The process of a crucible furnace involves heating materials, typically metals with low melting points like brass, bronze, or aluminum, inside a crucible until they reach their melting point. The furnace uses a fuel source such as natural gas, propane, or electricity to generate heat, which is transferred to the crucible. Once the material melts, it is poured into molds or containers to achieve the desired shape. The process can be controlled through temperature adjustments, and factors like furnace size and design influence melting efficiency and time. Crucible furnaces are widely used in small-scale production and for creating alloys with specific properties.
Key Points Explained:
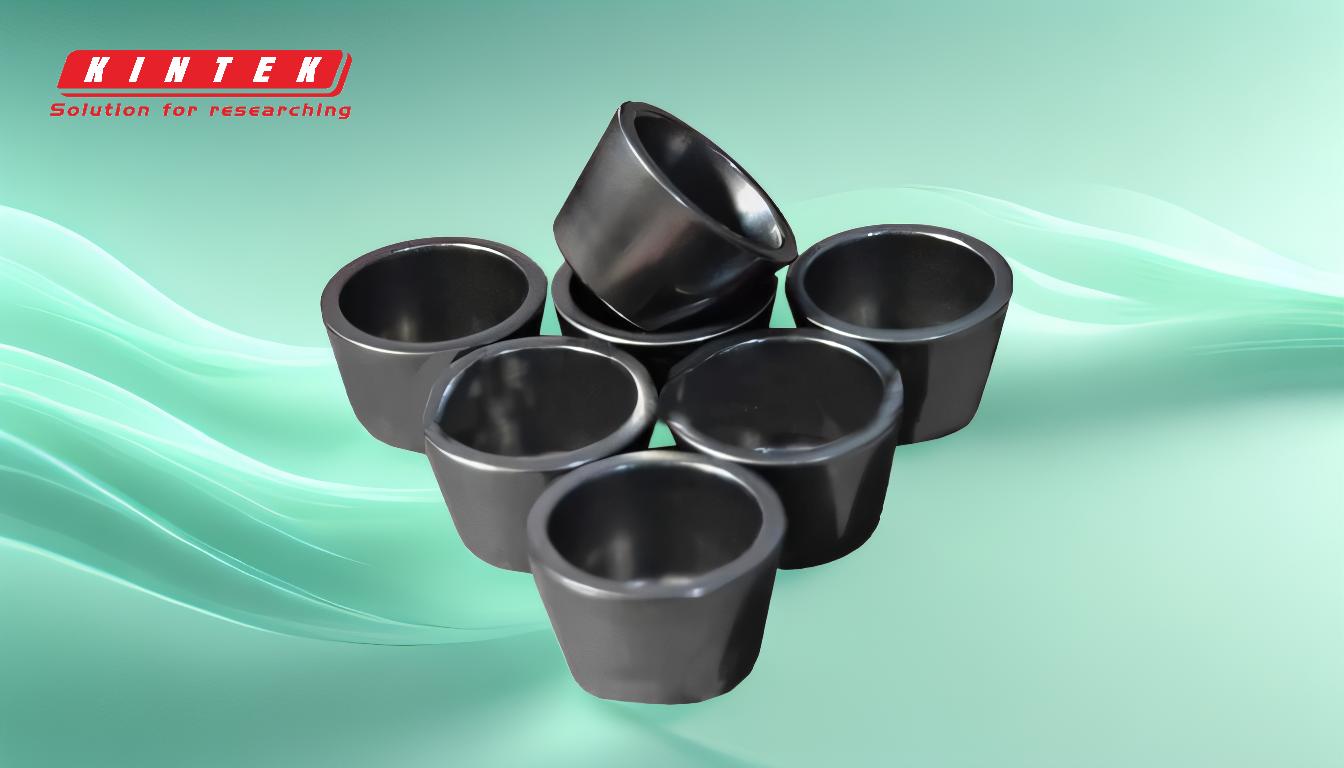
-
Purpose of a Crucible Furnace:
- Crucible furnaces are primarily used for melting and casting metals with low melting points, such as brass, bronze, and aluminum.
- They are ideal for small-scale production and for creating alloys with specific properties.
- These furnaces are one of the oldest types of melting ovens and remain widely used in the metallurgy industry.
-
Components of a Crucible Furnace:
- Crucible: A container made of refractory material that holds the metal or material to be melted.
- Furnace Chamber: The outer structure, also made of refractory material, which houses the crucible and withstands high temperatures.
- Heating Element: The source of heat, which can be fueled by natural gas, propane, or electricity.
- Temperature Control System: Optional equipment to regulate and maintain the desired temperature.
-
Heating Process:
- The heating element generates heat, which is transferred to the crucible.
- The crucible absorbs the heat and transfers it to the material inside, raising its temperature until it reaches the melting point.
- The furnace chamber, made of refractory material, ensures that heat is contained efficiently and safely.
-
Melting and Pouring:
- Once the material inside the crucible reaches its melting point, it becomes molten.
- The molten material is then poured into molds or containers to form the desired shape.
- This step is critical for casting processes and requires precision to achieve accurate results.
-
Control and Efficiency:
- The melting process can be controlled by adjusting the heat output or using a temperature control system.
- Factors such as the size and design of the furnace can impact the melting time and overall efficiency.
- Proper control ensures consistent results and minimizes energy waste.
-
Applications:
- Crucible furnaces are commonly used in metallurgy for small-scale production and specialized alloy creation.
- They are particularly useful for melting metals with low melting points and for applications requiring precise control over the melting process.
-
Advantages of Crucible Furnaces:
- Versatility: Suitable for a wide range of metals and alloys.
- Simplicity: Easy to operate and maintain compared to more complex furnace types.
- Cost-Effectiveness: Ideal for small-scale operations where large-scale furnaces may not be economical.
By understanding these key points, a purchaser can evaluate whether a crucible furnace meets their specific needs, considering factors like material type, production scale, and desired control over the melting process.
Summary Table:
Aspect | Details |
---|---|
Purpose | Melting and casting metals with low melting points (e.g., brass, aluminum). |
Components | Crucible, furnace chamber, heating element, temperature control system. |
Heating Process | Heat transferred to crucible, melting the material inside. |
Melting and Pouring | Molten material poured into molds for shaping. |
Control and Efficiency | Adjustable heat output, size, and design impact efficiency. |
Applications | Small-scale production, alloy creation, precise melting control. |
Advantages | Versatile, simple to operate, cost-effective for small-scale operations. |
Discover how a crucible furnace can meet your metal melting needs—contact us today for expert advice!