Sintering is a thermal process that transforms powdered materials into solid objects without melting them completely. It involves heating the powder below its melting point, allowing atoms to diffuse across particle boundaries and fuse together. The process typically includes stages like powder preparation, compression, heating, and solidification. Factors such as temperature, pressure, particle size, and composition influence the sintering process, affecting the final material's density, strength, and structural integrity. Sintering is widely used in manufacturing ceramics, metals, and plastics, offering a cost-effective way to produce complex shapes with high precision.
Key Points Explained:
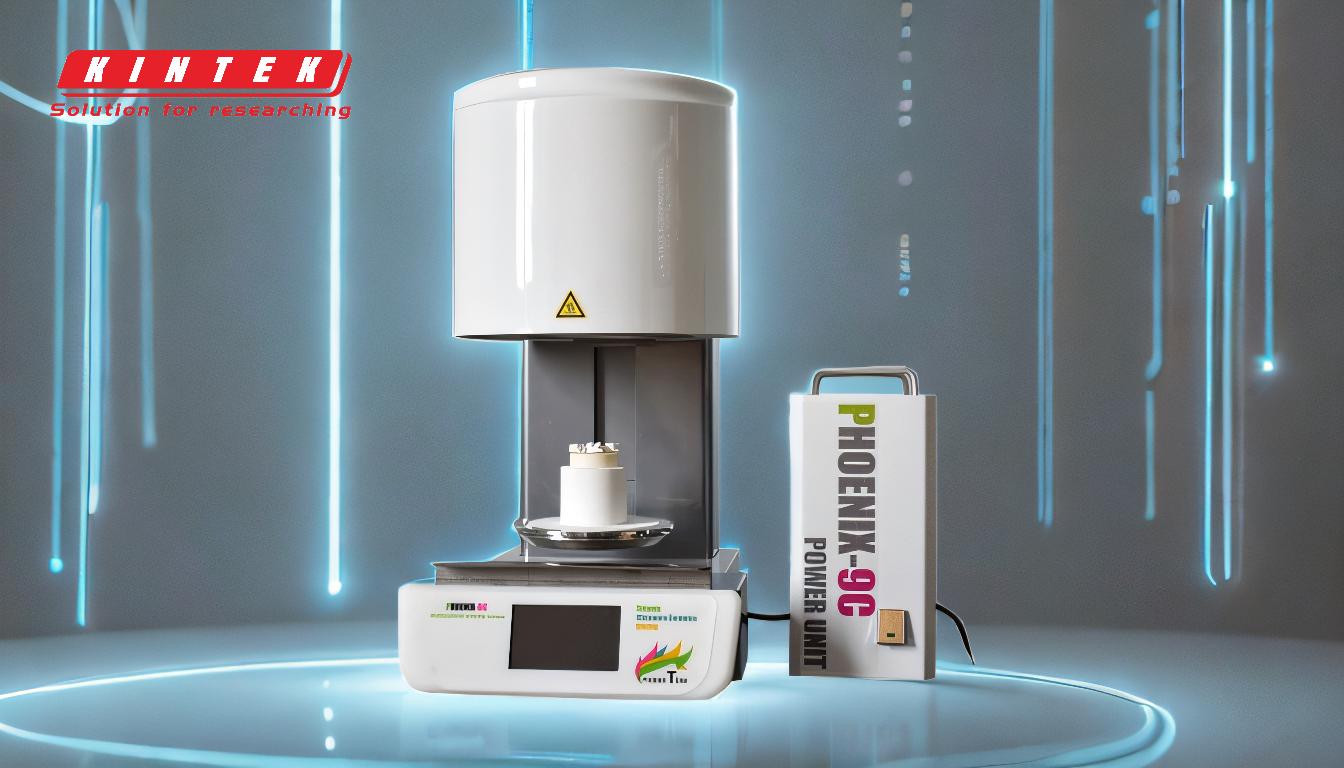
-
Definition and Purpose of Sintering:
- Sintering is a process that fuses powdered materials into a solid mass using heat and pressure, without melting the material completely.
- It is used to create objects with improved structural integrity, density, and strength, commonly in ceramics, metals, and plastics.
-
Stages of the Sintering Process:
- Powder Preparation: The raw material is ground into fine particles, often mixed with binders or coupling agents to improve handling and shaping.
- Compression: The powder is pressed into a desired shape using tools like molds or 3D-printed lasers. This step ensures the powder particles are closely packed.
- Heating: The compacted powder is heated in a furnace to a temperature just below its melting point. This activates atomic diffusion, allowing particles to bond.
- Solidification: After heating, the material cools and solidifies into a dense, unified mass with reduced porosity.
-
Key Factors Influencing Sintering:
- Temperature: Determines the rate of atomic diffusion and the final material properties. Higher temperatures accelerate sintering but must remain below the melting point.
- Heating Rate: Affects densification. A controlled heating rate ensures uniform bonding and minimizes defects.
- Pressure: Applied during compression to enhance particle rearrangement and eliminate porosity.
- Particle Size: Smaller particles have a larger surface area, promoting faster and more efficient sintering.
- Composition: Homogeneous mixtures of materials improve sintering behavior and final product quality.
-
Types of Sintering:
- Solid-State Sintering: Particles bond through atomic diffusion without melting. Common in ceramics and metals.
- Liquid Phase Sintering (LPS): A small amount of liquid phase forms, accelerating particle bonding. Often used in materials with low melting points.
- Pressure-Assisted Sintering: External pressure is applied during heating to enhance densification and reduce porosity.
-
Applications of Sintering:
- Ceramics: Used to produce high-strength, heat-resistant components like tiles, insulators, and cutting tools.
- Metals: Enables the production of complex metal parts with precise dimensions, such as gears, bearings, and automotive components.
- Plastics: Used to create durable, lightweight parts with intricate shapes, often in industries like aerospace and electronics.
-
Advantages of Sintering:
- Cost-Effective: Reduces material waste and energy consumption compared to melting processes.
- Complex Shapes: Allows the production of intricate designs that are difficult to achieve with traditional manufacturing methods.
- Material Properties: Enhances strength, density, and wear resistance of the final product.
-
Challenges and Considerations:
- Porosity Control: Achieving uniform density and minimizing voids can be challenging, especially in large or complex parts.
- Material Selection: Not all materials are suitable for sintering, and the process may require additives or binders.
- Process Optimization: Balancing temperature, pressure, and heating rate is critical to avoid defects like warping or cracking.
By understanding these key aspects, equipment and consumable purchasers can make informed decisions about sintering processes, ensuring the selection of appropriate materials and methods for their specific needs.
Summary Table:
Aspect | Details |
---|---|
Definition | Fuses powdered materials into solid objects using heat and pressure. |
Stages | Powder preparation, compression, heating, solidification. |
Key Factors | Temperature, heating rate, pressure, particle size, composition. |
Types | Solid-state, liquid phase, pressure-assisted sintering. |
Applications | Ceramics, metals, plastics for high-strength and complex shapes. |
Advantages | Cost-effective, enables intricate designs, enhances material properties. |
Challenges | Porosity control, material selection, process optimization. |
Ready to optimize your sintering process? Contact our experts today for tailored solutions!