The pressing process of ceramics is a critical step in the fabrication of ceramic components, particularly in dental and industrial applications. It involves transforming ceramic powder into a solid, dense form through the application of heat and pressure. The process requires precise control of time and temperature, as well as proper burnout of the ceramic material to ensure the final product is free of defects and has the desired properties. Key steps include preparing the ceramic ingot, placing it in a pressing furnace, and using a plunger to apply pressure. The success of the process depends on careful attention to detail at every stage.
Key Points Explained:
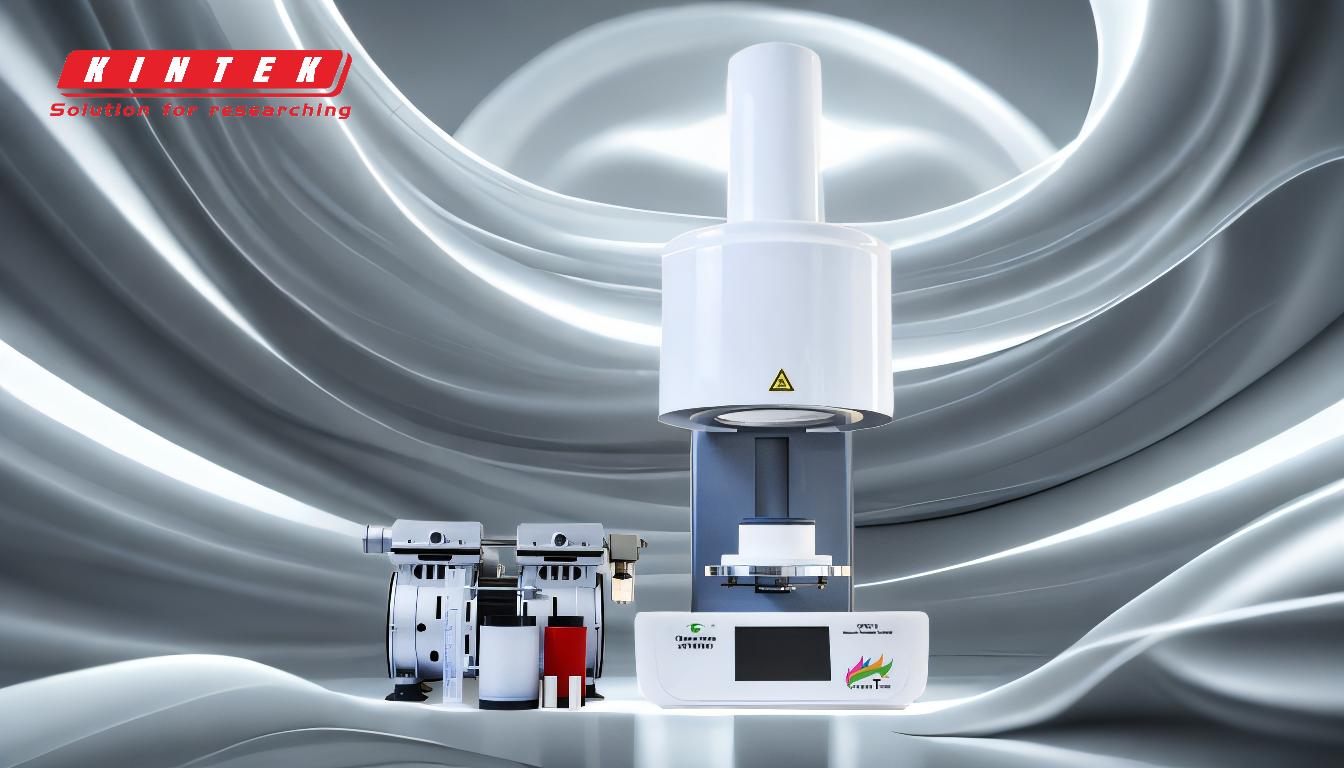
-
Preparation of Ceramic Ingot:
- The ceramic ingot, which is typically a pre-sintered or pre-compacted form of ceramic powder, is prepared for pressing. This involves ensuring the ingot is free of contaminants and has the correct dimensions for the pressing furnace.
-
Insertion into the Pressing Furnace:
- The ingot is placed into the pressing furnace, which is designed to apply both heat and pressure. The furnace must be preheated to the appropriate temperature to ensure the ceramic material can flow and fill the mold properly.
-
Application of Pressure:
- A plunger is used to apply pressure to the ceramic ingot within the furnace. The pressure helps to compact the ceramic particles, reducing porosity and increasing the density of the final product. The amount of pressure applied is critical and must be carefully controlled to avoid cracking or other defects.
-
Burnout Process:
- Burnout is a crucial step where any organic binders or additives used in the ceramic powder are removed through controlled heating. This process must be carefully managed to prevent the formation of voids or cracks in the ceramic. The burnout schedule, including time and temperature, is tailored to the specific ceramic material being used.
-
Cooling and Removal:
- After pressing, the ceramic component is allowed to cool slowly within the furnace to prevent thermal shock, which could lead to cracking. Once cooled, the component is removed from the furnace and inspected for quality.
-
Quality Control:
- The final step involves a thorough inspection of the pressed ceramic component. This includes checking for dimensional accuracy, surface finish, and any potential defects such as cracks or voids. Any issues identified during this stage may require adjustments to the pressing process parameters.
By following these steps meticulously, the pressing process of ceramics can produce high-quality components with the desired mechanical and aesthetic properties. The process is highly dependent on the precise control of temperature, pressure, and time, making it both an art and a science.
Summary Table:
Step | Description |
---|---|
1. Preparation | Clean and dimension ceramic ingot for pressing. |
2. Insertion | Place ingot into preheated pressing furnace for heat and pressure application. |
3. Pressure | Use a plunger to compact ceramic particles, ensuring density and avoiding cracks. |
4. Burnout | Remove organic binders with controlled heating to prevent defects. |
5. Cooling | Allow slow cooling to avoid thermal shock and cracking. |
6. Quality Control | Inspect for dimensional accuracy, surface finish, and defects. |
Need expert guidance on ceramic pressing? Contact us today for tailored solutions!