Induction furnaces are widely used in industrial applications for heating and melting metals due to their efficiency, precision, and environmental friendliness. The power of an induction furnace is a critical factor that determines its performance, capacity, and suitability for specific tasks. The power rating of induction furnaces typically ranges from 15 kW to 90 kW for compact models, but this can vary based on the application, material type, and desired outcomes. The power consumption for steel induction furnaces, for example, is around 625 kWh/ton. Several factors influence the power requirements, including the material being processed, heating time, productivity, temperature, and the weight of the workpiece. Advanced features like IGBT frequency conversion, comprehensive protection systems, and efficient heat transmission further enhance the furnace's performance, making it a versatile and reliable tool for industrial processes.
Key Points Explained:
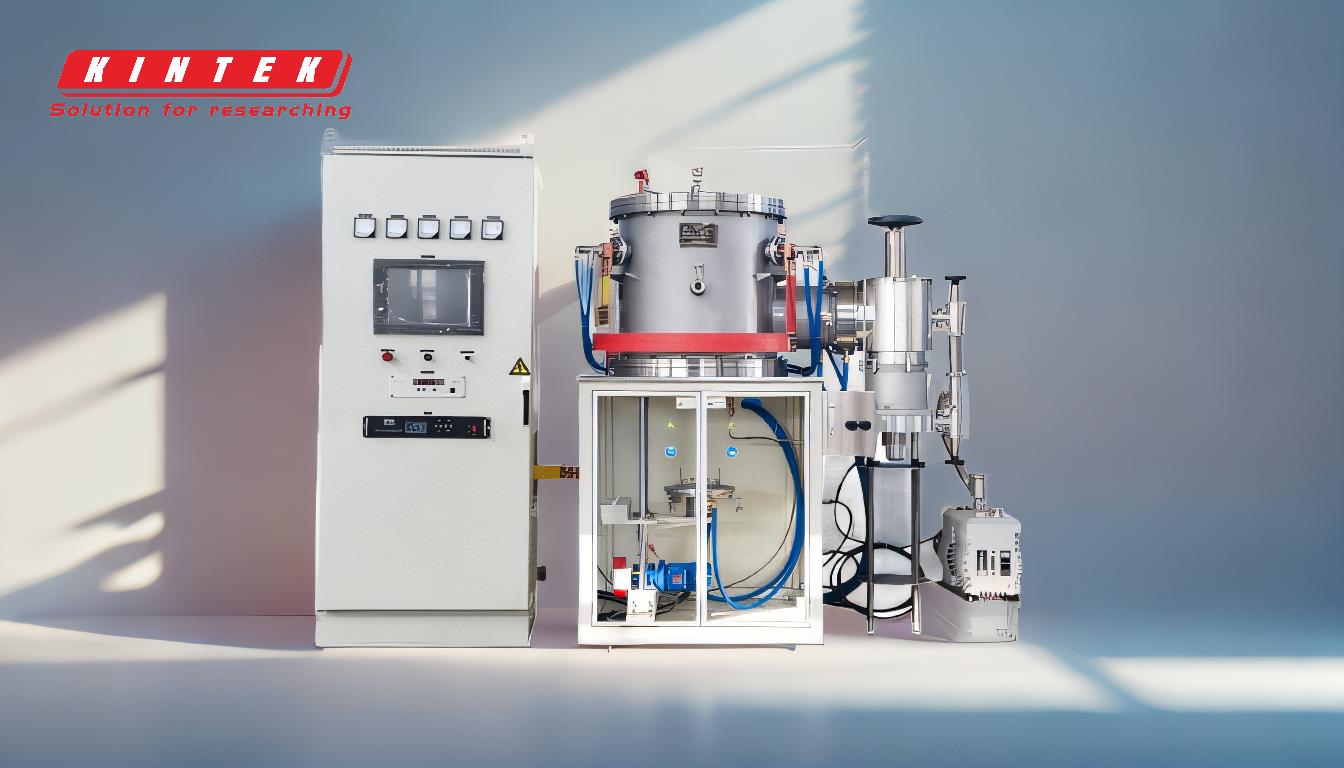
-
Power Range of Induction Furnaces
- Induction furnaces typically have a power rating ranging from 15 kW to 90 kW for compact models. This range is suitable for small to medium-scale operations, such as melting metals or heating workpieces.
