The Spark Plasma Sintering (SPS) process is a advanced sintering technique that combines the application of pressure and pulsed electric current to achieve rapid densification of materials. This process is characterized by its ability to produce materials with unique microstructures and properties at lower temperatures and shorter processing times compared to conventional sintering methods. The SPS process operates in a vacuum or controlled atmosphere to prevent oxidation and ensure material purity. It involves four main stages: removing gas and creating a vacuum, applying pressure, resistive heating, and cooling. The key mechanism involves the generation of localized high temperatures through spark discharges, which cause evaporation and melting on the surface of powder particles, forming necks around the contact areas between particles. This results in high thermal efficiency and rapid densification.
Key Points Explained:
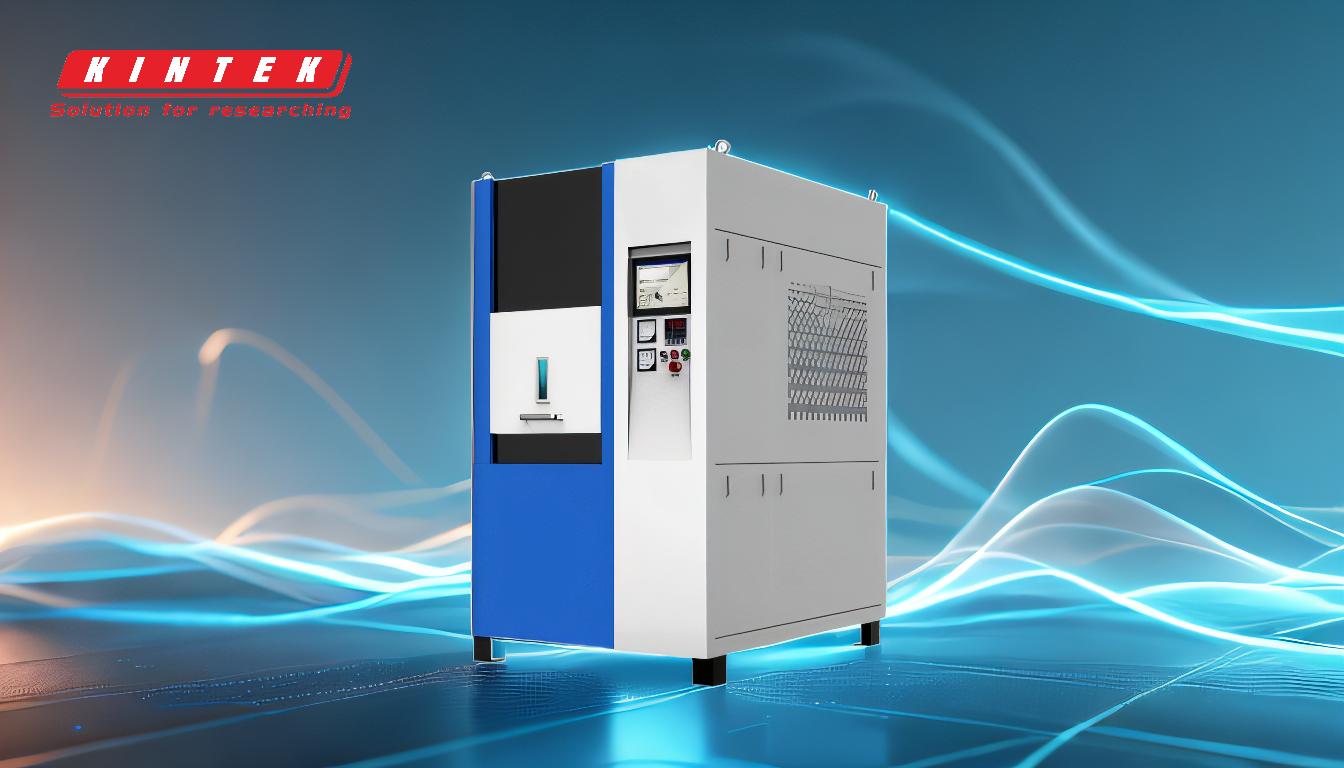
-
Basic Setup and Mechanism:
- The SPS process is based on a modified hot pressing setup where an electric current flows directly through the pressing die (usually graphite) and the component.
- This setup allows for very fast heating times and short process cycles through the use of pulsed currents and the 'spark plasma effect.'
- The spark plasma effect inhibits particle growth and allows the creation of materials with unique compositions and properties.
-
Stages of the SPS Process:
- Removing Gas and Creating a Vacuum: This stage ensures that the environment is free from contaminants and oxidation, which is crucial for maintaining material purity.
- Applying Pressure: Pressure is applied to the powder compact to facilitate densification.
- Resistive Heating: The powder compact is heated directly by pulse arc discharges, achieving very high thermal efficiency and rapid heating.
- Cooling: After the sintering process, the material is cooled down to solidify the microstructure.
-
Spark Discharge and Localized Heating:
- During the SPS process, spark discharges generate localized high temperatures on the surface of powder particles.
- This localized heating causes evaporation and melting, forming necks around the contact areas between particles.
- The formation of these necks is crucial for the densification process, as it enhances the bonding between particles.
-
Advantages of SPS:
- High Heating Rates: The SPS process can achieve very high heating rates, which significantly reduces the overall processing time.
- Low Sintering Temperatures: Materials can be sintered at temperatures 200–500°C lower than those used in conventional sintering methods.
- Precise Control: The process allows for precise control of temperature, pressure, and heating rate, enabling the fabrication of materials with unique microstructures and properties.
-
Applications and Material Properties:
- The SPS process is used to fabricate a wide range of materials, including ceramics, metals, and composites.
- The unique microstructures and properties achieved through SPS make it suitable for applications in aerospace, automotive, and biomedical industries.
- The ability to produce materials with fine grain sizes and enhanced mechanical properties is a significant advantage of the SPS process.
-
Environmental and Operational Considerations:
- The SPS process operates in a vacuum or controlled atmosphere, which prevents oxidation and ensures material purity.
- This controlled environment is essential for producing high-quality materials with consistent properties.
- The process is also characterized by its high thermal efficiency, which contributes to its rapid and energy-efficient operation.
In summary, the SPS process is a highly efficient and versatile sintering technique that leverages the combination of pressure, pulsed electric current, and localized heating to achieve rapid densification of materials. Its ability to produce materials with unique properties at lower temperatures and shorter processing times makes it a valuable tool in advanced material fabrication.
Summary Table:
Key Aspect | Details |
---|---|
Process Overview | Combines pressure and pulsed electric current for rapid material densification. |
Key Stages | 1. Gas removal and vacuum creation 2. Pressure application 3. Resistive heating 4. Cooling |
Advantages | - High heating rates - Low sintering temperatures - Precise control of parameters |
Applications | Aerospace, automotive, biomedical industries |
Environmental Benefits | Operates in vacuum/controlled atmosphere, ensuring material purity and efficiency. |
Ready to explore how Spark Plasma Sintering can revolutionize your material fabrication? Contact our experts today!