A mechanical forging press operates on the principle of converting rotational energy into linear force to shape metal. This is achieved through a flywheel that stores energy, which is then transferred to a ram via a crank mechanism. The ram applies significant pressure, up to 12,000 tons, to deform and shape metal workpieces. This process is essential in industries requiring high-strength metal components, such as automotive and aerospace manufacturing.
Key Points Explained:
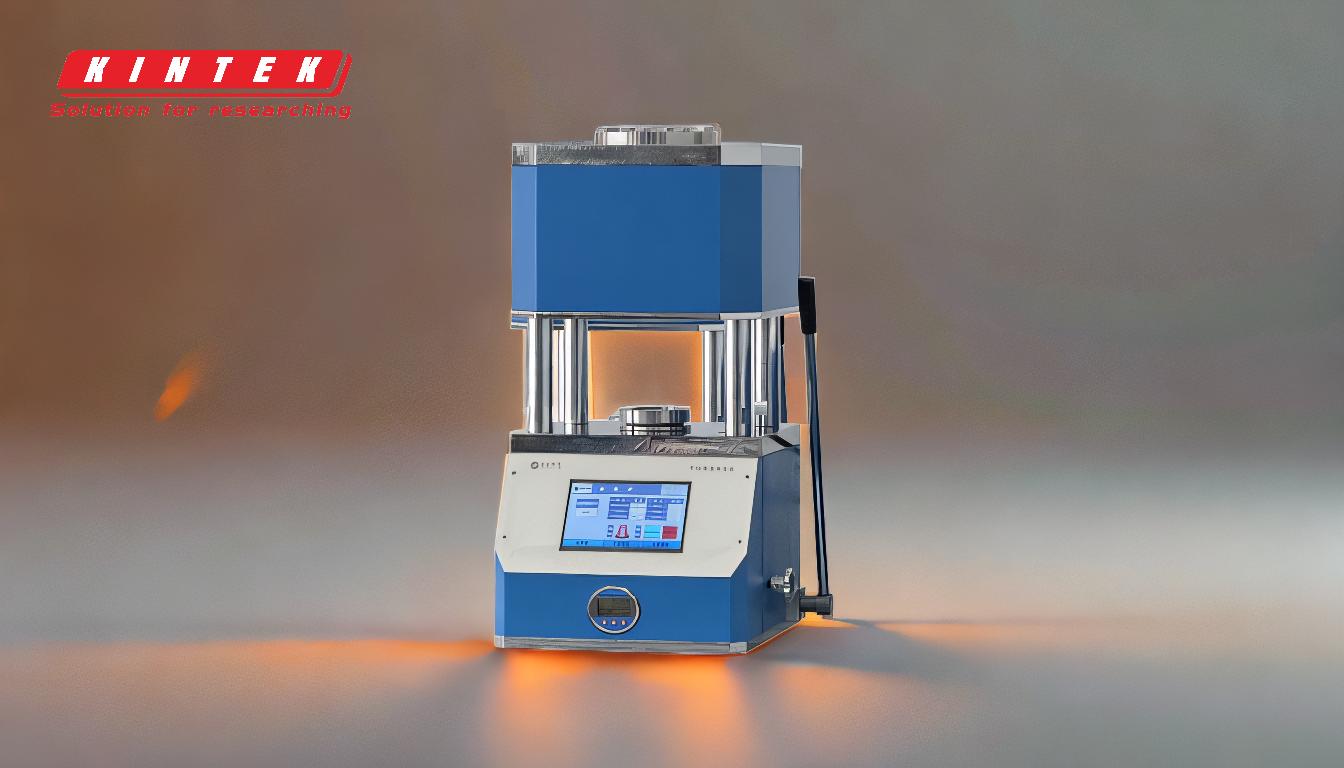
-
Energy Storage in the Flywheel:
- The flywheel is a critical component that stores rotational energy. When the press is activated, the flywheel's stored energy is harnessed to drive the press's operations.
- This energy storage mechanism ensures a consistent and powerful force application, which is crucial for effective forging.
-
Crank Mechanism:
- The crank mechanism translates the rotational motion of the flywheel into linear motion of the ram.
- This conversion is essential for applying the necessary force to the metal workpiece, allowing for precise shaping and deformation.
-
Ram Movement and Force Application:
- The ram, driven by the crank mechanism, moves vertically to apply pressure to the workpiece.
- The ability to apply up to 12,000 tons of pressure makes mechanical forging presses suitable for creating high-strength metal components.
-
Applications in Industry:
- Mechanical forging presses are widely used in industries that require robust and durable metal parts, such as automotive, aerospace, and heavy machinery manufacturing.
- The high force application ensures that the metal is thoroughly deformed, resulting in components with superior mechanical properties.
-
Advantages of Mechanical Forging Presses:
- High Force Application: Capable of applying up to 12,000 tons of pressure, these presses can handle large and complex metal workpieces.
- Precision and Consistency: The mechanical linkage ensures precise control over the ram's movement, leading to consistent and repeatable results.
- Durability: The robust construction of mechanical forging presses makes them suitable for high-volume production environments.
By understanding these key points, one can appreciate the efficiency and effectiveness of mechanical forging presses in industrial applications. The combination of energy storage, mechanical linkage, and high force application makes these presses indispensable in the manufacturing of high-strength metal components.
Summary Table:
Key Component | Function |
---|---|
Flywheel | Stores rotational energy for consistent force application. |
Crank Mechanism | Converts rotational motion into linear motion of the ram. |
Ram | Applies up to 12,000 tons of pressure to shape metal workpieces. |
Applications | Automotive, aerospace, and heavy machinery manufacturing. |
Advantages | High force, precision, consistency, and durability. |
Discover how mechanical forging presses can transform your manufacturing process—contact us today!