Deposition precipitation is a process used in thin film deposition techniques, where a target material is transported and deposited onto a substrate to form a thin film. This process typically involves several key steps, including selecting a pure material source, transporting the target material to the substrate through a medium (such as a fluid or vacuum), depositing the material onto the substrate, and optionally subjecting the film to post-deposition treatments like annealing. The quality and properties of the thin film, such as thickness uniformity and deposition rate, are influenced by factors like target-substrate distance, power, temperature, and the size of the erosion zone. This process is crucial for achieving desired thin film characteristics in various applications.
Key Points Explained:
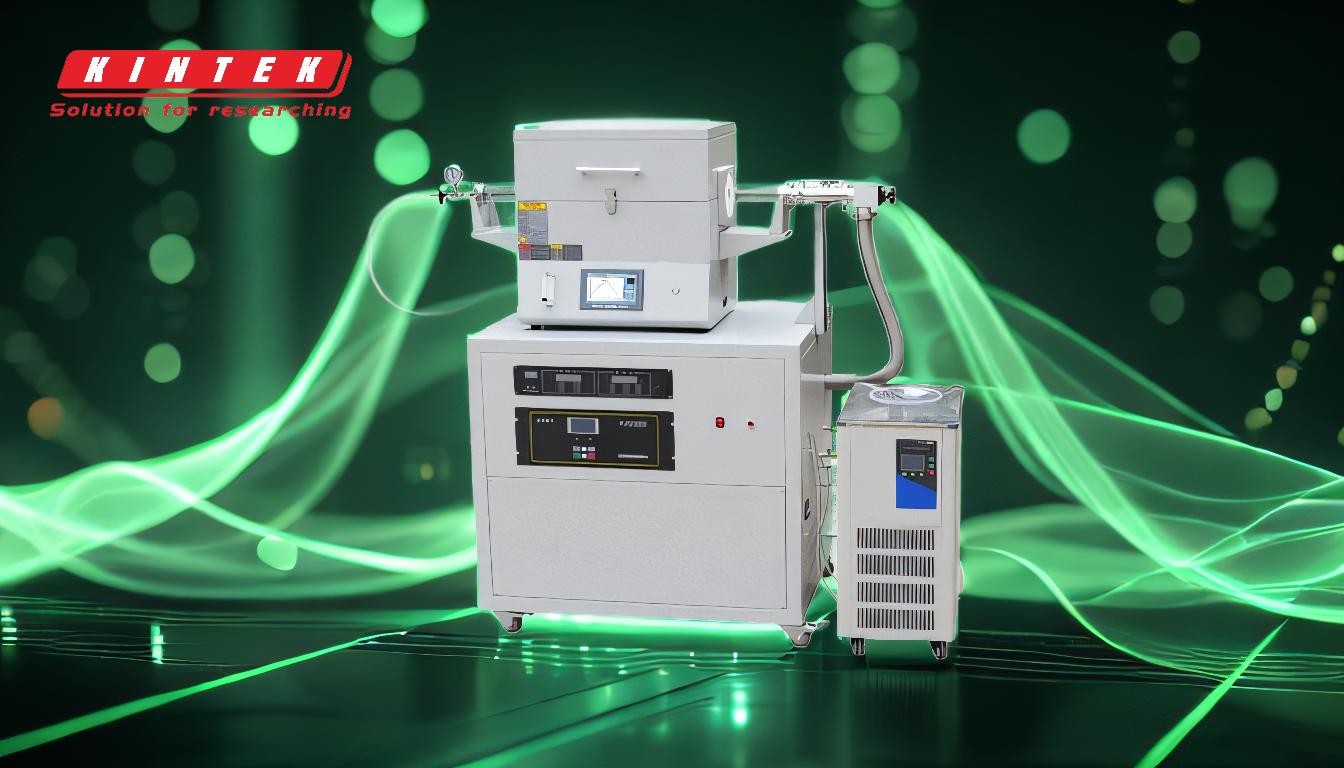
-
Selection of Pure Material Source (Target):
- The process begins with choosing a high-purity material source, known as the target. This material is crucial as it determines the composition and properties of the thin film. For instance, in sputtering deposition, the target material is bombarded by high-energy ions of argon gas, which removes its molecules and deposits them onto the substrate.
-
Transport of Target Material to Substrate:
- The target material is transported to the substrate through a medium, which can be a fluid or a vacuum. In sputtering deposition, the medium is typically a vacuum, which allows for the efficient transfer of the target material to the substrate without contamination.
-
Deposition of Target Material onto Substrate:
- The target material is deposited onto the substrate to form a thin film. This step is critical as it directly affects the film's thickness, uniformity, and overall quality. The deposition rate, which is influenced by factors such as the size of the erosion zone, magnetron power, and target material, plays a significant role in determining the film's characteristics.
-
Post-Deposition Treatments (Optional):
- After deposition, the thin film may undergo post-deposition treatments such as annealing or heat treatment. These treatments can improve the film's properties, such as its crystallinity, adhesion, and mechanical strength. Annealing, for example, can help to reduce defects and improve the film's overall quality.
-
Analysis and Modification of Deposition Process:
- The final step involves analyzing the properties of the thin film and, if necessary, modifying the deposition process to achieve the desired characteristics. This may include adjusting parameters such as target-substrate distance, power, and temperature to optimize the deposition rate and thickness uniformity.
-
Factors Influencing Deposition Rate and Thickness Uniformity:
- The deposition rate and thickness uniformity are influenced by several factors:
- Target-Substrate Distance: Increasing the distance between the target and substrate decreases thickness uniformity and the deposition rate.
- Power and Temperature: Higher power and temperature can increase the deposition rate, while lower power and higher gas temperature can decrease the thickness of the thin layer.
- Erosion Zone Size: A larger erosion zone can improve deposition rate and thickness uniformity.
- The deposition rate and thickness uniformity are influenced by several factors:
By carefully controlling these factors, the deposition precipitation process can be optimized to produce high-quality thin films with the desired properties for various applications.
Summary Table:
Step | Description |
---|---|
1. Selection of Pure Material Source | Choose a high-purity target material to determine the thin film's properties. |
2. Transport of Target Material | Move the target material to the substrate via a medium (e.g., fluid or vacuum). |
3. Deposition onto Substrate | Deposit the material onto the substrate to form a thin film. |
4. Post-Deposition Treatments | Optional treatments like annealing to enhance film properties. |
5. Analysis and Modification | Analyze the film and adjust parameters for optimal results. |
6. Influencing Factors | Target-substrate distance, power, temperature, and erosion zone size affect results. |
Optimize your thin film deposition process—contact our experts today!