- The power rating is directly related to the furnace's capacity and efficiency. Higher power ratings enable faster heating and melting, making them ideal for high-productivity environments.
-
Factors Influencing Power Calculation
- The power required for an induction furnace depends on several factors:
- Material Type: Different materials have varying thermal properties, affecting the energy needed for heating or melting.
- Heating Time: Faster heating requires higher power input.
- Productivity: High-throughput operations demand more power to maintain consistent output.
- Heating Temperature: Higher temperatures, such as 1800°C for melting, require more power.
- Workpiece Weight: Larger or heavier workpieces need more energy to achieve the desired temperature.
- These factors are based on years of industrial experience to ensure accurate power calculations and optimal furnace performance.
- The power required for an induction furnace depends on several factors:
-
Standard Power Consumption
- For steel induction furnaces, the standard power consumption is 625 kWh/ton. This metric provides a benchmark for energy efficiency and helps in estimating operational costs.
- Power-saving features, such as IGBT frequency conversion and constant power circuit control systems, contribute to reducing energy consumption while maintaining uniform smelting and heating.
-
Advanced Features Enhancing Power Efficiency
- IGBT Frequency Conversion: Modern induction furnaces use solid-state IGBT technology for efficient power regulation and frequency conversion. This ensures stable operation and reduces energy waste.
- Comprehensive Protection Systems: Features like overcurrent, water shortage, overheating, overvoltage, short circuit, and phase loss protection enhance safety and reliability.
- Heat Transmission and Uniformity: The furnace ensures good heat transmission and uniform temperature distribution, minimizing energy loss and improving process efficiency.
- Magnetic Stirring: The medium-frequency magnetic field provides magnetic stirring, which improves composition uniformity and scum removal, further enhancing efficiency.
-
Operational Efficiency and Flexibility
- Induction furnaces are designed for 24-hour continuous smelting, making them suitable for high-demand industrial applications.
- They are lightweight, movable, and compact, covering less than one square meter, which makes them easy to integrate into existing setups.
- Furnace bodies can be easily replaced to accommodate different weights, materials, and starting methods, providing flexibility for various applications.
-
Temperature Capabilities
- Induction furnaces can reach temperatures of 1800°C or more, depending on the inductive coupling of the coil with the charge materials. This makes them suitable for melting a wide range of metals, including those with high melting points.
- The forging heating temperature can reach 1250°C, while the melting temperature can reach 1650°C, ensuring versatility for different industrial processes.
-
Energy Efficiency and Environmental Benefits
- Induction furnaces are power-saving and environmentally friendly, reducing operational costs and minimizing environmental impact.
- Features like constant power circuit control systems and automatic frequency scanning ensure smooth and stable operation, further enhancing energy efficiency.
-
Design and Maintenance Advantages
- The high integrated circuit design simplifies debugging and operation, making the furnace user-friendly.
- Components in the power supply cabinet, such as AC contactors, silicon-controlled rectifiers, and inverter boards, are well-coordinated, ensuring easy maintenance and long-term reliability.
-
Application-Specific Considerations
- The melting rate and power configuration of the medium-frequency power supply are critical for achieving desired outcomes.
- Using a clean charge and appropriate furnace block length improves efficiency, while suitable refractory materials, such as quartz crucibles, reduce heat transfer consumption.
In conclusion, the power of an induction furnace is a key determinant of its performance, efficiency, and suitability for specific industrial applications. By understanding the factors influencing power requirements and leveraging advanced features, users can optimize furnace operation, reduce costs, and achieve consistent, high-quality results.
Summary Table:
Key Aspect | Details |
---|---|
Power Range | 15 kW to 90 kW for compact models |
Power Consumption (Steel) | 625 kWh/ton |
Temperature Capabilities | Up to 1800°C for melting, 1250°C for forging |
Advanced Features | IGBT frequency conversion, magnetic stirring, comprehensive protection systems |
Operational Efficiency | 24-hour continuous smelting, lightweight, and compact design |
Energy Efficiency | Power-saving, environmentally friendly, and reduced operational costs |
Ready to optimize your industrial heating process? Contact us today to find the perfect induction furnace for your needs!