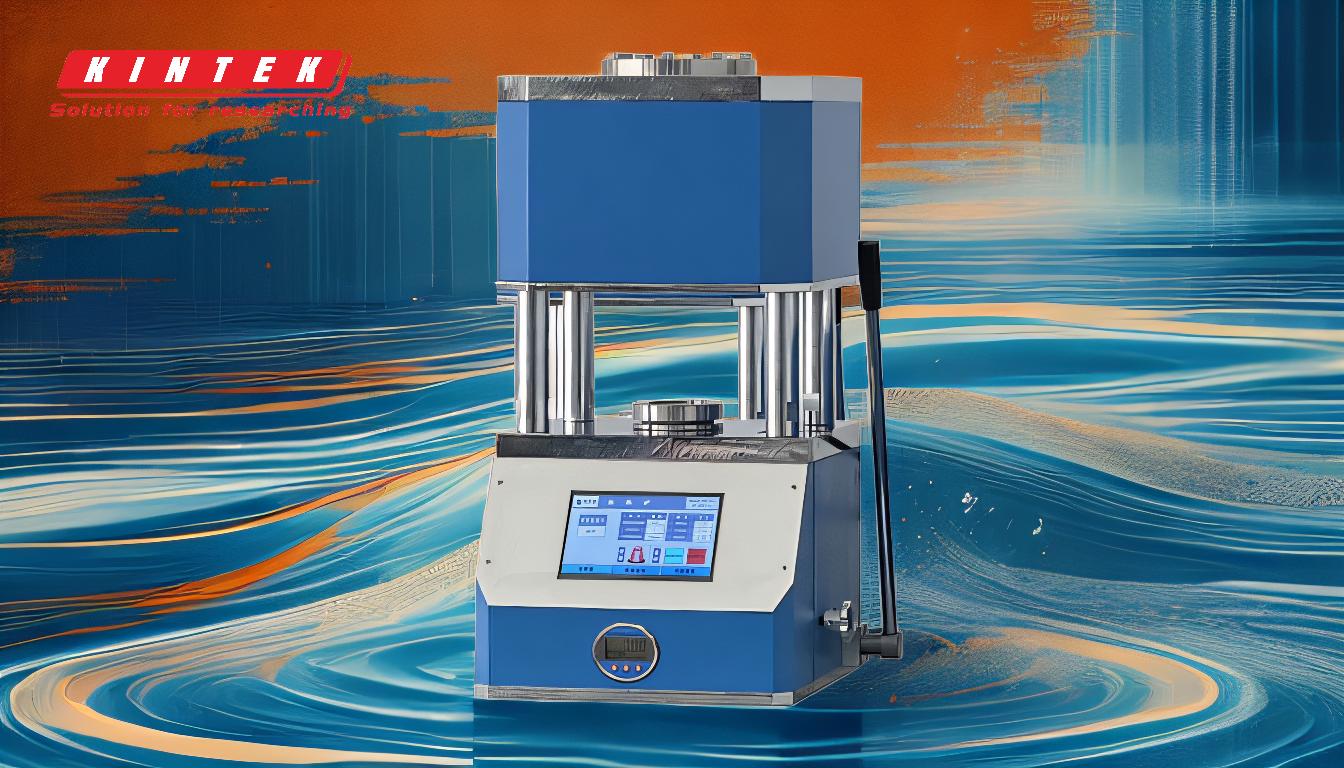
-
Definition and Process of Hot Pressing:
- Hot pressing involves applying both heat and pressure simultaneously to a powder compact contained within a die.
- Heating is typically achieved using induction coils and a graphite die, while pressure is applied hydraulically.
- This process is often conducted in a vacuum or under an inert gas atmosphere to prevent oxidation and contamination.
-
Benefits of Hot Pressing:
- Increased Densification: The applied pressure aids in achieving densities close to the theoretical maximum, resulting in stronger and more uniform materials.
- Reduced Sintering Time and Temperature: Hot pressing significantly shortens the sintering period and lowers the required temperature and pressure compared to conventional sintering methods.
- Improved Material Properties: The process effectively restrains grain growth, leading to finer microstructures and enhanced material performance.
-
Working Principle of a Hot Press Machine:
- A hot press machine operates by applying positive pressure based on negative pressure with special glue.
- It functions under high pressure, low temperature, and short film pressure time conditions, which help minimize workpiece deformation and ensure high product quality.
- The machine can automate tasks such as table feeding, heating, vacuuming, forming, and demolding, driven by oil pressure and compressed air.
-
Applications of Hot Pressing:
- Electronics: Used to form permanent electromechanical connections by heating and melting solder between components.
- Aerospace and Advanced Ceramics: Ideal for producing high-strength, high-density materials required in these industries.
- Large-Diameter Materials: The technique is capable of preparing large-diameter materials with uniform properties.
-
Advantages of Hot Press Machines:
- Precise Temperature Control: Ensures consistent and accurate heating, crucial for material quality.
- Rapid Heating: High heating rates reduce processing time and energy consumption.
- Even Pressure Distribution: Uniform pressure application leads to consistent material properties.
- Programmability: Machines can be programmed for various applications, offering flexibility and efficiency.
-
Technological Advancements:
- Vacuum Hot Pressing: This method further enhances the process by shortening the sintering period, reducing the sintering temperature, and improving material density.
- IT Integration: Modern hot press machines utilize IT technology for real-time monitoring and control, ensuring precise densification and material quality.
-
Economic and Environmental Benefits:
- Smaller Equipment Investment: Hot pressing requires less capital investment compared to other high-temperature processing methods.
- Energy Efficiency: The process consumes less energy due to reduced sintering times and lower temperatures.
- Material Efficiency: The ability to use thinner pressure-bearing materials reduces waste and material costs.
In summary, the hot press technique is a versatile and efficient method for producing high-quality materials with enhanced properties. Its ability to combine heat and pressure in a controlled environment makes it indispensable in various high-tech industries. The continuous advancements in hot press technology, including vacuum hot pressing and IT integration, further enhance its capabilities, making it a preferred choice for modern manufacturing processes.
Summary Table:
Key Aspect | Details |
---|---|
Process | Simultaneous heat and pressure application to powder compacts in a die. |
Heating Method | Induction coils and graphite die, often in vacuum or inert gas atmosphere. |
Pressure Application | Hydraulic systems for uniform pressure distribution. |
Benefits | Increased densification, reduced sintering time, improved material properties. |
Applications | Electronics, aerospace, advanced ceramics, large-diameter materials. |
Advantages of Machines | Precise temperature control, rapid heating, programmability, even pressure. |
Technological Advancements | Vacuum hot pressing, IT integration for real-time monitoring. |
Economic Benefits | Smaller equipment investment, energy efficiency, material efficiency. |
Ready to enhance your material production process? Contact us today to learn more about hot press solutions!