The melting process is a critical phase in various industries, including metallurgy, glass manufacturing, and plastics production. It involves transforming a solid material into a liquid state by applying heat, which is essential for shaping, purifying, or combining materials. The importance of the melting process lies in its ability to enable the creation of new products, improve material properties, and facilitate recycling. It also plays a key role in ensuring the quality and consistency of the final product, as the melting conditions directly influence the material's structure and performance. Understanding and controlling the melting process is vital for achieving desired outcomes in manufacturing and material science.
Key Points Explained:
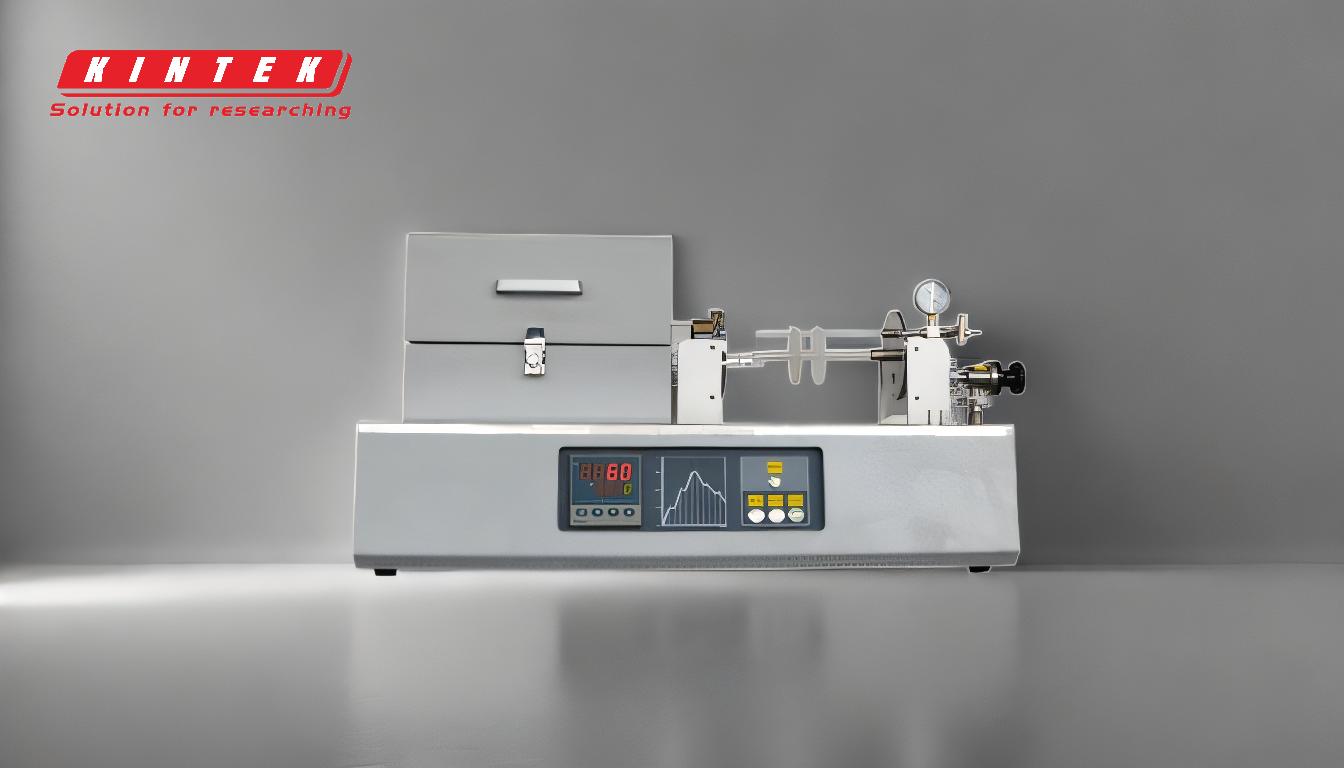
-
Material Transformation and Shaping:
- The melting process allows solid materials to be transformed into a liquid state, making them malleable and easier to shape. This is crucial in industries like metallurgy, where molten metals are cast into molds to create complex shapes and components.
- In glass manufacturing, melting raw materials like silica sand enables the production of glass products with specific properties, such as transparency and strength.
- For plastics, melting is essential for injection molding, extrusion, and other forming processes that produce a wide range of products.
-
Purification and Refinement:
- Melting is often used to purify materials by removing impurities. For example, in metal refining, the melting process separates unwanted elements from the desired metal, resulting in higher purity and better performance.
- In recycling, melting allows materials like metals and plastics to be reprocessed and reused, reducing waste and conserving resources.
-
Material Properties and Performance:
- The conditions under which a material is melted, such as temperature and cooling rate, significantly influence its final properties. For instance, controlled melting and cooling can enhance the strength, durability, and thermal resistance of metals and alloys.
- In glass production, precise control of the melting process ensures the desired optical, thermal, and mechanical properties of the final product.
-
Consistency and Quality Control:
- A well-regulated melting process ensures consistency in the final product, which is critical for meeting industry standards and customer expectations. Variations in melting conditions can lead to defects, such as cracks, voids, or uneven material distribution.
- Advanced monitoring and control systems are often employed to maintain optimal melting conditions, ensuring high-quality outputs.
-
Energy Efficiency and Sustainability:
- The melting process is energy-intensive, making energy efficiency a key consideration. Innovations in melting technologies, such as electric arc furnaces and induction heating, aim to reduce energy consumption and environmental impact.
- Sustainable practices, such as using recycled materials and optimizing melting processes, contribute to reducing the carbon footprint of manufacturing industries.
By understanding the importance of the melting process, industries can optimize their operations, improve product quality, and contribute to sustainable manufacturing practices.
Summary Table:
Key Aspect | Importance |
---|---|
Material Transformation | Enables shaping of materials for complex designs in metallurgy, glass, plastics. |
Purification | Removes impurities, improving material purity and performance. |
Material Properties | Influences strength, durability, and thermal resistance through controlled melting. |
Quality Control | Ensures consistency and reduces defects in final products. |
Sustainability | Promotes recycling and energy-efficient practices, reducing environmental impact. |
Optimize your melting process for better results—contact our experts today!