Sintering glass is a process that transforms powdered glass into a dense, solid form by applying heat and pressure without reaching the material's melting point. This method is widely used in manufacturing to create durable and strong glass components. The process typically involves preparing a powder compact, heating it in a controlled atmosphere to allow particle fusion, and cooling it to form a unified mass. Key steps include composition, compression, and heat application, which ensure the removal of coupling agents and the fusion of primary materials into a low-porosity structure. Sintering is particularly useful for materials with high melting points and is essential in industries like ceramics and powder metallurgy.
Key Points Explained:
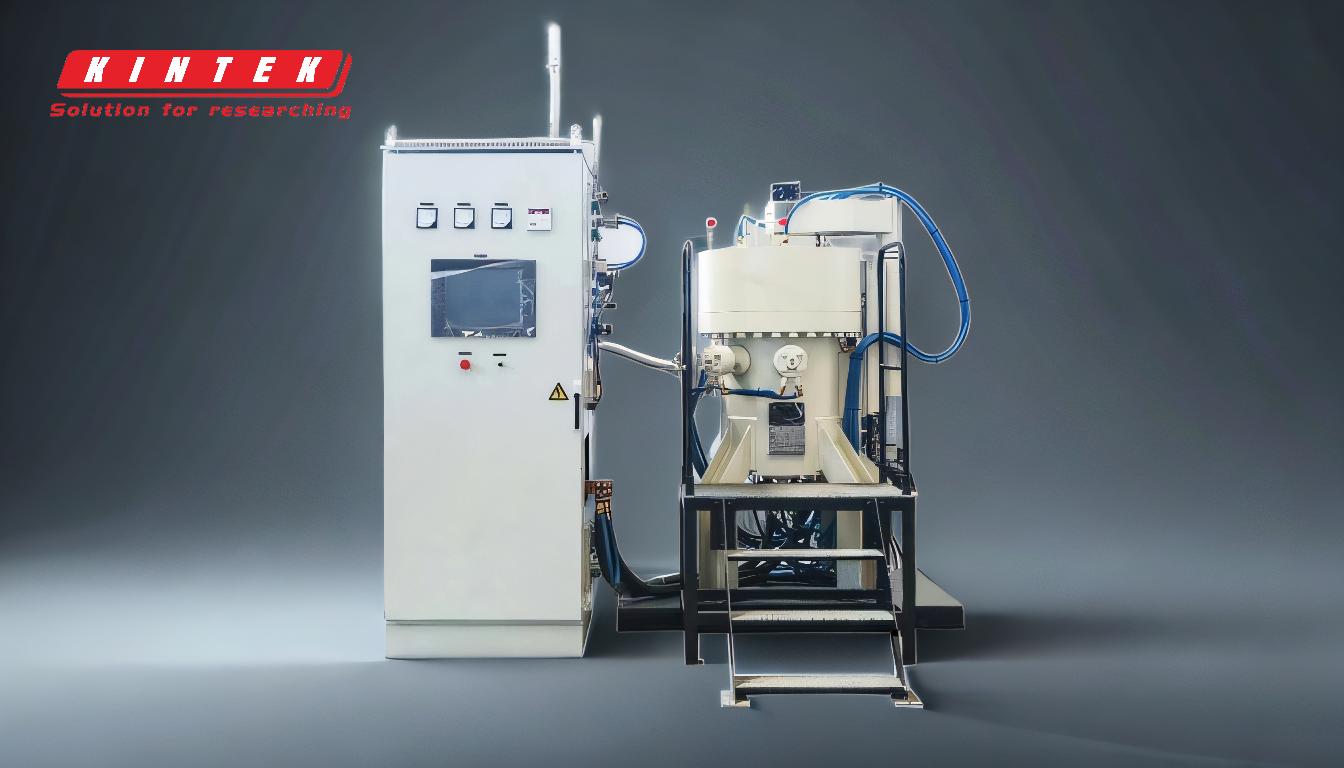
-
Preparation of Powder Compact:
- Process: The first step involves preparing a powder compact from finely powdered glass. This can be done using methods like cold welds, 3D-printed lasers, or pressing tools in a controlled atmosphere.
- Details: The powder is mixed with primary materials and coupling agents to ensure uniformity. The mixture is then pressed into a desired shape using a graphite mould, which also supports any metal parts if present.
-
Application of Heat and Pressure:
- Process: The shaped powder compact is subjected to high heat and pressure in a controlled atmosphere, typically a mixed nitrogen-hydrogen environment, using high-frequency induction heating.
- Details: The temperature is carefully controlled to remain below the melting point of the glass to prevent liquefaction. This stage allows the bonding agent to evaporate or burn away, leaving the primary particles to begin fusing at their surfaces.
-
Particle Fusion and Densification:
- Process: As the temperature rises, the primary particles heat enough to just begin to melt, causing individual particles to fuse at their surfaces. Alternatively, an intermediate bonding agent such as bronze may melt and couple between the particles.
- Details: This stage involves material migration and grain boundary movement under high temperature, leading to the gradual densification of the ceramic materials. Over time, the materials form a porcelain body with a certain strength.
-
Cooling and Solidification:
- Process: After sufficient particle fusion, the material is allowed to cool and solidify into a unified mass.
- Details: The cooling process must be controlled to prevent thermal stresses that could lead to cracking or warping. The final product is a dense, low-porosity glass component with enhanced mechanical properties.
-
Controlled Atmosphere:
- Process: Throughout the sintering process, a controlled atmosphere is maintained to prevent oxidation and other unwanted chemical reactions.
- Details: The use of a mixed nitrogen-hydrogen atmosphere is crucial for achieving the desired material properties and ensuring the integrity of the final product.
-
Applications and Benefits:
- Process: Sintering is used in various industries, including ceramics and powder metallurgy, to produce components with high strength and durability.
- Details: The process is particularly beneficial for materials with extremely high melting points, such as tungsten and molybdenum, where traditional melting and casting methods are impractical.
By following these steps, the sintering process effectively transforms powdered glass into a dense, durable, and high-performance material suitable for a wide range of industrial applications.
Summary Table:
Step | Process | Details |
---|---|---|
1. Preparation of Powder Compact | Powder is mixed with primary materials and coupling agents, then pressed into shape. | Ensures uniformity and supports metal parts using a graphite mould. |
2. Application of Heat and Pressure | High heat and pressure are applied in a controlled atmosphere. | Temperature stays below melting point to prevent liquefaction; bonding agents evaporate. |
3. Particle Fusion and Densification | Particles fuse at surfaces or through intermediate bonding agents like bronze. | Material migration and grain boundary movement lead to densification and porcelain formation. |
4. Cooling and Solidification | Material cools and solidifies into a unified mass. | Controlled cooling prevents cracking or warping, resulting in a dense, low-porosity structure. |
5. Controlled Atmosphere | Mixed nitrogen-hydrogen atmosphere is maintained. | Prevents oxidation and ensures desired material properties. |
6. Applications and Benefits | Used in ceramics and powder metallurgy for high-strength components. | Ideal for materials with high melting points like tungsten and molybdenum. |
Discover how sintering glass can enhance your manufacturing process—contact our experts today!