The melting point of PVD (Physical Vapor Deposition) itself is not a fixed value because PVD is a process, not a material. Instead, PVD can deposit materials with a wide range of melting points, up to 3500 °C. The process involves creating a physical vapor of the material to be deposited, which then condenses onto a substrate in a vacuum environment. The properties of the resulting PVD coating, such as wear resistance, corrosion resistance, and hardness, depend on the material used and the substrate it is applied to. PVD coatings are known for their durability, thinness, and ability to replicate finishes with minimal effort.
Key Points Explained:
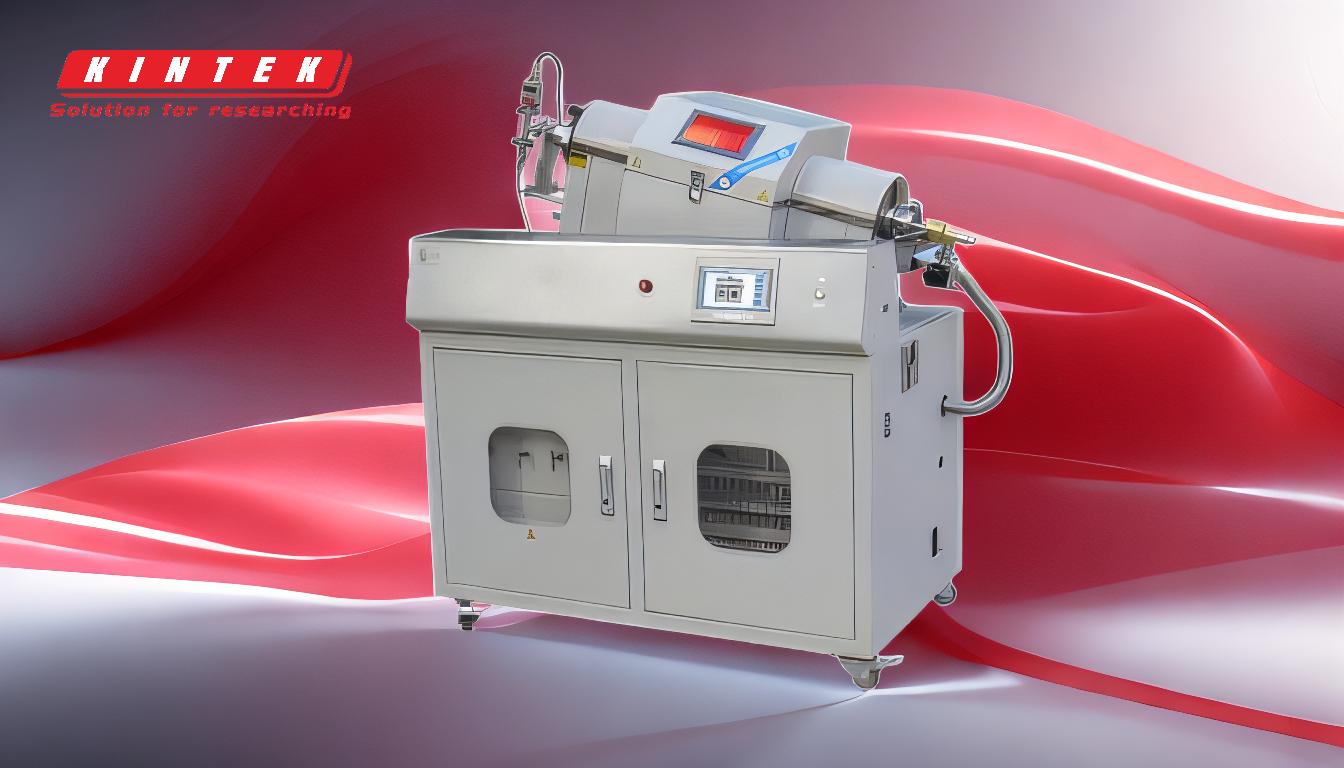
-
PVD is a process, not a material:
- PVD (Physical Vapor Deposition) is a method used to deposit thin films of materials onto a substrate. It is not a material itself, so it does not have a melting point. Instead, the materials used in PVD can have melting points up to 3500 °C.
-
Materials used in PVD can have high melting points:
- The reference states that PVD deposition tools can deposit monolayers of virtually any material, including those with melting points as high as 3500 °C. This means that the process is versatile and can handle materials that are extremely heat-resistant.
-
PVD process involves creating a physical vapor:
- The PVD process involves generating a physical vapor of the material to be deposited. This is typically done in a vacuum chamber, where the material is vaporized and then condenses onto the substrate to form a thin, uniform coating.
-
Properties of PVD coatings:
- PVD coatings are known for their excellent properties, including high wear resistance, corrosion resistance, and chemical resistance. They are also very hard, uniform, and durable, with a low coefficient of friction and excellent adhesion.
-
Dependence on substrate material:
- The properties of PVD coatings are influenced by the substrate material. For example, a TiN (Titanium Nitride) coating can significantly improve the fatigue limit and endurance of a Ti-6Al-4V alloy. The hardness of the coating is a critical factor in determining its durability and performance.
-
Comparison with CVD (Chemical Vapor Deposition):
- PVD films are generally more wear-resistant and have higher compressive stress compared to CVD films. Additionally, PVD coatings can be deposited at lower temperatures, which can be advantageous for certain applications.
In summary, while PVD itself does not have a melting point, it is a versatile process capable of depositing materials with extremely high melting points, up to 3500 °C. The resulting coatings are highly durable, resistant to wear and corrosion, and can be tailored to specific applications based on the substrate material and the properties of the coating material.
Summary Table:
Key Aspect | Details |
---|---|
PVD Nature | A process, not a material; no fixed melting point. |
Material Melting Points | Can deposit materials with melting points up to 3500 °C. |
Process | Creates a physical vapor in a vacuum, condensing onto a substrate. |
Coating Properties | High wear resistance, corrosion resistance, hardness, and durability. |
Substrate Dependence | Coating properties vary based on substrate material. |
Comparison with CVD | More wear-resistant, higher compressive stress, lower deposition temps. |
Unlock the potential of PVD coatings for your applications—contact us today for expert guidance!